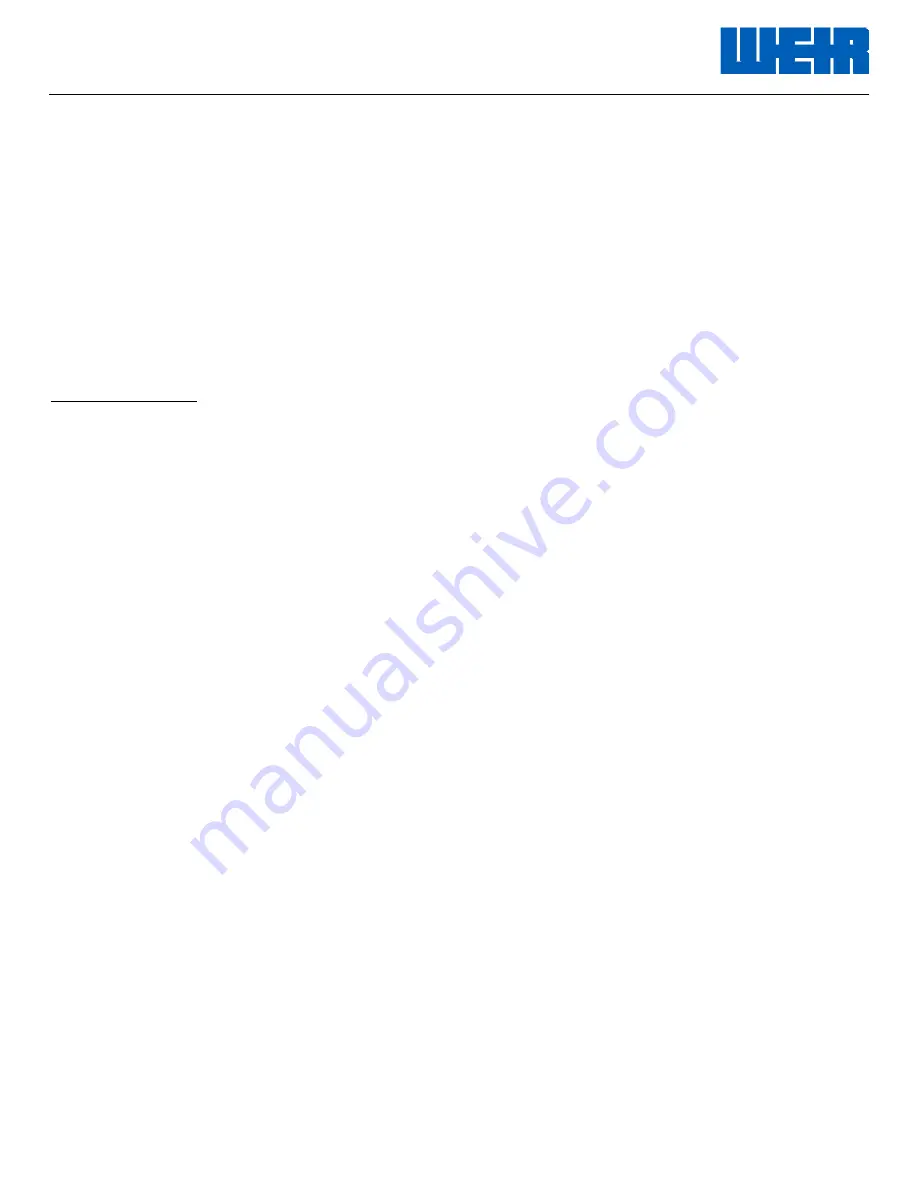
4 of 44
Document P/N:
2P137414
Release Date:
05/29/2017
Revision: IR
12. Any repairs or service (even routine maintenance) performed on the pump must be performed by a
trained service technician who is qualified to work on high pressure reciprocating plunger pumps. All
such service and repairs must be supervised by qualified management personnel or returned to Weir Oil
& Gas for service. Only SPM
®
replacement parts should be utilized
. Failure to do so may result in
loss
of warranty
as well as
SERIOUS INJURY OR DEATH
. Weir Oil & Gas
provides a Pump
Maintenance Mechanic Training School to qualify pump service mechanics.
13. SPM
®
well service pumps should never be used to pump gaseous, explosive, or uninhibited corrosive
fluids. These may result in equipment failure, leading to
INJURY OR DEATH.
14. Never place hands in area of reciprocating pony rod or plunger path. If work must be done in this area,
make sure pump is disengaged from driver and isolated from suction and discharge pressure prior to
initiating activity
(locked out and tagged out).
Special Precautions:
1. The modifications to or unauthorized repair of any part of an SPM
®
pump, or use of components not
qualified by Weir Oil & Gas, can lead to pump damage or failure and
SERIOUS INJURY OR DEATH.
2. The pump's fluid end and related piping must always be flushed with clean water after every job. If
freezing temperatures are anticipated the fluid cylinder must be completely drained of any fluid. Failure
to do this may result in fluid cylinder damage from fluids which have hardened or frozen.
3. All
SPM
®
threaded components are right hand threaded unless specifically designated otherwise. Any
turning counterclockwise will unscrew the assembly. Always make sure any threaded component is
made up properly with the proper torque.
4. All products should be properly cleaned, greased, or oiled after each use and inspected prior to each
use.
Do not put oil or grease on the valve seat, or fluid end valve seat tapered area.
5. Pressure seal (line pipe) threads are not recommended for pulsating service above 10,000 PSI or where
side loading or erosion are suspected. Non-pressure seal (round tubing) threads or straight integral
connections are recommended under these conditions. In order to achieve the recommended Non-
Shock Cold Working Pressure, power-tight make-up is required on all threaded connections. Consult
the factory for any usage other than normal constant flow working conditions. Integral connections are
recommended in lieu of pipe threaded connections for all pump applications.
6. Each integral union connection is clearly marked with a pressure code (i.e. “1502”, 15,000 psi). This
pressure must not be exceeded. This code should also be used with mating unions. Improper mating
can result in failures. All integral union connections used must match (according to size, pressure
rating, etc.). These connections must also match the service of the designated string they are installed
in.
Содержание SPM QWS 2500 XL
Страница 12: ...12 of 44 Document P N 2P137414 Release Date 05 29 2017 Revision IR Performance Data ...
Страница 13: ...13 of 44 Document P N 2P137414 Release Date 05 29 2017 Revision IR ...
Страница 14: ...14 of 44 Document P N 2P137414 Release Date 05 29 2017 Revision IR ...
Страница 15: ...15 of 44 Document P N 2P137414 Release Date 05 29 2017 Revision IR ...
Страница 16: ...16 of 44 Document P N 2P137414 Release Date 05 29 2017 Revision IR ...
Страница 17: ...17 of 44 Document P N 2P137414 Release Date 05 29 2017 Revision IR ...
Страница 18: ...18 of 44 Document P N 2P137414 Release Date 05 29 2017 Revision IR ...
Страница 22: ...22 of 44 Document P N 2P137414 Release Date 05 29 2017 Revision IR ...
Страница 23: ...23 of 44 Document P N 2P137414 Release Date 05 29 2017 Revision IR ...
Страница 28: ...28 of 44 Document P N 2P137414 Release Date 05 29 2017 Revision IR Power End Lube System Schematic ...