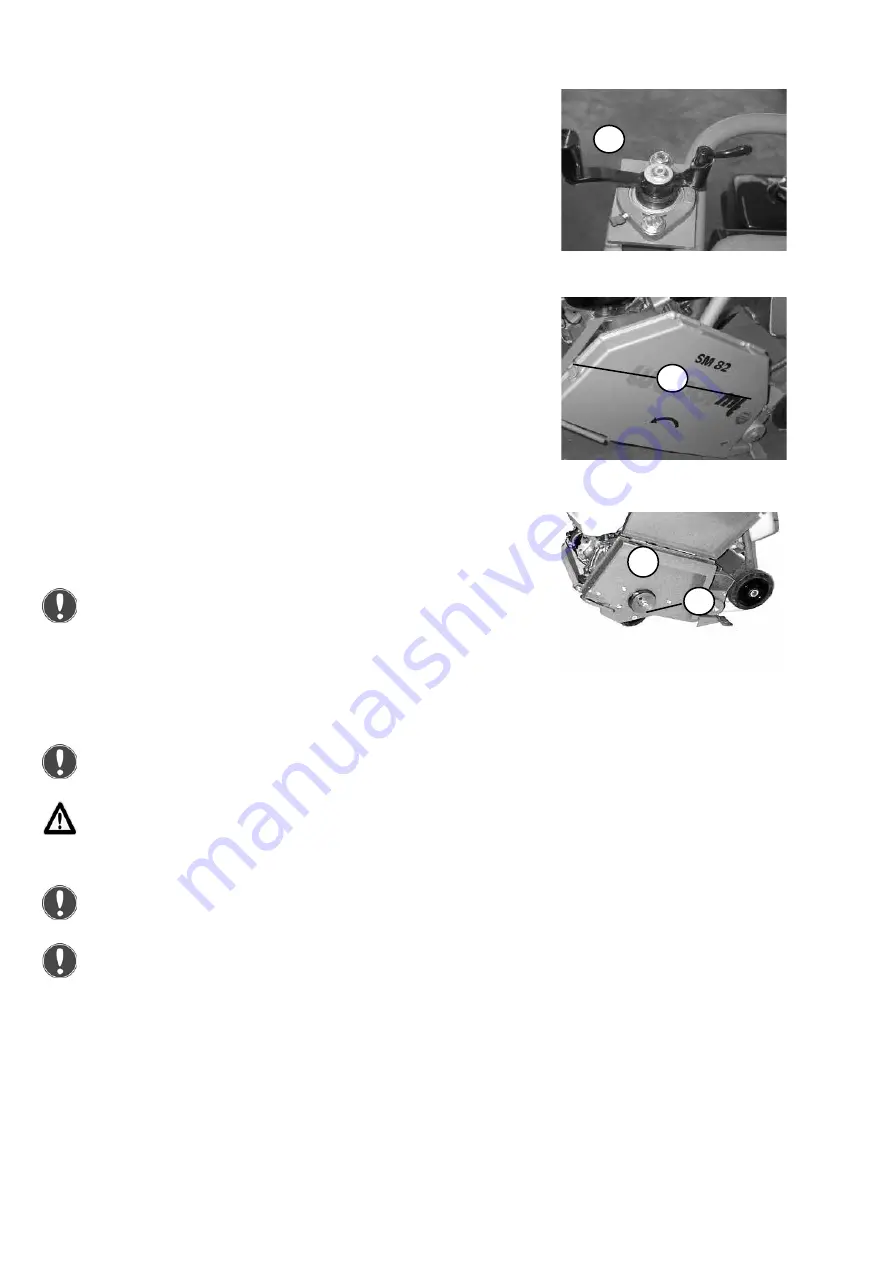
14
1
Install the cutting disk
Turn the cutting disk protection into the highest position with
the crank (1).
Open the cutting disk protection by releasing both clamps (1).
Unscrew the securing screw (1).
Remove the flange cover (2) with the ring flange and sealing
ring from the hub.
After removing the parts, clean them thoroughly and check
them for damage.
2
1
Installing the cutting disk
Fit the cutting disk as follows:
Sealing ring, ring flange, cutting disk, flange cover. The
flange cover must be fastened with the Allen screw.
The support surface of the clamping disk and the hub
must be free of notches and any other damage. Otherwise
the cutting disk might wobble.
The cutting disk must be flat on the hub. The grooved pin
locks the cutting disk in its cutting direction.
When installing the cutting disk, the arrows of the cutting
disk and the cutting disk protection must point in the
same direction.
1
Содержание SM 82-3
Страница 1: ...1 Operating and Maintenance Manual SM 82 3 0401703...
Страница 2: ...2...
Страница 11: ...11 1 Description 2 Type 3 Serial number 4 Year of manufacture 5 Weight 6 Rated power kW 2 1 3 4 5 6...
Страница 24: ...24...
Страница 25: ...25...
Страница 26: ...26...
Страница 27: ...27...