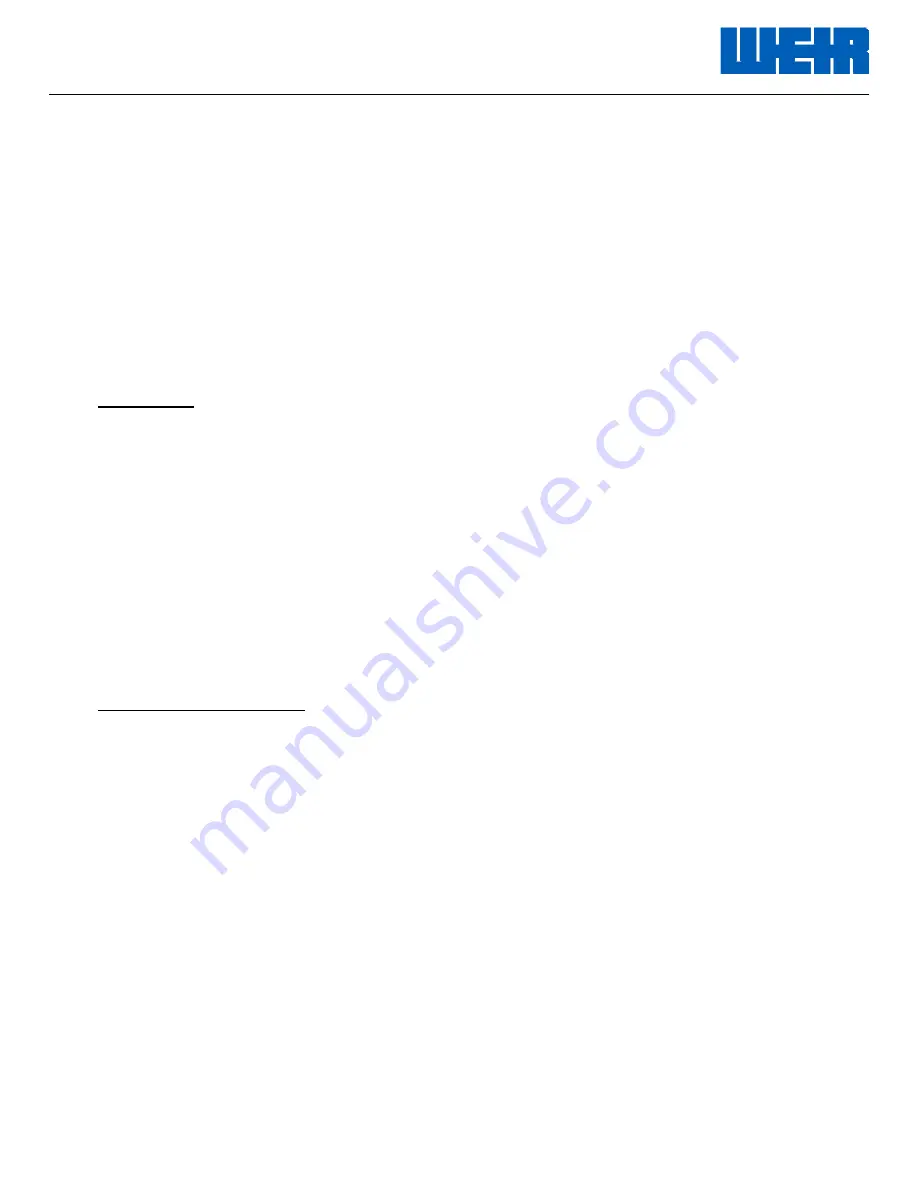
25 of 44
Document P/N:
2P137414
Release Date:
05/29/2017
Revision: IR
Power End Lube System Requirements:
Providing a well-designed trouble-free power end lube system is one of the most important factors in obtaining
maximum service and long life from the SPM
®
QWS 2500 XL Well Service Plunger Pump. Due to the nature of
well servicing operations, the highest pump pressures and highest load conditions typically occur at very slow
pump speeds. This characteristic of well service pump operation necessitates the use of an engine driven lube
pump that will deliver maximum lube oil volume at high engine speeds regardless of slow pump speeds. As a
result of this operating characteristic and the many different equipment design possibilities, it is not feasible for
SPM
®
to provide a power end lube system with the pump. The equipment manufacturer who builds the
powered well service unit must provide power end lube system components that are compatible with the
specific engine, transmission, etc. being utilized on the unit.
A properly designed power end lube system will meet the following specifications:
1. Oil
Reservoir:
A.
Must be of 125 gallon capacity minimum. This can change depending on pump model.
B.
Suction outlet to be 3” minimum and located as deep as possible.
C.
Suction outlet and return inlets to be as far apart as possible.
D.
Return fitting for drain lines back to tank to be 3” minimum; return fitting for relief valve line to be 1”
minimum.
E.
A serviceable magnet located near the 3” return port is highly recommended.
F.
Breather/filler cap to be 40 micron/25CFM minimum and should include a built-in strainer to prevent
trash from entering the reservoir.
G.
Dipstick or sight glass to indicate oil level in the reservoir.
H.
Reservoir must be located below the lowest drain port in the plunger pump and as near the plunger
pump as possible (preferably directly underneath).
I.
A small air space should be designed into the tank. (See power end lube startup and performance
data)
J.
A removable cover to allow access to the tank for clean out will assist in preventative maintenance.
2.
Lube System Suction Piping:
A.
Must be 3” I.D. minimum throughout so that the suction flow velocity never exceeds 2 to 3 ft. per
second.
B.
Must include a suction strainer w/3” minimum port size, 40 to 100 mesh (400-150 micron) wire
cloth, 500 sq. in. minimum element area, 3 to 5 PSI (6 to 10 Hg) built-in bypass, and rated at 90
GPM minimum flow. An in-line wye type strainer is much preferred due to the ease of routine
maintenance in cleaning the element.
C.
A 3” minimum swing type check valve may be used in the suction line if the lube pump is located
above the fluid level in the reservoir.
D.
The suction line should be as short as possible, should be free from excessive bends, and should
be wire reinforced to prevent collapsing. If longer than 10 ft. the resulting friction losses should be
compensated for by increasing the line size to 3” I.D. minimum.
E.
The use of a 3” full flow isolation valve will assist in shutting off the line. The shutting off the 3” line
will allow for strainer maintenance without draining the tank.
Содержание SPM QWS 2500 XL
Страница 12: ...12 of 44 Document P N 2P137414 Release Date 05 29 2017 Revision IR Performance Data ...
Страница 13: ...13 of 44 Document P N 2P137414 Release Date 05 29 2017 Revision IR ...
Страница 14: ...14 of 44 Document P N 2P137414 Release Date 05 29 2017 Revision IR ...
Страница 15: ...15 of 44 Document P N 2P137414 Release Date 05 29 2017 Revision IR ...
Страница 16: ...16 of 44 Document P N 2P137414 Release Date 05 29 2017 Revision IR ...
Страница 17: ...17 of 44 Document P N 2P137414 Release Date 05 29 2017 Revision IR ...
Страница 18: ...18 of 44 Document P N 2P137414 Release Date 05 29 2017 Revision IR ...
Страница 22: ...22 of 44 Document P N 2P137414 Release Date 05 29 2017 Revision IR ...
Страница 23: ...23 of 44 Document P N 2P137414 Release Date 05 29 2017 Revision IR ...
Страница 28: ...28 of 44 Document P N 2P137414 Release Date 05 29 2017 Revision IR Power End Lube System Schematic ...