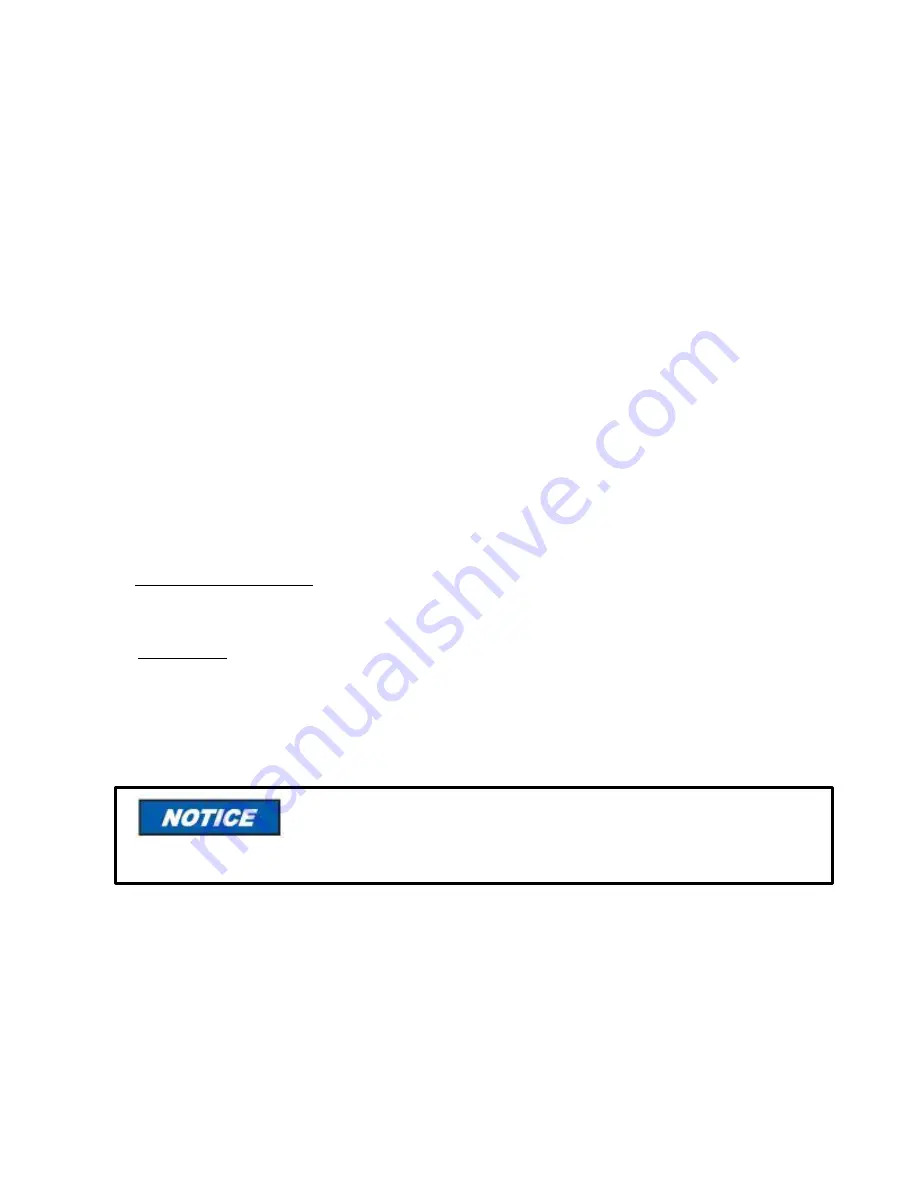
24
3. Turn on the main electrical power and set the thermostat or operation control to call for heat. Allow the
burner to run a MINIMUM of 5 minutes to purge combustion chamber and appliance heat exchanger.
4.
Set the thermostat or operating control below room temperature, shutting the burner “OFF” for 1
minute. This is will reset the primary control.
5.
Depress the combination gas valve manual control now and turn to “ON” position.
6. Set the thermostat or operating control to call for heat. The burner will start and go through the
applicable sequence of burner/primary gas control operation.
7. On new gas line installations, air may be trapped in the line, the burner may experience several
lockouts until all the air is purged from the lines. If the burner goes into lockout, it may be reset by
adjusting the thermostat or operating control below room temperature for a few seconds, then
readjusting to call for heat.
8. Once burner is running set the manifold pressure by
adjusting the gas valve’s pressure regulator while
measuring the gas pressure using a manometer. The correct operating manifold orifice pressure range
for both natural and LP
gas is 2.0” w.c. (498 Pa) minimum to 4.0” w.c. (996 Pa) maximum. By
adjusting the pressure regulator between 2.0” w.c. (498 Pa) minimum to 4.0” w.c. (996 Pa) on either
natural or LP gas, a wide input range can be achieved with a single orifice size. If the desired input
rating cannot be obtained within the above manifold orifice pressure adjustment range, the next size
larger or smaller orifice should be used (Refer to orifice chart Figure 11).
9. A more accurate Btu/hr (kW) input can be determined by using the natural gas service meter with only
the burner on (all other gas appliances should be off). The hand on the gas meter dial with the lowest
cubic feet valve (fastest revolving dial), should be clocked for one complete revolution and use the
formula listed below where one complete revolution on the gas meter is equal to one cubic foot of gas.
3600 x
ft
3
per rev. x Btu value/
ft
3
= Btu/hr (kW)
Seconds per revolution
EXAMPLE:
3600 x 1 x 1000 = 300,000 Btu/hr (87.9 kW)
12
COMBUSTION ADJUSTMENT OF BURNER
All adjustments below must be made with the following equipment:
1. Draft Gauge
3. CO Tester
2. O
2
or CO
2
Analyzer 4. Water Column Gauge
ALWAYS USE RELIABLE COMBUSTION TEST INSTRUMENTS.
BEING PROFICIENT IN THE USE OF THESE INSTRUMENTS AND INTERPRETING THEIR DATA
IS NECESSARY FOR SAFE, RELIABLE, AND EFFICIENT BURNER OPERATION.
1. After the burner has been in operation for at least 10 minutes and the off cycle damper and primary air
shutter were set per Figure 18, assuring combustion chamber and heat exchanger are fully warmed,
take combustion analysis flue gas samples just ahead of the draft control in the flue pipe. See step 2
for recommended values.
2.
For natural gas applications
, best performance will be achieved with a CO
2
setting of 8% to 10%
(3% to 6.5% O
2
) and
CO should be minimized with a goal of 100 ppm or less.
In no case should CO be above 400 ppm
Air Free.
For LP gas applications
, best performance will be achieved with a CO
2
setting of 9.5% to 11.8% (3%
to 6.5% O
2
) and CO should be minimized with a goal of 100 ppm or less.
In no case should CO be
above 400 ppm Air Free.
Содержание HSG200
Страница 30: ...30 Figure 20 Flame Current Measurement Top Wayne control Bottom Honeywell control...
Страница 48: ...48 Figure 29 continued Junction Box Assemblies Exploded Figure 30 Motor Assembly Exploded...
Страница 49: ...49 Figure 31 Gun Assembly Exploded Figure 32 HSG Series Burner Exploded...
Страница 50: ...50 Figure 33 Outer Dimensions of HSG Series Burner 13 2 335 mm REF 7 7 in 195mm 7 in 178 mm 15 25 in 377 mm...
Страница 52: ...52 NOTES...