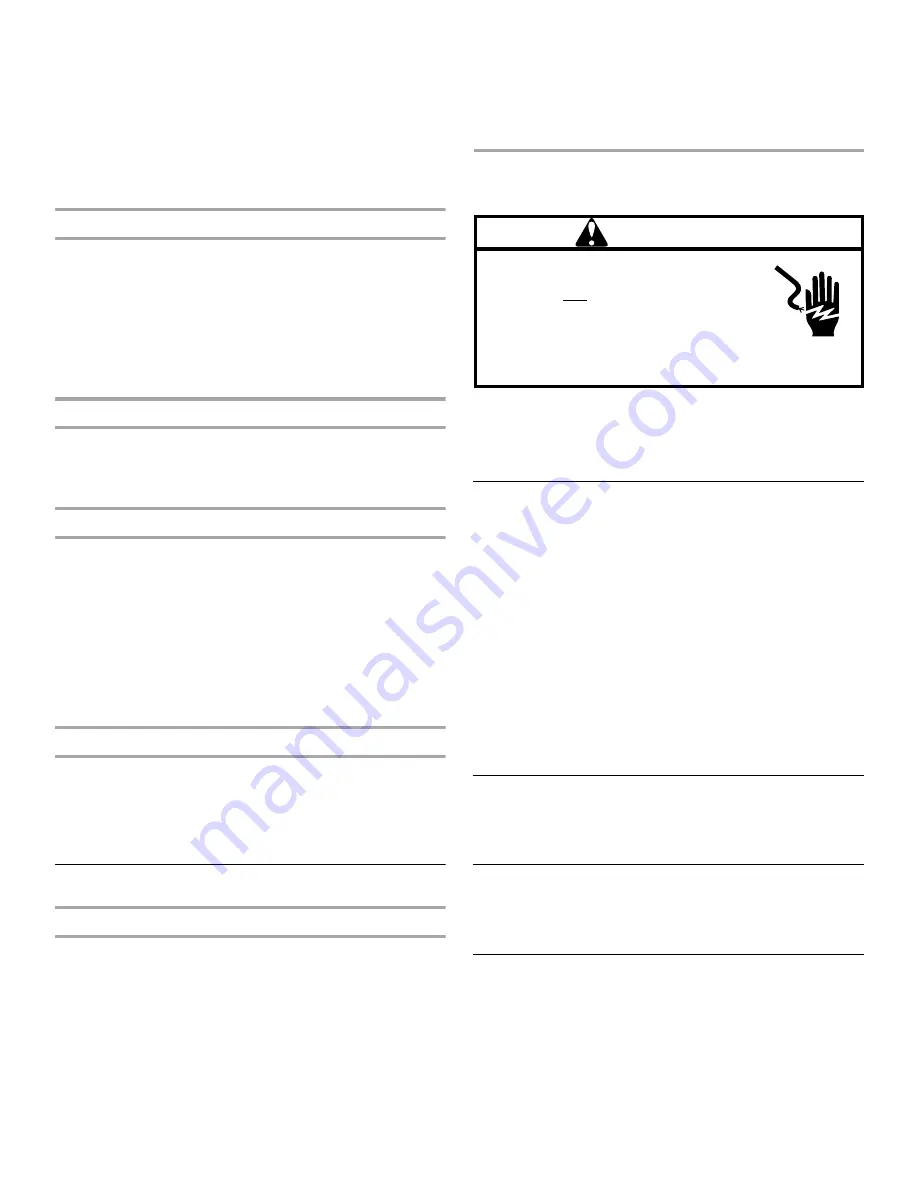
18
■
Check flame sensor.
A drop in flame signal can be caused by nearly invisible
coating on the sensor. Remove the sensor and carefully clean
with steel wool.
■
Check wiring.
Check wiring for opens/shorts and incorrect wiring.
IMPORTANT: If you have to frequently reset your gas/electric
package unit, it means that a problem exists that should be
corrected. Contact a qualified servicer for further information.
