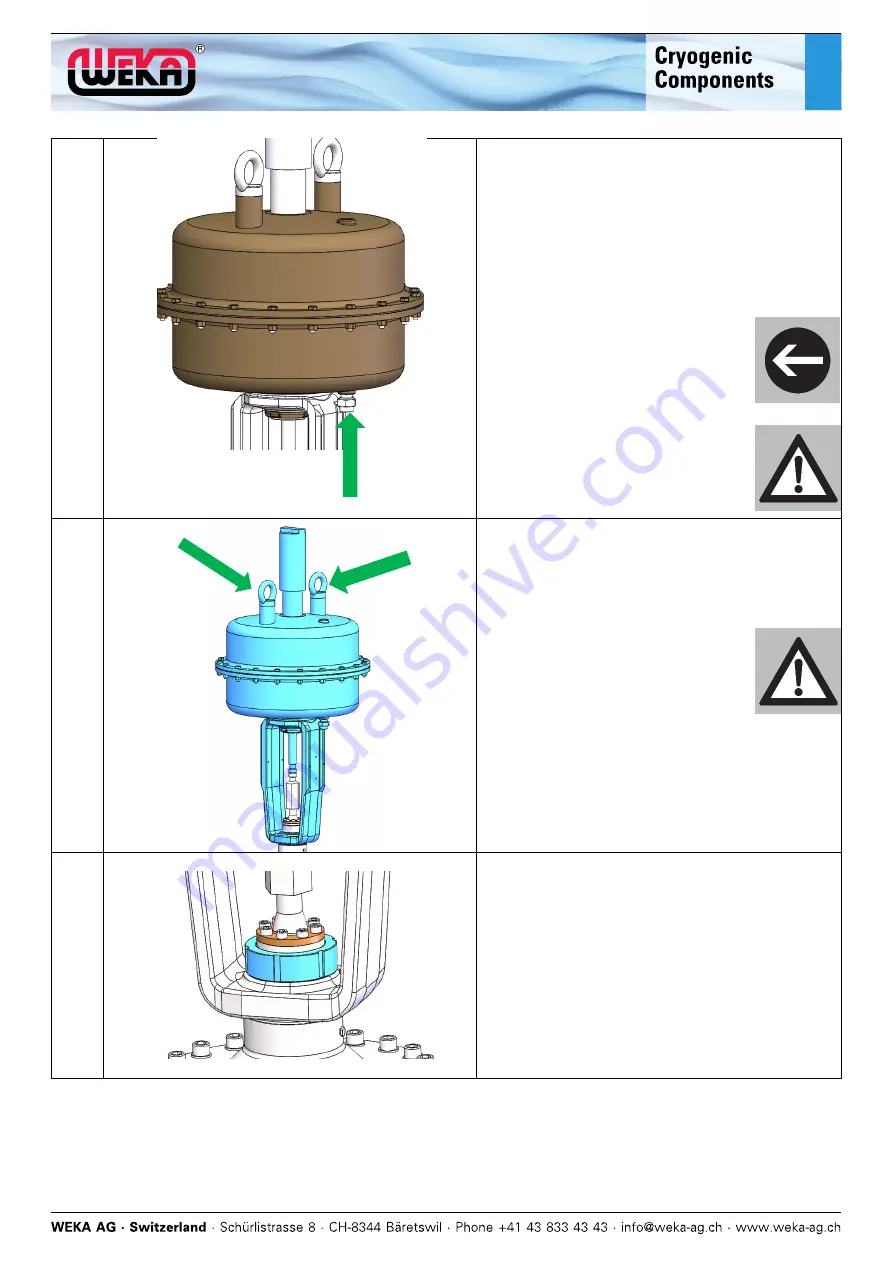
WEKA_IOM_C-0068_TgxV_DN250_PN6_EN / 17.04.2020
31 / 38
3
Connect the compressed air line to the
actuator.
The maximum and minimum air pressure
values are provided in the customer drawing.
Depending on the additional parts for the
actuator, the air connection can be at a
different location.
Please note:
The maximum air pressure of 6 bar
must not be exceeded; higher
pressure will result in damage to
the actuator.
Attention:
The actuator and the coupling are
moving parts. Risk of injury! Keep
your hands off.
4
Carefully assemble the complete actuator unit
(blue marked) with a crane.
Use the two eye bolts for this.
ATTENTION:
The insert must not be turned
during disassembly, this could
result in irreversible damage to the
seat surface.
5
Grease the thread from the lower nut with
Gleitmo 599.
The nut can be retracted between the spindles.
Tighten the lower nut from the actuator using a
Hook spanner 120
– 130.