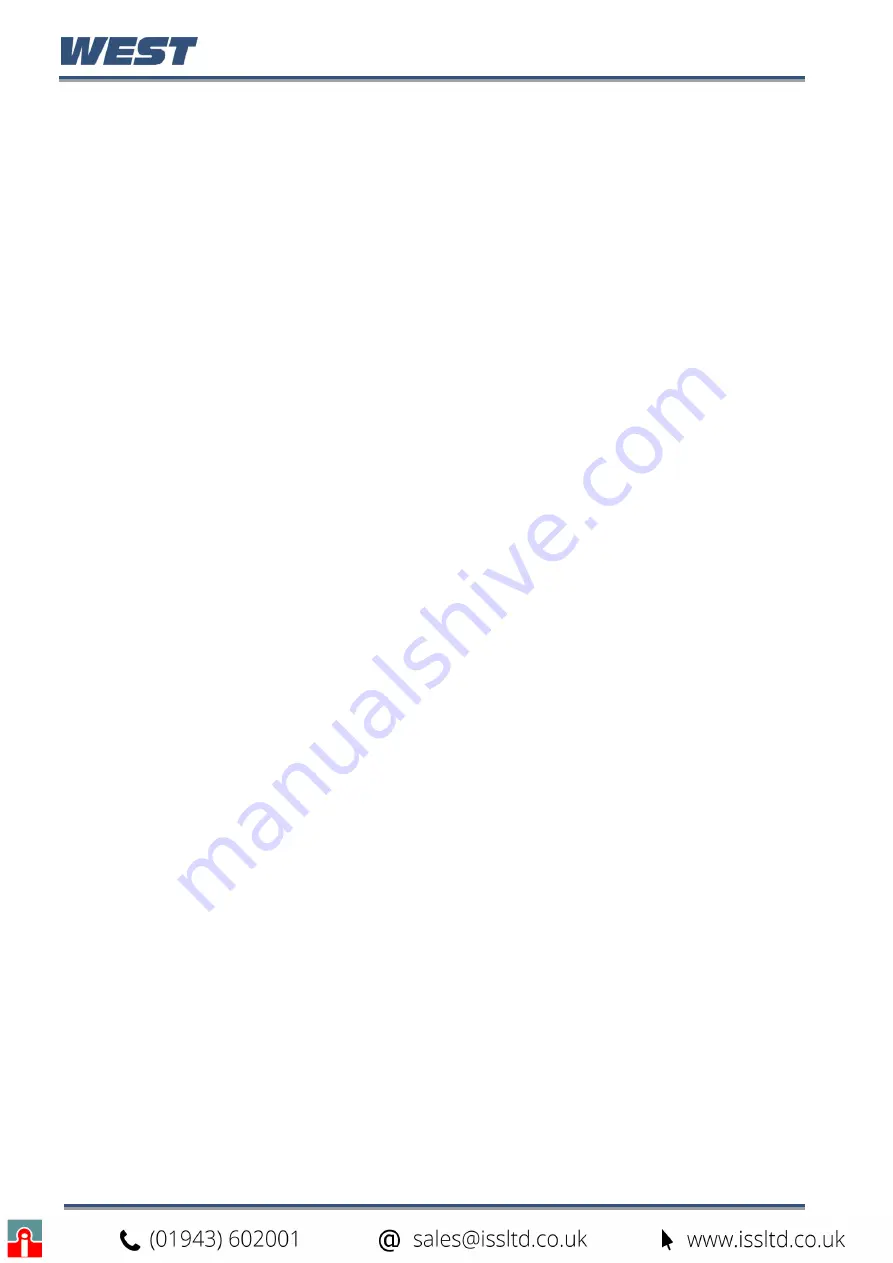
Pro-EC44 2-Loop Graphical Profile Controller & Recorder
Pro-EC44 Product Manual - 59540-2 September 2014
Page 218
Manual Loop Alarm Time
The loop alarm time used is manually set whenever a loop alarm is defined to have a
manually set time, or if P, PD or On-Off control is selected. This parameter determines the
duration of the output saturation condition after which the loop alarm will be activated.
Also refer to: Loop Alarm; On-Off Control; PD; PI and PID.
Manual Mode
Manual Mode operates as follows:
The setpoint legend is replaced by the word
MAN
and setpoint value is replaced by a %
output power value. This value may be adjusted using the keypad or via serial comms. The
power value can be varied from 0% to 100% for controllers using single control type, and -
100% to +100% for controllers using dual control type. Switching between automatic and
manual modes is achieved using “bumpless transfer”.
Auto/manual mode can selected from the control configuration sub-menu or via a digital input
if one has been configured for this function. Alternatively, if enabled in the display
configuration sub-menu, the user to switch between automatic and manual control from
operation mode. It is possible to use a controller as a permanent “Manual Station” by
permanently selecting manual control in the control configuration sub-menu.
Caution:
Manual Mode should be used with care because the power output level is set
by the operator, therefore the PID algorithm is no longer in control of the process.
Manual mode also ignores any output power limits, valve open/close limits and the
control enable/disable setting. The operator is responsible for maintaining the process
within safe limits.
Also refer to: Bumpless Transfer; Control Configuration; Control Type; Operation Mode; PID;
Power Output Limits and Serial Communications.
Manual Reset
Used to manually bias proportional outputs to compensate for control deviation errors due to
process load variations. It is expressed as a percentage of output power. This parameter is
not applicable if the primary output is set to On-Off control. If the process variable settles
below setpoint use a higher value to remove the error, if the process variable settles above
the setpoint use a lower value.
For PID or PI control, typically set manual reset to approximately 80% of power needed to
maintain setpoint, although lower values can be used to inhibit start-up overshoot. Integral
action will automatically remove any control deviation error.
Also refer to: Control Deviation; Integral Action; ON/OFF Control; PI Control; PID;
Proportional Control; Process Variable; and Setpoint.
Master & Slave Controllers
The terms Master and Slave are often used in relation to serial communications. This
instrument can be a communications slave if an Ethernet or RS485 module is fitted.
With RS485 it can also act as a setpoint master or slave in multi-zone applications. In this
case, one instrument controls the setpoint of one or more others. This could be a simple
master/slave application where the master controller transmits its setpoint to the slaves so
that all operate at the same temperature. Alternatively, an offset can be applied to each zone
using the slave’s setpoint offset parameter, so each is offset slightly from the master.
A similar master/slave relationship can be achieved if the master retransmits its setpoint as
an analogue signal. In this case, the slave controllers must have matching remote setpoint
inputs so that they can follow the
masters’ setpoint value. It is possible to apply an offset to
each zone if the slave has an RSP offset parameter. If not the remote setpoint input scaling
can be adjusted to achieve the offset.
Содержание Pro-EC44
Страница 1: ...Pro EC44 2 Loop Graphical Profile Controller Recorder Pro EC44 User Guide 59540 2 ...
Страница 2: ......
Страница 6: ......