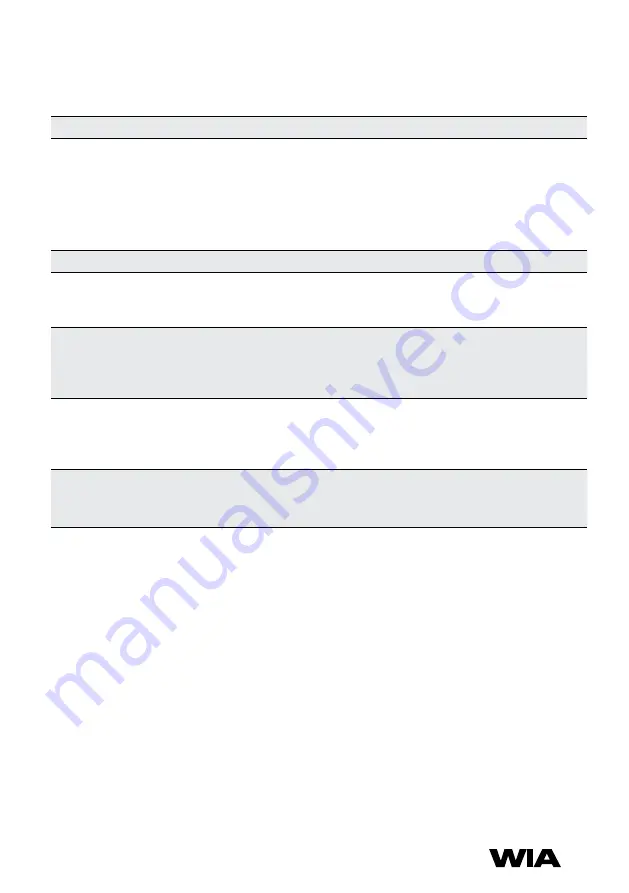
29
28
Problem
Likely Reason
Outcome
MMA/STICK Models
In MMAW (Stick), the
arc is difficult to strike.
The technique required for VRD
enabled welding machines is
not the same as earlier stick
welding units
The technique to strike should
be reviewed, not as a ‘strike’
but more as ‘touch, twist, lift’
motion.
Disabling of the VRD could
enable an easier weld start.
GTAW/TIG Models
Tungsten burns up on
arc start.
The polarity of the electrode/
return cables is incorrect.
Polarity should be confirmed
for the process/wire type in
use.
The weld has small
black ‘lumps’ or ‘dots’
appearing in the pool.
Cleaning is poor.
Old or dirty filler rods can
often be the cause of ‘dirty’
TIG welding operations.
Switching filler rods to
another type or batch may
solve this issue.
Weld is contaminated
with small bubbles
(presence of porosity).
The gas hose is not securely
connected at the machine or
at the regulator.
Ensure the gas connections
from regulator through to
the torch connection are
sufficiently tightened.
Presence of porosity at
weld start.
The torch gas hose has not
been purged sufficiently.
Purge the system and confirm
sufficient gas flow through
the regulator.
Содержание MC114-0
Страница 1: ...WELDING COM AU From serial numbers M1142A Stick TIG Welder OPERATORS MANUAL MC114 0 ...
Страница 31: ...31 Fig 13 Weldarc 200 AC DC Circuit Diagram 11 1 CIRCUIT DIAGRAMS POWER SOURCE ...
Страница 38: ...Weldarc 200 AC DC Operator Manual Model No MC114 2 38 NOTES ...
Страница 39: ...39 NOTES ...