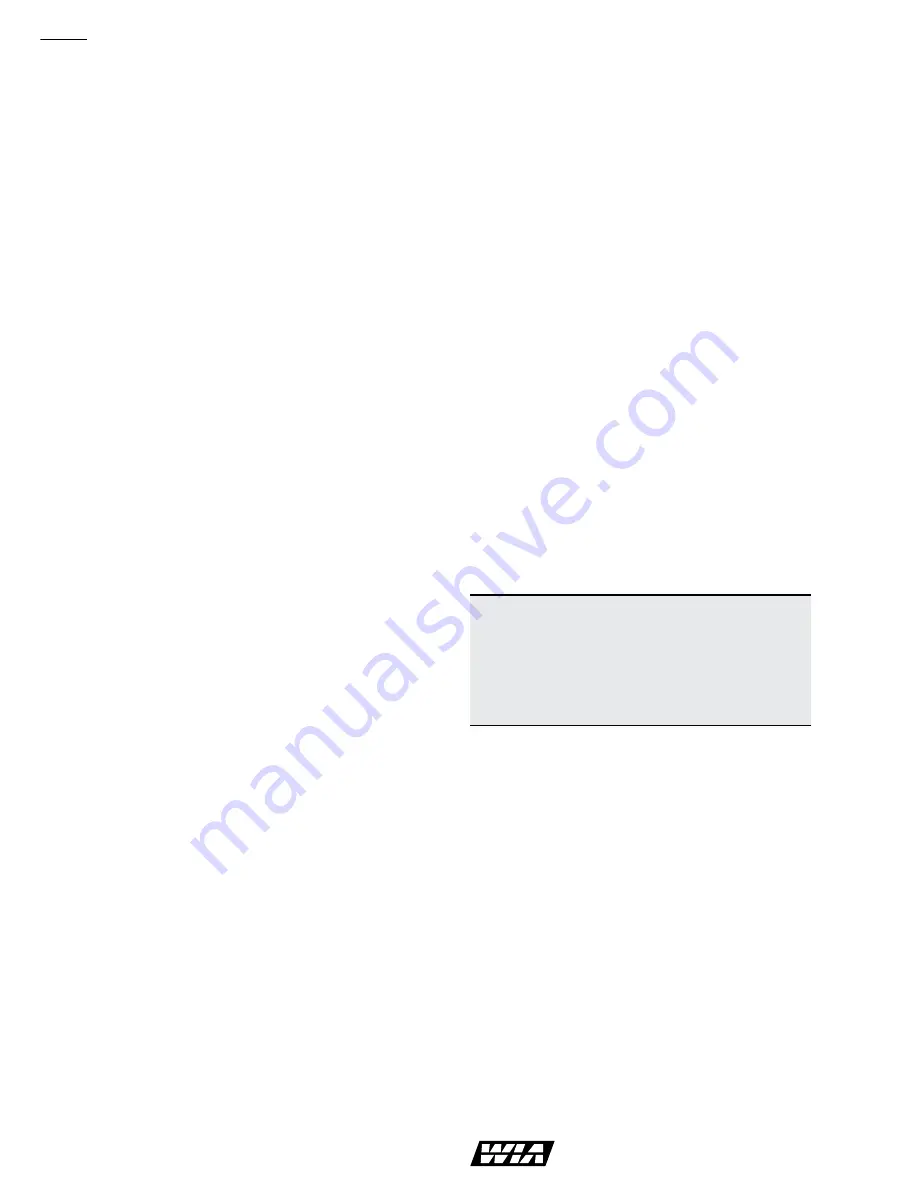
4
Operators Manual
Quality
•
Reliability
•
Performance
A person acting as Fire Watcher must be
standing by with suitable fire extinguishing
equipment during and for some time after
welding or cutting if;
• Combustibles (including building
construction) are within 10 metres.
• Combustibles are further than 10 metres
but can be ignited by sparks.
• Openings (concealed or visible) in floors
or walls within 10 metres may expose
combustibles to sparks.
• Combustibles adjacent to walls, ceilings,
roofs, or metal partitions can be ignited
by radiant or conducted heat.
After work is done, check that area is free of
sparks, glowing embers, and flames.
A tank or drum which has contained
combustibles can produce flammable
vapours when heated. Such a container must
never be welded on or cut, unless it has first
been cleaned as described in AS.1674-2.
This includes a thorough steam or caustic
cleaning (or a solvent or water washing,
depending on the combustible’s solubility),
followed by purging and inerting with nitrogen
or carbon dioxide, and using protective
equipment as recommended in AS.1674-2.
Water-filling just below working level may
substitute for inerting.
Hollow castings or containers must be
vented before welding or cutting. They can
explode. Never weld or cut where the air
may contain flammable dust, gas, or liquid
vapours.
Shock Prevention
Exposed conductors or other bare metal
in the welding circuit, or ungrounded
electrically alive equipment can fatally shock
a person whose body becomes a conductor.
Ensure that the equipment is correctly
connected and earthed. If unsure have the
equipment installed by a qualified electrician.
On mobile or portable equipment, regularly
inspect condition of trailing power leads and
connecting plugs. Repair or replace damaged
leads.
Fully insulated electrode holders should be
used. Do not use holders with protruding
screws. Fully insulated lock-type connectors
should be used to join welding cable lengths.
Terminals and other exposed parts of
electrical units should have insulated knobs
or covers secured before operation.
If the supply cable is damaged
it must be replaced by the
manufacturer, their service agent
or a similarly qualified person.
Содержание Weldmatic Fabricator P135-2
Страница 21: ...Weldmatic Fabricator Model No CP135 2 Iss A 02 12 19 Notes...
Страница 22: ...20 Operators Manual Quality Reliability Performance Notes...
Страница 23: ...Weldmatic Fabricator Model No CP135 2 Iss A 02 12 21 Notes...
Страница 24: ......