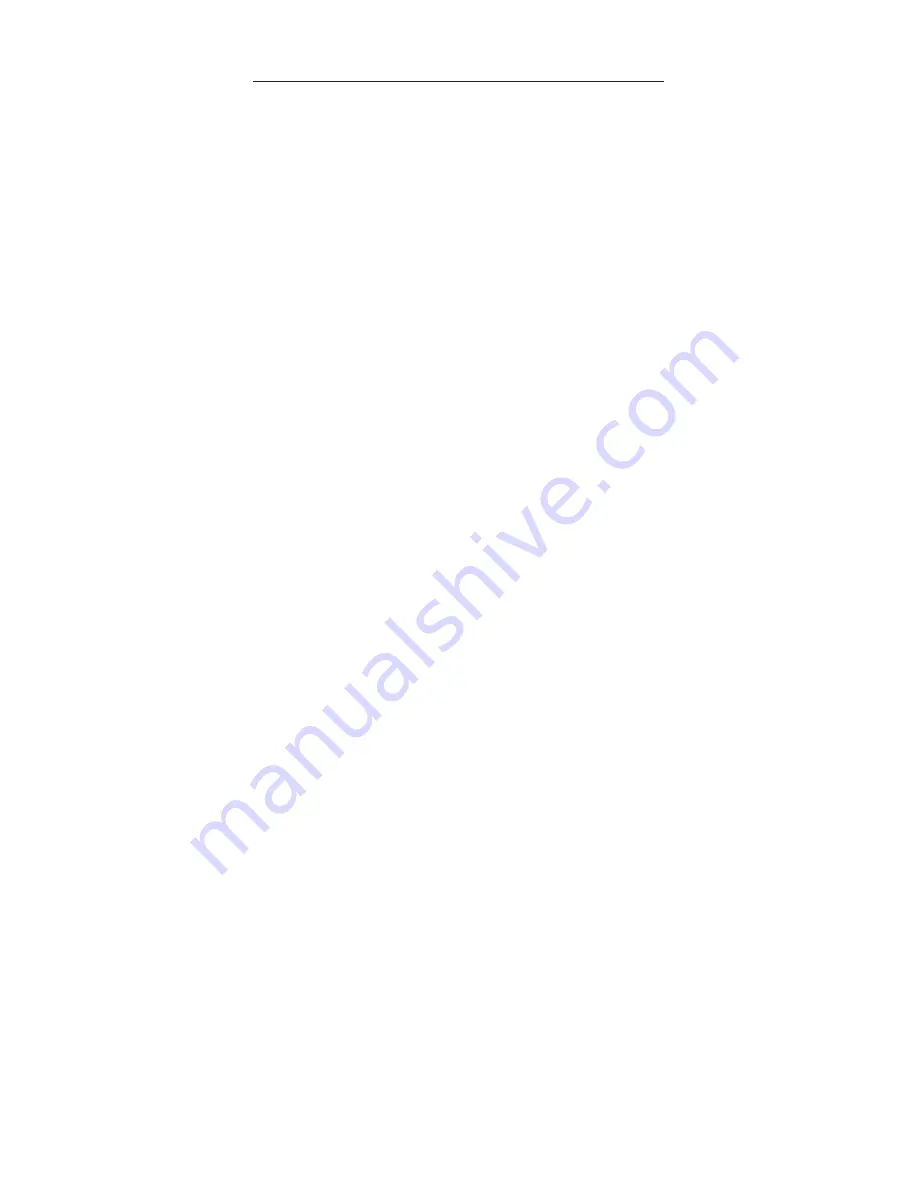
6
PROGRAMME
The electronic control measures dryness by the electrical
resistance method and operates relays to: a) energise
the drive motor, in foward and reverse rotation and b)
energise the full sequence flame controller.
The electronic controller determines when the selected
dryness level is reached, then turns off the heat source
and continues to rotate the drum for 12 minutes
"cool down", intermittent tumbling follows this until the
machine is unloaded - "anticrease" is indicated by a
neon.
The full sequence flame controller opens the tandem
solenoid gas valves after a delay time of about 8 seconds
and operates the pulsing spark ignition. If the flame is not
detected by the flame failure electrode within 10 seconds
then the valves are closed. The system must then be re-
set by switching the machine off and re-starting.