Pressure Switch Stuck Open
A pressure switch stuck open can be caused by a faulty pressure
switch, faulty wiring, a disconnected or damaged hose, a
blocked or restricted flue or a faulty induced draft blower.
If the control senses an open pressure switch during the prepurge
cycle, the induced draft blower only will be energized. If the
pressure switch opens after ignition has begun, the gas control
valve is de-energized, the circulator blower heat-off cycle begins,
and the induced draft blower remains on. The diagnostic fault
code is 2 flashes.
Pressure Switch Stuck Closed
A stuck closed pressure switch can be caused by a faulty
pressure switch or faulty wiring. If the control encounters a
pressure switch stuck closed, the induced draft blower remains
off. The diagnostic LED code for this fault is 3 flashes.
Open Thermal Protection Device
If the primary limit switch opens, the gas control valve is
immediately de-energized, and the induced draft and air
circulating blowers are energized. The induced draft and air
circulator blowers remain energized until the limit switch recloses.
The diagnostic fault code for an open limit is 4 flashes.
A primary limit will open due to excessive supply air
temperatures. This can be caused by a dirty filter, excessive duct
static, insufficient airflow or a faulty limit. Check filters, total
external duct static, blower motor, blower motor speed tap (see
wiring diagram) and limit. This limit will automatically reset once
the temperature falls below a preset level.
Flame Detected with Gas Control Valve Closed
If flame is detected with the gas control valve de-energized, the
combustion and air circulator blowers are energized. The
diagnostic fault code is 5 flashes for this condition. The control
can be reset by removing the power supply to the unit or it will
automatically reset after one hour. Incorrect wiring is the probable
cause for this fault.
Abnormal Operation—Cooling
Short Cycle Compressor Delay
The automatic ignition control has a built-in feature that prevents
damage to the compressor in short-cycling situations. In the
event of intermittent power losses or intermittent thermostat
operation, the ignition control will delay output to the compressor
contactor for 3 minutes from the time power is restored.
Compressor is off a total of 3 minutes. The diagnostic LED will
flash 6 times to indicate the compressor contactor output is
being delayed.
NOTE: Some electronic thermostats also have a built-in
compressor short-cycle timer that may be longer than the
3-minute delay given above. If you are using an electronic
thermostat and the compressor has not started after 3 minutes,
wait an additional 5 minutes to allow the thermostat to complete
its short-cycle delay time.
MAINTENANCE
Have the gas heating section of the unit checked at least once a
year before the heating season begins to be sure that the
combustion air inlet and flue outlet hoods are not blocked by
debris, which would prevent adequate combustion air and a
properly operating vent system.
Filter Replacement or Cleaning
A return air filter is not supplied with this unit; however, there
must be a means of filtering all of the return air. The filter(s) may
be located in the return air duct(s) or return air filter grille(s).
Consult with your installing dealer for the actual location of the
return air filter(s) for your unit.
Dirty filters are the most common cause of inadequate heating or
cooling performance. Filter inspection should be made at least
every 2 months; more often if necessary because of local
conditions and usage.
Dirty throwaway filters should be discarded and replaced with a
new, clean filter. Dirty permanent filters should be washed with
water, thoroughly dried and sprayed with a filter adhesive before
being reinstalled. (Filter adhesives may be found at many
hardware stores.) Permanent filters should last several years.
However, should one become torn or uncleanable, it should be
replaced.
Cabinet Finish Maintenance
Use a fine grade automotive wax on the cabinet finish to maintain
the finish’s original high luster. This is especially important in
installations with extended periods of direct sunlight.
Clean Outside Coil—Qualified Servicer Only
The coil with the outside air flowing over it should be inspected
annually and cleaned as frequently as necessary to keep the
finned areas free of lint, hair and debris.
Condenser, Evaporator and Induced Drafter Motors
Bearings on the air circulating blower motor, condenser motor
and the combustion fan motor are permanently lubricated. No
additional oiling is required.
HIGH VOLTAGE!
WARNING
Disconnect ALL power before servicing.
Multiple power sources may be present.
Failure to do so may cause property damage,
personal injury or death.