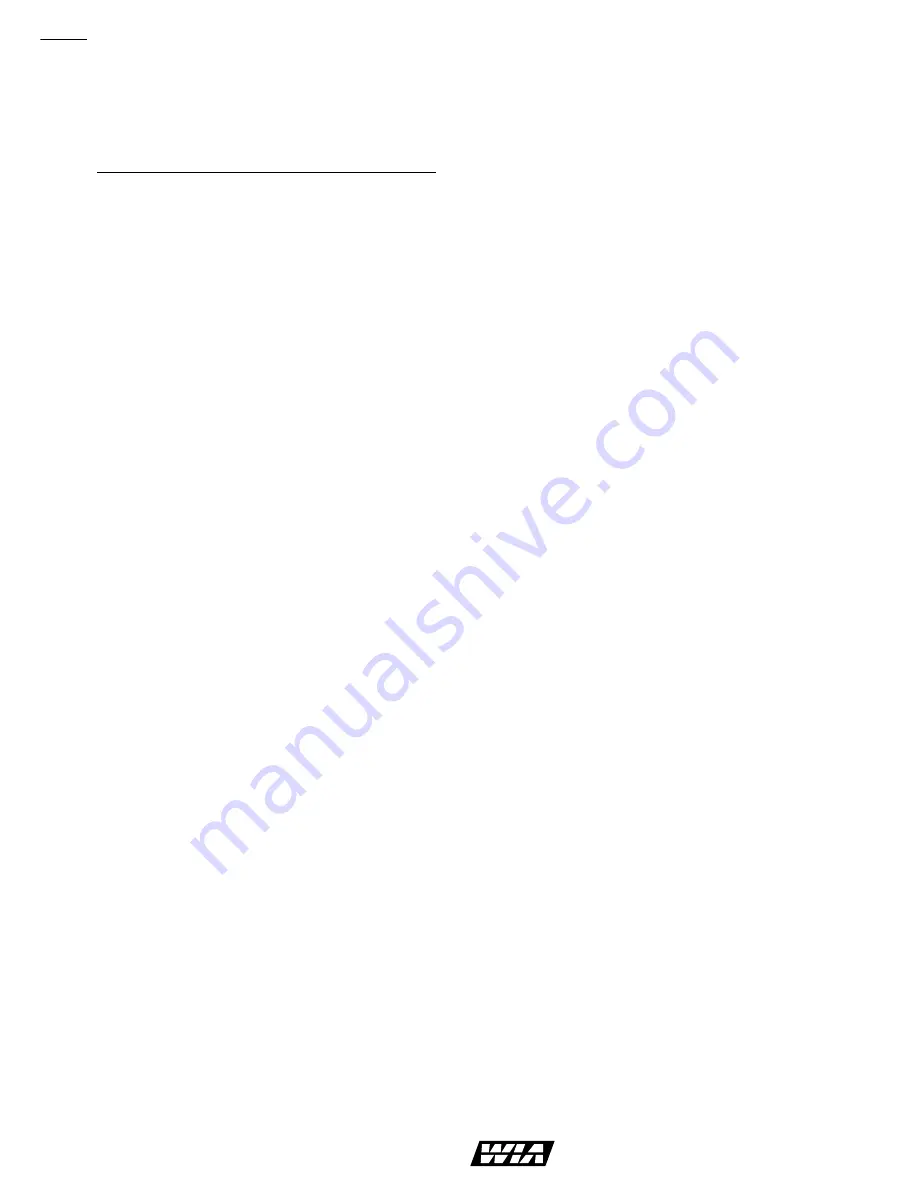
14
Operators Manual
Quality
•
Reliability
•
Performance
Unsatisfactory Welding Performance
and Results
Erratic arc characteristics caused by
poor wirefeed
Erratic wirefeed is the MOST LIKELY cause
of failure in all Gas Metal Arc Welding. It
should therefore be the first point checked
when problems occur.
1 Refer to the wirefeeder Operators
Manual for wirefeed trouble shooting
2 Check if the consumable wire is slipping
in the feed rolls. Replace the feed roll if it
is the incorrect size or is worn
3 Check that gun cable liner is not too
short and is fitted correctly. Refer to the
wirefeeder Operators Manual for fitting
instructions.
Constant poor arc characteristics
Check that the:
1 Correct polarity has been selected for
work and weld cables (refer page 8)
2 Shielding gas is correct for the
consumable wire in use (refer page 10)
3 Welding circuit is making good electrical
connection. Ensure that the work clamp
is securely tightened onto the work
piece so that good electrical contact is
achieved
4 All connections in the external welding
circuit are clean and tight. Problems may
show as hot spots
5 Work piece surface is not contaminated.
Water, oil, grease, galvanising, paint,
or oxide layers can severely disturb the
welding arc and result in a poor weld.
Porosity in weld caused by lack of
shielding gas
1 Check that the correct gas flow rate has
been set (refer page 10)
2 Check for leaks in the gas hose. Replace
if leaking
3 Check for leaks in gun/cable assembly,
eg. fractured gas hose, broken or missing
‘O’ rings. Replace as required
4 Check the gun nozzle is free from spatter
and is firmly attached to the welding gun
to ensure that no air is being drawn into
the shielded area.
Содержание Weldmatic Fabricator P135-2
Страница 21: ...Weldmatic Fabricator Model No CP135 2 Iss A 02 12 19 Notes...
Страница 22: ...20 Operators Manual Quality Reliability Performance Notes...
Страница 23: ...Weldmatic Fabricator Model No CP135 2 Iss A 02 12 21 Notes...
Страница 24: ......