The heat selector switch provides options for either 60°C,
or 50°C, exhaust thermostat control. This results in the
burner cycling on and off giving Ionger drying times. With
low heat drying times vary depending on the weight and
size of the articles, type of fabric, dampness etc. These
thermostats turn off the heating towards the end of the
chosen cycle and so avoid waste of energy. The lower
temperature thermostat prevents delicate fabrics from
getting too hot with possible risk of damage.
An inlet thermostat is fitted in the ducting at the back of
the dryer. This will operate under restricted airflow
conditions. It may operate under certain other conditions,
for example, an overloaded drum or blocked lint filter. This
thermostat switches off the flame controller. This will
result in the burner cycling on and off giving longer than
anticipated drying times. Drying times vary depending on
the weight and size of the articles, type of fabric,
dampness etc.
Should the thermostat fail there is an inlet cut-out
connected in circuit with the gas valves. After operation,
the flame controller must be re-set by switching OFF/ON
the mains supply to restore heating but a service call may
be required to correct the initial fault.
The conditions of failure of the air flow, blow-back, or of
gas interruption are detected by the flame failure
electrode and the system is shut-down.
Both drum rotation and heater control are switched off
when the door is opened and switched on when the door
is reclosed, and the Start button pressed.
For programme times see chart on dryer control panel.
Note:
Do not allow fluff to accumulate around the dryer.
RECOMMENDATIONS FOR DISMANTLING
Note:
Re-assembly should be done in reverse
sequence to these instructions.
TOP ACCESS
Terminal Block (28), Control Unit (10), Timer (211),
Heat Switch (235),
Neon (213),
Micro-Switch
Assembly (248), Control Panel (353).
Withdraw 3 screws from the back flange of the Table Top
Assy. (386) and lift and move it rearwards for removal.
This gives access to the 2-screws securing the Control
Unit Bracket (11) to the top flange of the Cabinet.
Pull off the Timer Knob (352) by means of a loop of thin
insulating wire inserted behind it, to expose the 2-screws
securing the Timer (211) to the Control Panel (353).
To remove the Neon (213) disconnect the faston
connectors and push the neon out of the control panel.
To remove the Control Panel (353), disconnect the faston
connectors from the Timer, Neon, and Heat Switch.
Withdraw 3-screws securing the Control Panel lugs to the
Cabinet top rail. Tilt the Control Panel so that the bottom
lugs can be freed from the top flange of the Front Panel
(376).
To remove the door Micro-Switch Assy. (248), withdraw
the 3-screws securing the Control Panel lugs to the
cabinet top rail and free the Control Panel Assy from the
top flange of the Front Panel. Open the door and
withdraw 2 screws securing the Micro-switch Assy, to
the Front Panel, unclip the wires from the top flange of
the Front Panel, lift out the Assy, and disconnect the
faston connectors.
REAR ACCESS LOWER
Exhaust Thermostats (229, 250), Motor Assembly
(101), Fan Assembly (446), Capacitor (112).
Withdraw the 6 screws securing the Cover Plate (19) to
the Back Panel (24) and remove it. Pull out the Exhaust
Tube (30).
This gives access to the Exhaust Thermostats (229,
250), which are each secured to the Banjo (440) by a
screw.
Note: The 50˚C thermostat is identified by a red spot on
the body.
REAR ACCESS LOWER (continued)
To remove the Motor (101) the belt (125), must first be
removed from the Motor. Disconnect the Motor leads.
Withdraw the black headed pin (537). Exert an anti-
clockwise force to disconnect the bayonet fitting between
SERVICE INSTRUCTIONS
Содержание ECO 83A
Страница 12: ...12 Chart 3 Motor runs Full Sequence Control produces ignition sparks but gas does not ignite ...
Страница 14: ...14 ...
Страница 15: ...15 WHITE KNIGHT ECO 83A_ CROSSLEE P L C EXPLODED VIEW 1 367 ...
Страница 17: ...17 WHITE KNIGHT ECO 83A_ CROSSLEE P L C EXPLODED VIEW 3 INTERNALS VIEWED FROM REAR ...
Страница 18: ...WHITE KNIGHT ECO 83A_ CROSSLEE P L C EXPLODED VIEW 4 INTERNALS VIEWED FROM REAR 18 ...
Страница 19: ...19 WHITE KNIGHT ECO 83A_ CROSSLEE P L C EXPLODED VIEW 5 HEATER ASSEMBLY ...
Страница 23: ...23 ...
Страница 24: ...Manufactured By Crosslee plc Halifax Road Hipperholme Halifax HX3 8DE 4213 094 79382 ...