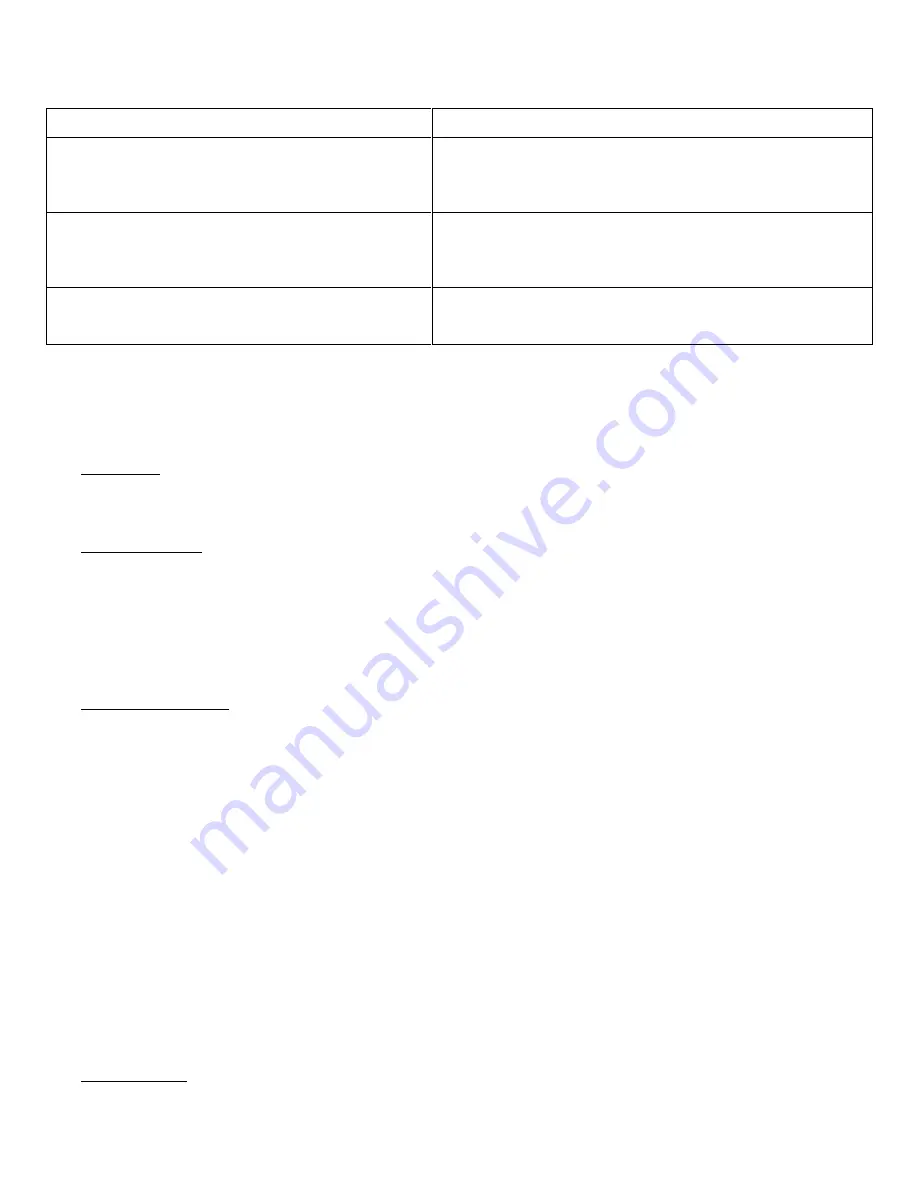
30
Table 8: Troubleshooting Chart Electronic Pilot Ignition
(For Burners Utilizing Fenwal Control)
PRELIMINARY CHECKS, DIAGNOSIS AND SERVICE HINTS
(ELECTRONIC PILOT IGNITION)
Although the following tests can be made using standard volt meter, it is quicker and more convenient to use a Fenwal Model 0 5-
125539-001 Test Adapters.
1.
Input Polarity
If a spark is present and the gas valve opens for the flame establishing period but the control locks without sensing flame, check
the input voltage at terminals 1 and 6 for the proper polarity. Terminal TH or 24V should be “hot”; 24VAC (05-16) with respect to
ground. Terminal GND is neutral, or zero voltage, with respect to ground.
2.
Improper Grounding
If a flame is present during the Trial for Ignition period but the system shuts down, ensure that the burner is properly grounded. If
the burner is not grounded, the flame monitoring signal will not function and the system will go into lockout. Check for loose or
corroded terminals and replace if necessary. Ensure good electric connection by scraping paint or any other foreign matter off the
area where ground connection is made.
It is equally important to be certain that the electrode bracket assembly is properly grounded. The bracket should be common with
the ground lead on the input connector (ground terminal 6). If the bracket is not properly grounded, damage to the ignitor can
result.
3.
Inoperative High Voltage
If there is no spark or sparking is intermittent, check the following after disconnecting voltage to the system.
a.
Check spark gap. Gap should be 1/8 (3.2mm) +/- 1/32”(.8mm) form H.V. to ground.
CAUTION:
NEVER REPLACE THE COMPONENT BOARD WITHOUT FIRST CHECKING TO ENSURE THAT THE ELECTRODE
HAS THE PROPER GAP. IF THE GAP IS TOO WIDE, DAMAGE TO THE IGNITOR CAN RESULT.
b.
Check electrode leads and determine there is no corrosion at the terminals. If there is corrosion, clean it off.
DO NOT USE
LIQUIDS TO CLEAN TERMINALS.
Use steel wool or emery cloth to clean.
c.
Check ceramic insulators for cracks, foreign matter, and carbon. If there are cracks, replace electrodes. If there is carbon or
foreign matter, clean it off.
DO NOT USE LIQUIDS TO CLEAN.
Use steel wool or emery cloth to clean.
d.
Check high voltage lead wire for cracks or breaks. If there are cracks, breaks or chafing, replace high voltage wire.
e.
Check to ensure that the high voltage terminal is clear of dust, moisture or any foreign matter that could create high voltage
leakage to ground.
4.
Valve Malfunction
With power applied to the ignitor, sparking should occur and the solenoid valve should open simultaneously. If sparking occurs but
the valve does not open, place a volt meter between Terminal PV1 and ground (or across valve). If valve does not function with
Symptoms
Possible Causes
1. PILOT DOES NOT LIGHT.
a. Air in gas line.
b. High or low gas pressure.
c. Blocked pilot orifice.
d. Broken or damaged ignition cable.
2. MOTOR DOES NOT RUN.
a. Thermostat or limit defective or improperly set.
b. Relay or transformer defective.
c. Motor burned out.
d. Improper wiring.
3. MOTOR RUNNING BUT NO FLAME.
a. Very low or no gas pressure to pilot.
b. High gas pressure to pilot.
c. Defective regulator.
Содержание P250 series
Страница 35: ...35 FIGURE 23 WIRING DIAGRAMS FOR GAS BURNER WITH DIRECT IGNITION FENWAL...
Страница 36: ...36 FIGURE 24 WIRING DIAGRAMS FOR GAS BURNER WITH ELECTRONIC PILOT HONEYWELL...
Страница 37: ...37 FIGURE 25 WIRING DIAGRAMS FOR GAS BURNER WITH ELECTRONIC PILOT NO T STAT...
Страница 38: ...38 FIGURE 26 WIRING DIAGRAMS FOR GAS BURNER WITH ELECTRONIC PILOT FENWAL...
Страница 46: ...46 NOTES...