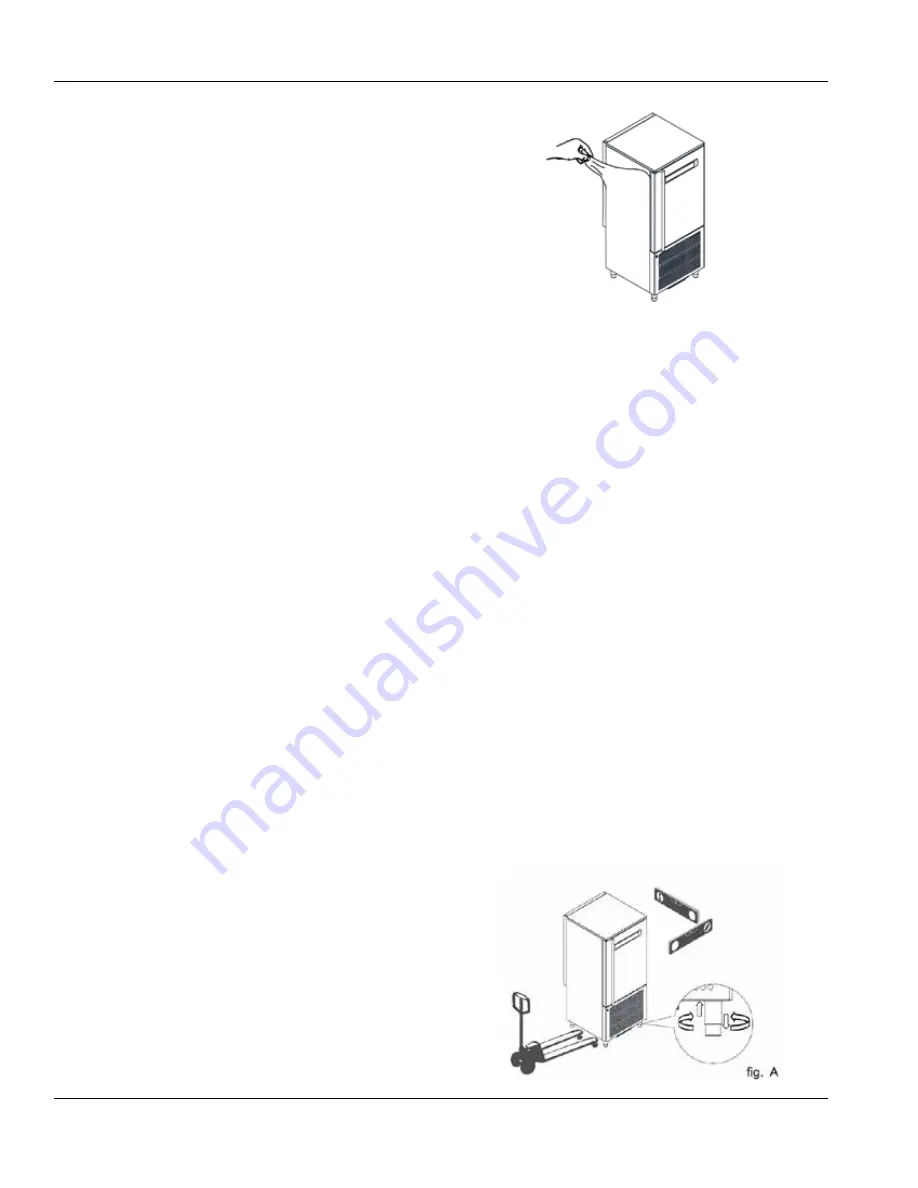
8
Part Number: 9294045 07/19
Technical Information
Section 2
3 - INSTALLATION
,
,
All stages of installation must be carried out in
compliance with the national standards in force
according to the manufacturer’s instructions and
by professionally qualified personnel.
Installation of the appliance and of the refrigerating
unit must only be carried out by technicians of the
manufacturer or by skilled personnel.
If the machine was supplied with a remote condesing
unit, it is the installer’s responsibilty to check all the
connections in accordance with the instructions provided
for the installation of the systems and machinery.
The installer is advised to use the appropriate personal
protective equipment necessary for processing and in
compliance with the regulations in force.
3.1 - Transportation and handling
The net and gross weight of this appliance can be found
on the external packaging.
Loading and unloading of the appliance and/or of the sub-
systems from the means of transport can be performed
using a forklift truck or fork pallet truck, the length of
which is more than half that of the unit or using cranes
where the apppliance/sub-system is fitted with eyebolts.
The lifting equipment must be chosen according to the
size of the packaged machine/components and with
sufficient capacity. For handling of the appliance/sub-
systems, every precaution must be taken not to damage
them, respecting the indications on the packaging.
3.2 - Unpackaging and disposal
Remove all cardboard or the wooden crate from the base
on which the machine is placed. Then lift the machine/
sub-assemblies with a suitable means (forklift truck);
remove the wooden base and position the machine/sub-
assemblies in the place provided.
After removing the packaging, verify the integrity of the
machine/sub-assemblies in case of uncertainty do not use
it and contact the distributor.
Remove the protective PVC film on the stainless steel
panels from all sides both internally and externally.
NOTE: All the various components of the packaging must
be disposed of according to the regulations in force in the
country where the appliance is being used. In any case
nothing must be disposed of into the environment.
3.3 - Positioning
The appliance:
• must be installed in places where it can be checked by
qualified personnel
• it must not be installed outdoors.
• it must not be installed in dusty environments.
• it must not be placed in locations with the presence of
water jets.
• it must not be washed with water jets.
• it must be installed and tested in full compliance with
safety laws, traditional systems and with the regulations
in force.
• it must be positioned at a minimum distance of 120mm
from the rear wall.
The installer must verify any requirements for fire safety
(refer to the command of the local fire department for the
relevant indications.)
Level the appliance through adjustment of the feet. For
the setting up of heavier machines, use dedicated hoists
(fig. A - chap. 3.1).
If the appliances are not levelled their functioning and the
flow of condensates could be impaired.
Содержание Delfield CV10E
Страница 22: ...22 Part Number 9294045 07 19 Troubleshooting Section 4 T40 BLast Chiller Shock Freezer ...
Страница 25: ...Part Number 9294045 07 19 25 Section 4 Troubleshooting T5 T14D Refrigeration System Schematic ...
Страница 26: ...26 Part Number 9294045 07 19 Troubleshooting Section 4 T5 T14D Wiring Diagram ...
Страница 31: ...Part Number 9294045 07 19 31 Section 4 Troubleshooting Controller Buttons ...
Страница 41: ...Part Number 9294045 07 19 41 Section 4 Troubleshooting THIS PAGE INTENTIONALLY LEFT BLANK ...