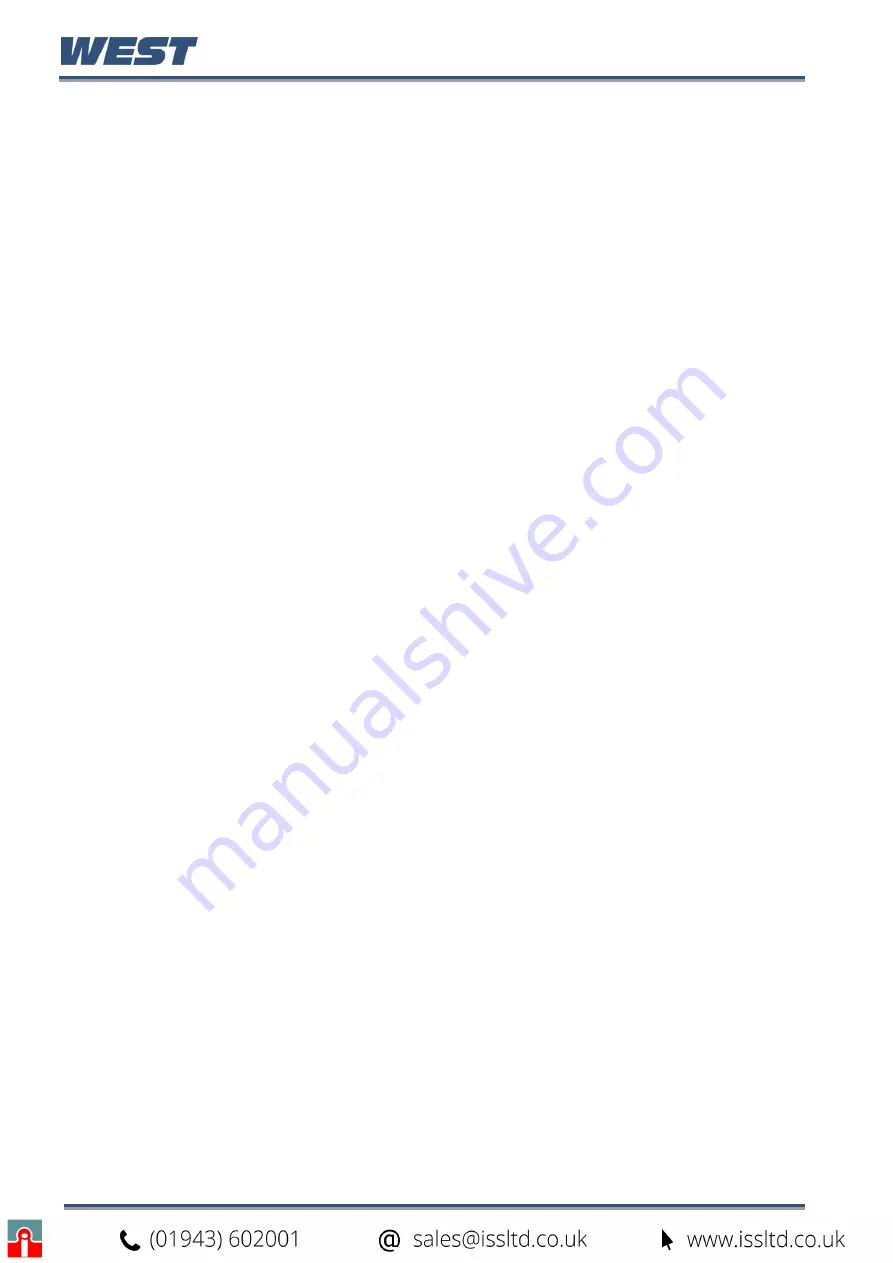
Pro-EC44 2-Loop Graphical Profile Controller & Recorder
Pro-EC44 Product Manual - 59540-2 September 2014
Page 208
Auxiliary Input Offset
Used to adjust the value of auxiliary input A if it provides a Remote Setpoint. Positive values
are added to the remote setpoint value, negative values are subtracted, but the setpoint is
still constrained by the setpoint limits.
Also refer to: Auxiliary Input; Remote Setpoint; Scaled Input Upper Limit; Scaled Input Lower
Limit Setpoint Lower Limit and Setpoint Upper Limit.
Auxiliary Input Type
Defines the type and range of the linear input signal for auxiliary input A. It can be mADC or
VDC. This can be used as a Remote Setpoint input.
Also refer to: Remote Setpoint and Setpoint.
Auxiliary Input Upper Limit
When the auxiliary input is used to provide a Remote Setpoint (RSP), this setting defines the
value of the RSP when the auxiliary input signal is at its maximum value (e.g. for 4 to 20mA,
the value when 20mA is applied). However, the RSP value is always constrained by the
setpoint limits.
Also refer to: Auxiliary Input; Auxiliary Input Lower Limit; Auxiliary Input Offset; Remote
Setpoint; Setpoint and Setpoint Upper Limit and Setpoint Lower Limit.
Band Alarm Value
The amount of control deviation that is acceptable before a Band Alarm is activated. If the
process variable is more than the value of this band from the actual setpoint, the alarm will
be active.
Also refer to: Actual Setpoint; Alarm Operation; Alarm Types; Control Deviation; Input Span;
LSD and Process Variable.
Bar Graphs
The instrument displays uni or bi-directional bar-graphs in the operation mode for loop 1 & 2
PID power (single control = 0 to 100%, dual control =
-
100% to +100%), control deviation (-
5% to +5%) and % Recorder Memory Used (0 to 100%). In Profiler Mode, profile & current
segment bar-graphs are shown (0 to 100%).
Also refer to: Control Deviation; Data Recorder; Display Configuration; Operation Mode; Main
Menu; PID and Profiler.
Bias
Bumpless Transfer
A method used to prevent sudden changes to the correcting variable, when switching
between automatic PI or PID and Manual control modes. During a transition from PI or PID to
manual control, the initial manual power value is set to the previous automatic mode value.
The operator then adjusts the value as required. During a transition from manual control to PI
or PID, the initial automatic value is set to the previous manual mode value. The correcting
variable level will gradually adjusted by the control algorithm at a rate dependant on the
integral action resulting from the integral time constant value.
A similar
Bumpless transfer is
used with Gain Scheduling when switching PID Sets. Since integral action is essential to
Bumpless Transfer, this feature is not available if integral is turned off.
Also refer to: Correcting Variable; Gain Scheduling; Integral Action; Manual Mode; PI and
PID.
Содержание Pro-EC44
Страница 1: ...Pro EC44 2 Loop Graphical Profile Controller Recorder Pro EC44 User Guide 59540 2 ...
Страница 2: ......
Страница 6: ......