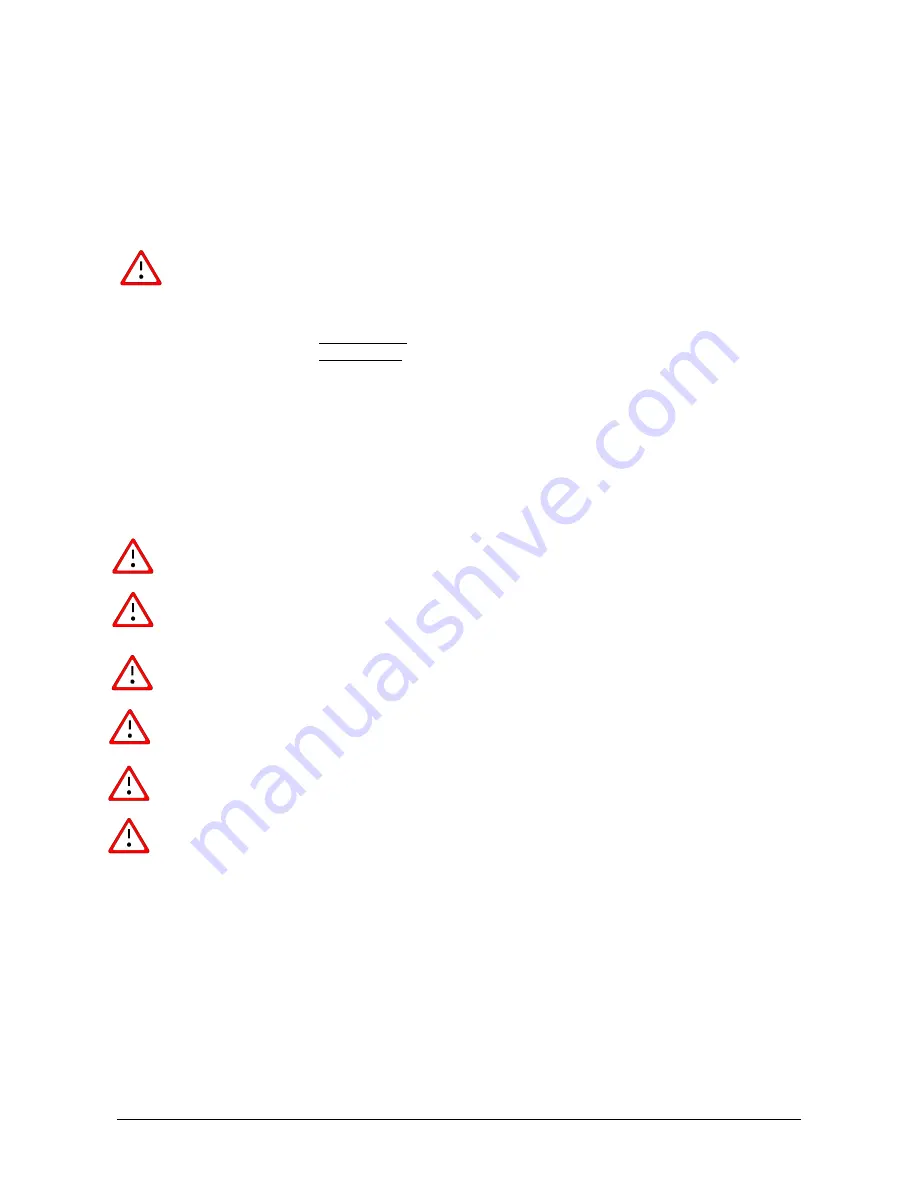
- 7 -
Installation and Connection
Water connection
WHIRLPOOL ovens have one or two water connections.
To facilitate cleaning and service, the oven should be connected with an approved flexible ¾’’
hose and the permanent installations should be fitted with a stop tap.
Before connecting the oven to water, flush the tubes thoroughly.
Hardness of the water: max.
3
dH
Conductivity:
min. 75 microsiemens
Water pressure: min.
2.5
bar (36 PSI) dynamic pressure (when CombiWash on),
max. 6 bar (87 PSI)
Water flow:
min.
12
l/m
Water temperature:
max. 20°C (68°F)
Chloride concentration: max. 100 mg/litre
Sulphate:
max. 150 mg/litre
The connection wire to the system should be fitted with a stop valve and a nonreturn valve.
If the feeder is connected to the water distribution system with a flexible hose, this hose
should be VA approved.
If the water temperature exceeds 20°C / 68°F, problems with regard to
ClimaOptima calibration and cooling of the oven may occur.
Ovens with a steam generator must not be connected to a reversed osmosis
plant, as this may cause problems with the reading of the water level in the
steam generator.
The water connection must be carried out by an authorised plumber in
accordance with existing rules and regulations
Clogged up water filters and dirt in the solenoid valves are not covered by the
warranty.
To ensure that the water quality is in conformity with the above requirements,
the installation of a water filter in front of the water connection to the oven is
recommended.
The installation of a particle filter (0.25mm) is also recommended.
In the case of two water connections, the following applies:
1)
1 connection for raw water for the condensation jet (cold water). Located at the back.
2)
1 connection for the steam generator and the jet in the oven chamber. Must meet the
requirements applying to water supplied to household appliances; however, hot water with
a temperature not exceeding 20°C / 68°F can be used. Located at the front.