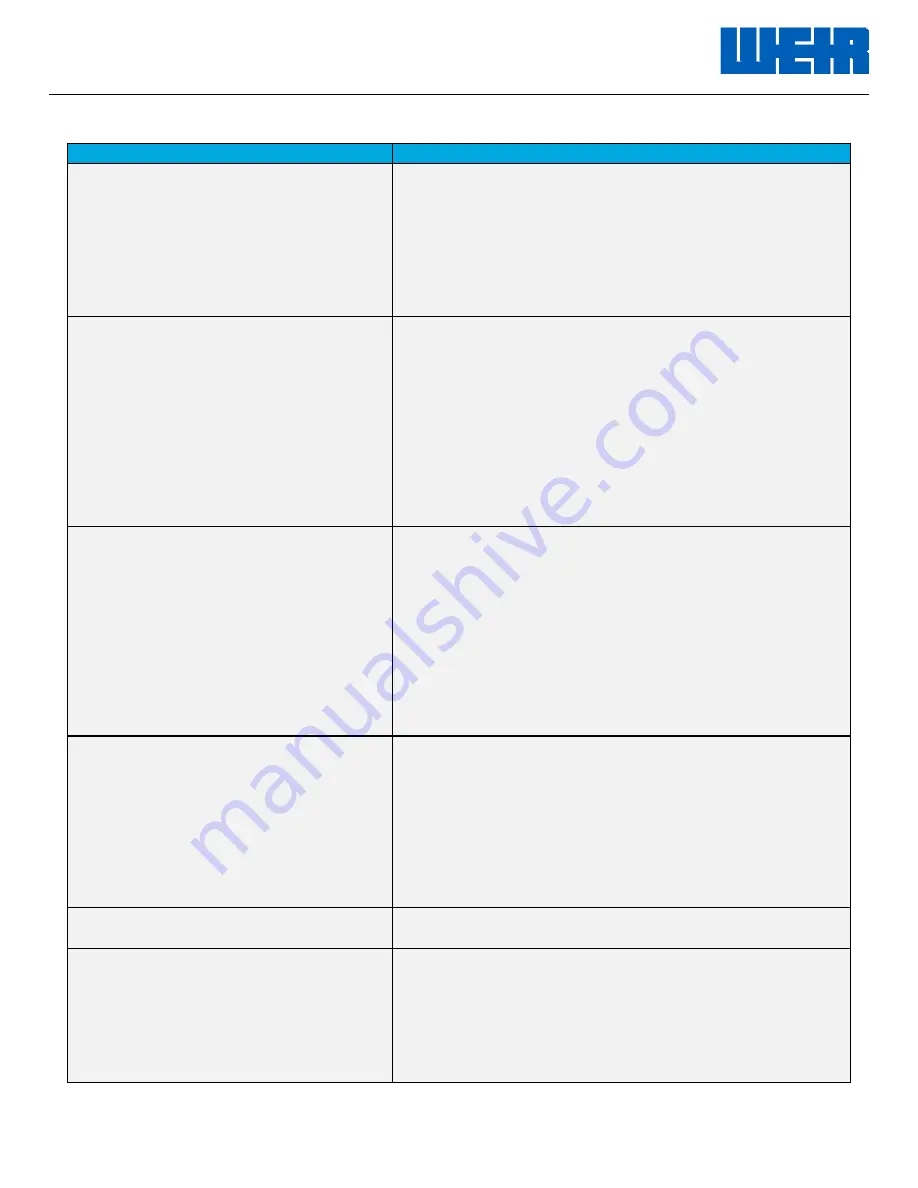
42 of 44
Document P/N:
2P137414
Release Date:
05/29/2017
Revision: IR
Troubleshooting Guide:
TROUBLE SYMPTOM:
PROBABLE CAUSE:
A.)
Abnormally high vacuum at power
end lube pump suction inlet (may
or may not be accompanied by
abnormally low oil pressure).
1. Extremely cold ambient temperature/dangerously high
oil viscosity.
2. Clogged lube system suction strainer.
3. Kinked or collapsed lube system suction hose.
4. Clogged oil reservoir breather.
5. Erroneous gauge reading.
6. Closed tank valve.
B.)
Abnormally low power end lube oil
pressure with normal to low
vacuum reading at lube pump
suction (may or may not be
accompanied by high oil
temperature).
1. Leak in lube pump suction piping, which allows air to be
drawn into the system.
2. Worn or damaged lube pump.
3. Leak in lube pump pressure piping.
4. Low oil level in reservoir.
5. Clogged oil filter element.
6. Faulty lube system relief valve.
7. Extremely hot lube oil temperature/dangerously low oil
viscosity.
8. Erroneous gauge reading.
C.)
Abnormally high power end lube
oil temperature (may or may not
be accompanied by low oil
pressure).
1. Extremely warm ambient temperature/dangerously low
oil viscosity/incorrect grade of gear oil.
2. Gear oil contaminated with water, trash, or air bubbles.
3. Plunger pump has been operated continuously for too
long a period of time at or near its maximum horsepower
or torque rating.
4. Heat exchanger or oil cooler malfunction.
5. Erroneous gauge reading.
6. Internal power end damage or power end wear.
7. Thermostatic valve malfunction.
D.)
Leaking power end oil seals.
1. Extremely cold ambient temperature/high oil viscosity.
2. Damaged seal surface on mating parts.
3. Clogged oil breather/high crankcase pressure.
4. Worn or damaged seal.
5. Contaminated lube oil.
6. Loose inspection cover bolts, torn inspection cover
gaskets, or sealing bonded inspection cover bolt
washers.
E.) Leaking lube lines.
1. Loose fittings, damaged hoses, damaged fittings.
F.)
Leaking fluid end seals.
1. Seal installed improperly.
2. Seal cut or pinched on installation.
3. Mating seal surface not cleaned properly prior to seal
installation.
4. Damaged or corroded mating seal surface.
5. Sealing part not properly tightened.
Содержание SPM QWS 2500 XL
Страница 12: ...12 of 44 Document P N 2P137414 Release Date 05 29 2017 Revision IR Performance Data ...
Страница 13: ...13 of 44 Document P N 2P137414 Release Date 05 29 2017 Revision IR ...
Страница 14: ...14 of 44 Document P N 2P137414 Release Date 05 29 2017 Revision IR ...
Страница 15: ...15 of 44 Document P N 2P137414 Release Date 05 29 2017 Revision IR ...
Страница 16: ...16 of 44 Document P N 2P137414 Release Date 05 29 2017 Revision IR ...
Страница 17: ...17 of 44 Document P N 2P137414 Release Date 05 29 2017 Revision IR ...
Страница 18: ...18 of 44 Document P N 2P137414 Release Date 05 29 2017 Revision IR ...
Страница 22: ...22 of 44 Document P N 2P137414 Release Date 05 29 2017 Revision IR ...
Страница 23: ...23 of 44 Document P N 2P137414 Release Date 05 29 2017 Revision IR ...
Страница 28: ...28 of 44 Document P N 2P137414 Release Date 05 29 2017 Revision IR Power End Lube System Schematic ...