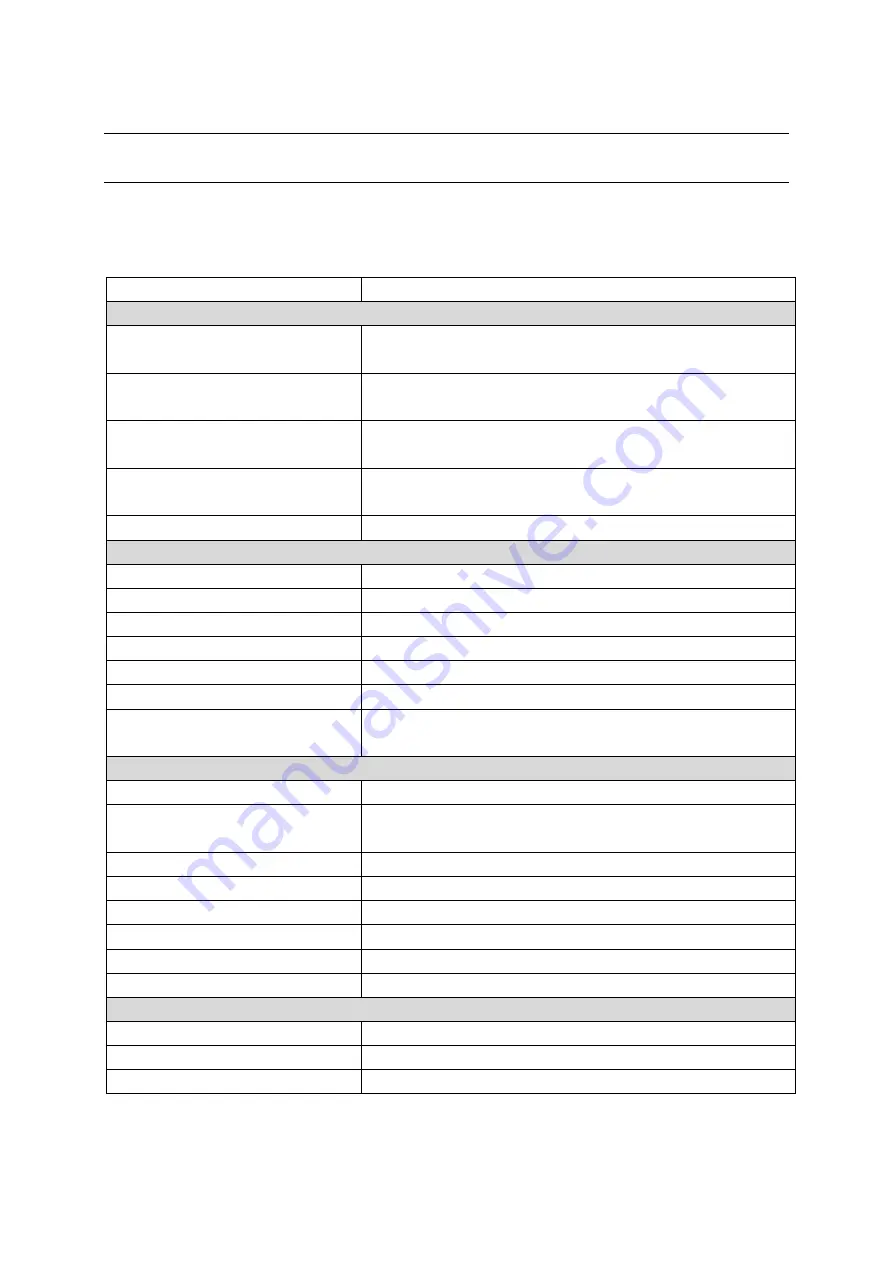
34
Trouble Shooting
4.1 Mig Welding Trouble Shooting
The following chart addresses some common problems during MIG Welding.
In the event of equipment malfunction, contact an authorized service agent.
Possible Reason
Suggested Solution
The Welding current is unstable
The pressure arm on the wire feeder is not
properly adjusted
Adjust it to get proper pressure.
The drive roll does not match the wire size being
used.
Make sure they match with each other.
The contact tip of the welding torch is badly
worn.
Replace it.
The wire-feeding tube of the welding torch is
badly worn.
Replace it
The welding wire is of poor quality
Replace it with welding wire of good quality
Excessive Spatter
Wire feed speed set too high
Select lower wire speed
Voltage to high
Select a lower voltage setting
Wrong polarity Set
Select the correct polarity for the wire being used
Stick out too long
Bring the torch closer to the work piece
Contaminated base metal
Remove any paint , grease, oil & dirt
Contaminated MIG Wire
Use clear dry rust free wire only.
Gas Flow too high or too low
Check gas is connected. Set gas flow between 10-15 l/min. Protect Weld Zone
from wind & drafts
Porosity
Wrong Gas
Check that correct gas is being used
Gas Flow too high or too low
Check gas is connected. Set gas flow between 10-15 l/min.
Protect Weld Zone from wind & drafts
Moisture on the base metal
Remove all moisture from base metal
Contaminated base metal
Remove any paint , grease, oil & dirt
Contaminated MIG Wire
Use clear dry rust free wire only.
Gas nozzle worn or out of shape
Replace it
Missing or damaged gas diffuser
Replace it
Mig Torch O-ring missing or worn
Replace it
Wire stubbing
Holding the torch too far away
Bring torch closer to work piece. Stick out should be 5-10mm
Welding Voltage too Low
Increase Voltage
Wire Speed Too High
Decrease the wire speed
Содержание TM250C
Страница 2: ...2...