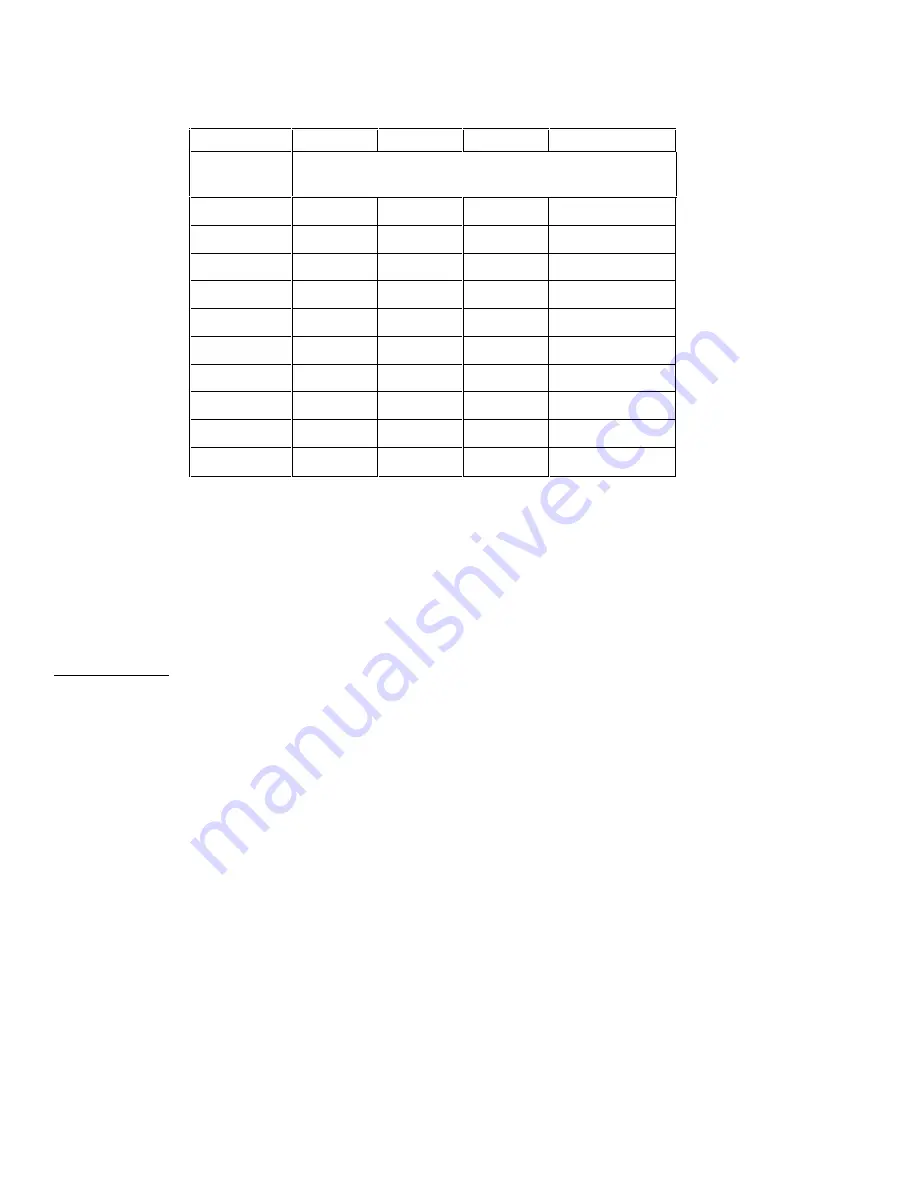
18
Table 7: Pipe Sizing Chart for Liquid Propane (11” w.c.) with Copper Tubing
The following chart is based on
11” w.c.
inlet pressure and a pressure drop of
0.5” w.c..
Maximum Capacity of Tube Size in Btu per Hour
Pipe Size
1/2”
5/8”
3/4”
7/8”
Length
(feet)
Maximum Capacity in Btu/hr
10
110,000 206,000 348,000
536,000
20
76,000 141,000 239,000
368,000
30
61,000 114,000 192,000
296,000
40
52,000
97,000 164,000
253,000
50
46,000
86,000 146,000
224,000
60
42,000
78,000 132,000
203,000
70
38,000
71,000 120,000
185,000
80
36,000
67,000 113,000
174,000
90
33,000
62,000 105,000
161,000
100
32,000
59,000 100,000
154,000
NOTE:
Copper tubing shall comply with standard type K or L of ASTM B 88 or ASTM B 280.
TESTING PIPING FOR LEAKS
Before turning gas under pressure into piping, all openings from which gas can escape should be closed. Immediately after
turning on gas, the system should be checked for leaks. This can be done by watching the 1/2 cubic feet test dial and allowing 5
minutes to show any movement, or by soaping each pipe connection and watching for bubbles. If a leak is found, make the
necessary repairs and repeat the above test. Defective pipes or fittings should be replaced and not repaired.
Never use a flame
or fire in any form to locate gas leaks, use a soap solution.
After the piping and meter have been checked completely, purge the system of air. Do not bleed the air inside the furnace. Be sure to
relight all the gas pilots on other appliances.
ELECTRICAL WIRING OF BURNER
The conversion burner is shipped completely wired. It is only necessary to supply the 115 volt circuit, thermostat and limit circuit. All
wiring must conform with the National Electric Code or the code legally authorized in the locality where the installation is being made.
The burner, when installed, must be electrically grounded in accordance with local codes or, in the absence of local codes, with the
latest edition of the National Electrical Code, ANSI/NFPA No. 70. See wiring diagrams in Figure 22 through Figure 26 for reference on
wiring, thermostat connection, and limit circuit. If an external electrical source is utilized, the conversion burner, when installed, must be
electrically grounded in accordance with local codes or, in the absence of local codes, with the latest edition of the National Electrical
Code ANSI/NFPA No. 70.
The burner ships with a jumper wire on the thermostat (T-T) terminals. Jumper needs to be removed for remote thermostat control and
the thermostat needs to be connected per wiring diagrams. T-T terminal is an open/close switch for the burner and no voltage should
be connected to it. For boilers it may be necessary to leave the T-T terminal jumped as the aquastat may be providing the voltage to the
burner and controlling when voltage is sent to the burner. The burner is controlled by the appliance. Once wiring is complete between
burner and appliance, verify appliance is controlling the burner’s on/off operation. When connecting the burner to the 120 volt electrical
supply, utilize the knockout provided on the burner’s junction box.
Содержание P250 series
Страница 35: ...35 FIGURE 23 WIRING DIAGRAMS FOR GAS BURNER WITH DIRECT IGNITION FENWAL...
Страница 36: ...36 FIGURE 24 WIRING DIAGRAMS FOR GAS BURNER WITH ELECTRONIC PILOT HONEYWELL...
Страница 37: ...37 FIGURE 25 WIRING DIAGRAMS FOR GAS BURNER WITH ELECTRONIC PILOT NO T STAT...
Страница 38: ...38 FIGURE 26 WIRING DIAGRAMS FOR GAS BURNER WITH ELECTRONIC PILOT FENWAL...
Страница 46: ...46 NOTES...