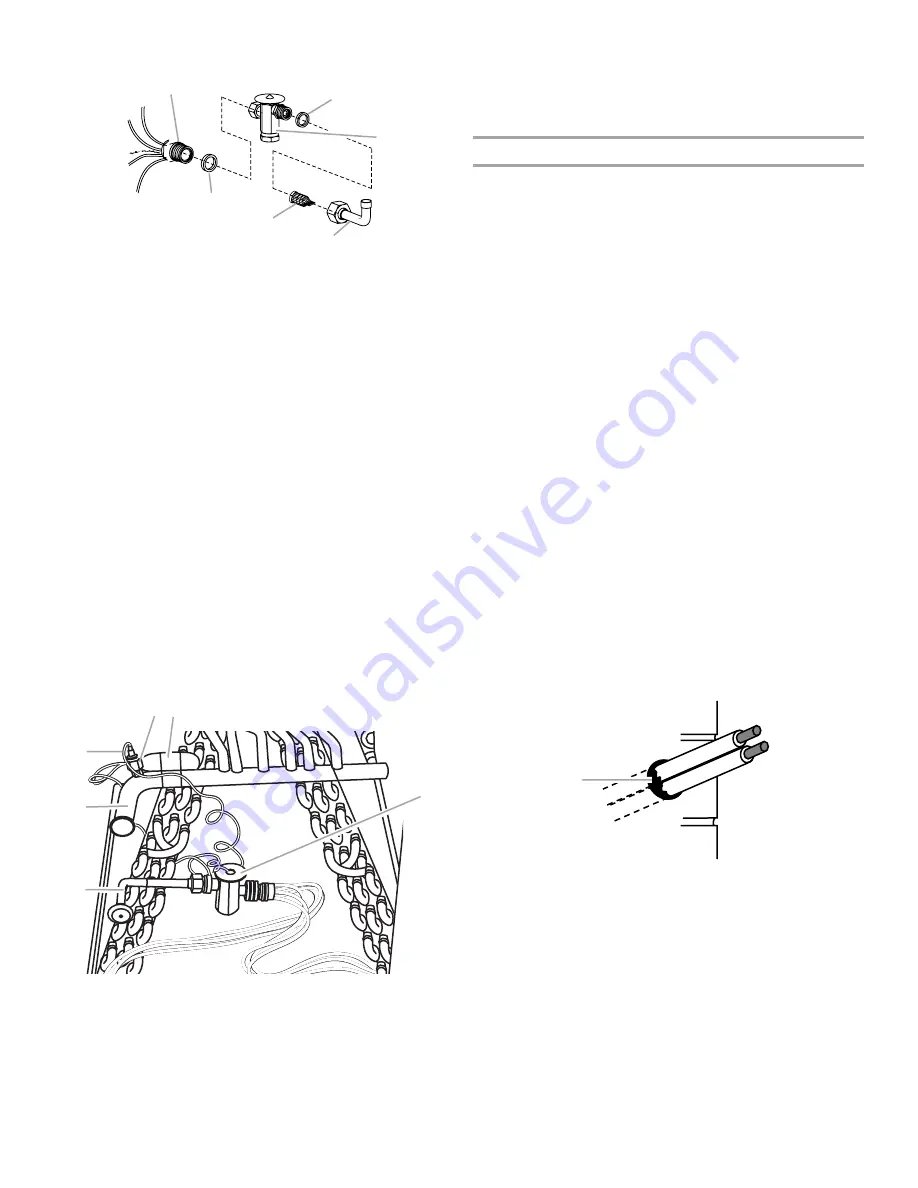
7
Thermal Expansion Valve Installation
To install the thermal expansion valve:
1. Separate the distributor assembly.
2. If a piston orifice is installed, remove the piston orifice and old
Teflon
®
seal and discard.
3. Insert nozzle end of the thermal expansion valve along with a
new Teflon
®
seal into the distributor.
4. Tighten to 20 to 30 ft/lbs. Use backup wrench on all wrench
flats.
NOTE: Overtightening may crush the Teflon
®
seal and cause
a leak.
5. Attach liquid line portion of distributor assembly along with
new Teflon
®
seal to the inlet of the thermal expansion valve.
6. Tighten to 20 to 30 ft/lbs. Use backup wrench on all wrench
flats.
NOTE: Overtightening may crush the Teflon
®
seal and cause
a leak.
7. Connect the external equalizer line to the equalizer port on
the suction line.
8. Tighten to 8 ft/lbs.
9. Attach the superheat sensing bulb to the suction header with
the strap provided with the thermal expansion valve.
NOTE: If installing a thermal expansion valve on an indoor coil
that previously used a fixed orifice, be sure to remove the existing
fixed orifice. Failure to remove a fixed orifice when installing a
thermal expansion valve to the indoor coil may result in improper
operation and damage to the system.
Connect Liquid and Suction Lines
1. Route the suction and liquid lines from the fittings on the
indoor coil to the fittings on the heat pump. Run the lines in
as direct a path as possible, avoiding unnecessary turns and
bends.
2. For product efficiency, be sure that the suction line is
insulated over the entire exposed length and that both
suction and liquid lines are not in direct contact with floors,
walls, ductwork, floor joists, or other piping.
3. Remove valve cores.
4. Wrap the service valves with a wet rag.
5. Connect the suction and liquid lines, using a brazing
compound. Braze with an alloy of silver or copper and
phosphorus with a melting point above 1,100°F (593ºC).
NOTE: Do not use soft solder.
6. Make sure indoor coil has been put in place according to the
Installation Instructions and is connected to the refrigerant
lines.
7. Replace valve cores.
8. Pressurize the lines and indoor coil with a pressure not to
exceed 20 psig.
9. Leak test the lines with a pressure not to exceed 20 psig.
10. Evacuate the indoor coil and lines to a minimum of
500 microns to remove contamination and moisture, then
disconnect the vacuum pump.
11. Open the suction and liquid service valves fully.
12. Insulate the suction line with refrigerant line insulation
material of
¹⁄₄
" (6.4 mm) or more wall thickness.
13. Pack insulating material around refrigerant lines where they
penetrate the structure to protect the lines and to minimize
vibration transmission.
A. Distributor
B. Teflon
®
seal
C. Thermal expansion valve
D. Liquid line stub
E. Strainer
F. Teflon
®
seal
A. Equalizer port
B. Superheat sensing bulb
C. Thermal expansion valve
D. Liquid line
E. Suction line
F. Equalizer line
A
B
C
D
E
F
®Teflon is a registered trademark of E.I. Dupont de Nemours and
Company.
E
F
A B
C
D
A. Insulating material around refrigerant lines
A