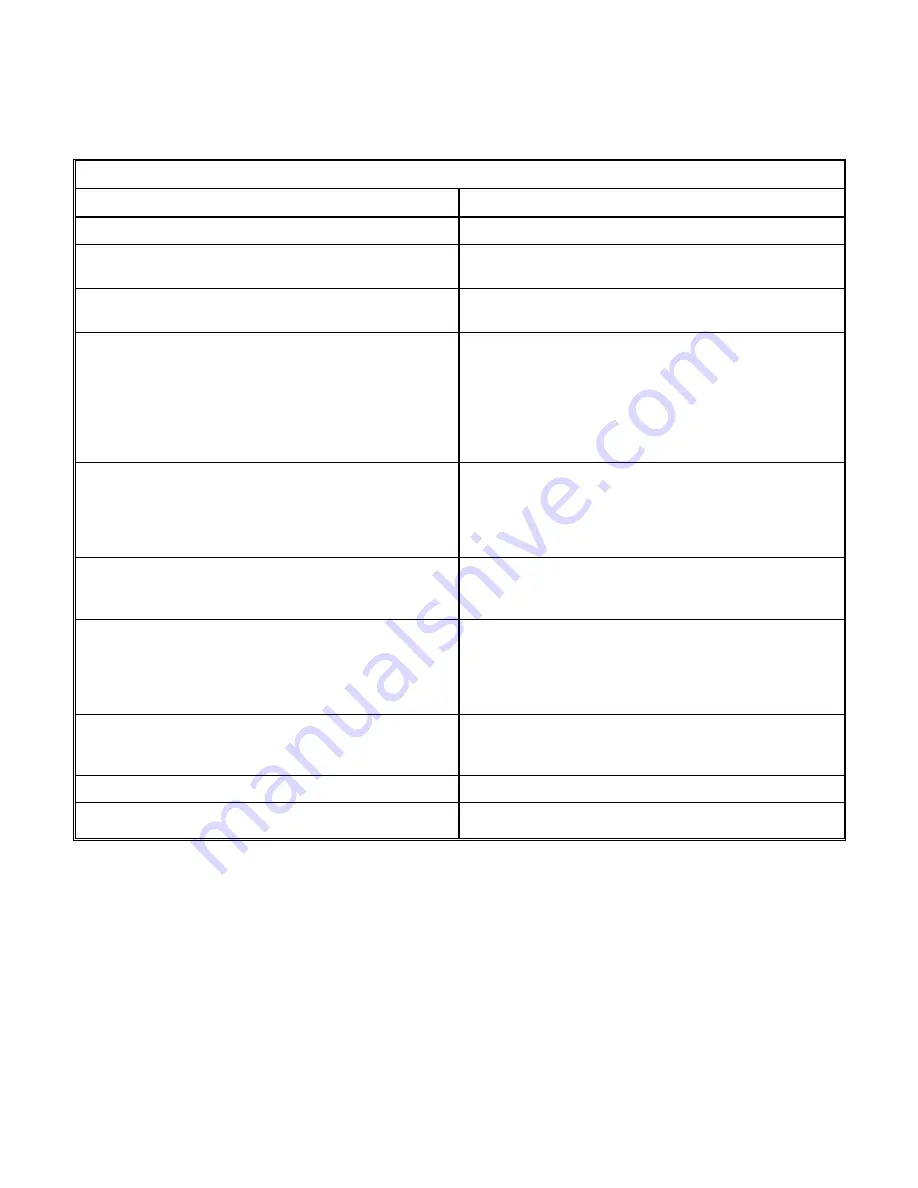
26
V.
TROUBLESHOOTING
A.
NO LIQUID DELIVERED AT END DELIVERY POINT OR THROUGH FLOW METER
Possible Causes
Corrective Action
1. Inlet or discharge valves closed
Be sure all valves are fully opened.
2. Lack of prime.
Fill pump and suction completely with liquid. Check for
vapor bind.
3. Obstruction in liquid passages.
Dismantle pump and inspect passages of pick-up tube,
rotor cover and manifold. Remove obstruction.
4. System head too high.
Total system head greater than head for which pump
designed. Check pipe friction losses. Larger piping
may correct condition. Are valves wide open? Increase
pump speed to develop greater differential pressure.
CAUTION – Brake HP of pump varies as the cube of
the speed; therefore, any increase in speed means
considerable increase in the power demand.
5. Suction Lift Too High
If no obstruction at inlet, check for pipe friction losses.
However, static lift may be too great. Measure with
mercury column or vacuum gauge while pump
operates. If static lift is too high, liquid to be pumped
must be raised or pump lowered.
6. Air Leak in Suction Line
Suction line can be tested by shutting off or plugging
inlet and putting line under pressure. A gauge will
indicate leak with a drop of pressure.
7. Speed Too Low.
Slipping drive belts – check belt tension. Check drive
sheave and verify correct size for required speed.
Check whether motor is directly across-the-line and
receiving full voltage. Frequency may be incorrect,
motor may have an open phase.
8. Wrong Rotation.
Check motor rotation with required pump rotation.
Pump rotation is clockwise viewed from the manifold
end of pump.
9. Suction or Discharge Line Plugged.
Unplug line.
10. Gas or Vapor Pocket in Suction Line.
Provide gas separation chamber on suction line.