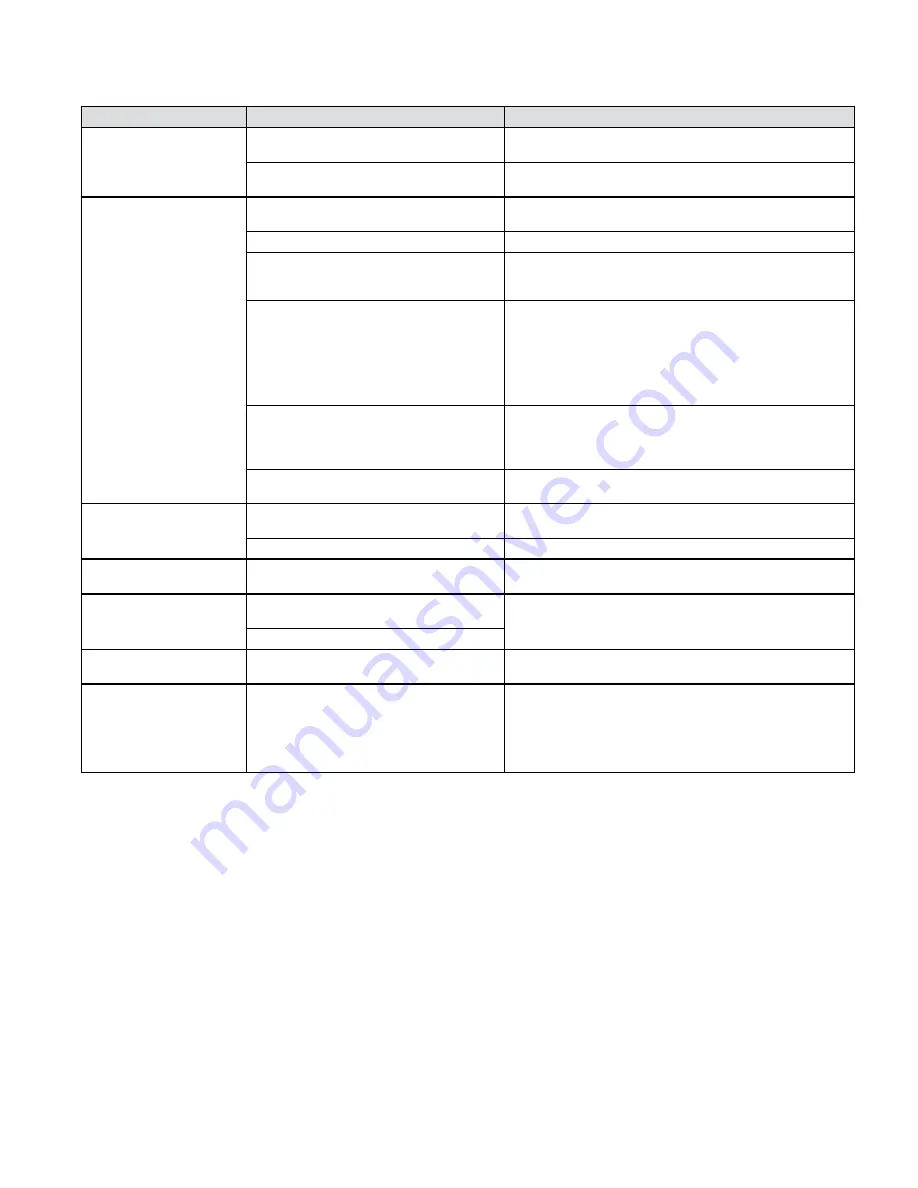
7
Problem
Cause
Solution
Valve spits periodically
from the vent.
Fluctuating supply pressure.
Install a soft seated check valve immediately upstream of
the de vice.
Fluctuating downstream pressure.
Install a soft seated check valve downstream of the device,
as close as possible to the shutoff valve.
Valve drips continually
from the vent.
Fouled first check.
Flush valve. If flushing does not resolve problem, disassemble
valve and clean or re place the first check.
Damaged or fouled relief valve seat.
Clean or replace the relief valve seat.
Relief valve piston O-ring not free to move
due to pipe scale, dirt, or build
up of mineral deposits.
Clean, grease, or replace the piston O-ring.
Excessive back pressure, freezing, or water
hammer has distorted the second check.
Elim i nate source of excessive backpressure or water hammer
in the system downstream of the device. Use Watts No. 15
to eliminate water hammer. Replace defective second check
assembly.
In case of freezing, thaw, disassemble, and inspect internal
components.
Replace as necessary.
Electrolysis or relief valve seat or first
check seats.
Replace relief valve seat or inlet cover.
Electrically ground the piping system and/or electrically
isolate the device with plastic pipe immediately upstream
and down stream of the device.
Valve improperly reassembled.
If valve is dis as sem bled during installation, exercise caution
when reinstalling check springs in their proper location.
Valve exhibits high
pressure drop.
Fouled strainer.
Clean strainer element or replace.
Valve too small for flows encountered.
Install proper size device based upon flow requirements.
No water flows down-
stream of valve.
Valve installed backward.
Install valve in accordance with flow direction arrow.
Valve does not test properly. Manufacturer’s test procedure not followed. Clean or replace gate valve with full port ball valves or
resilient wedge shutoff valves.
Leaky downstream gate valve.
Valve quickly and repeatedly
fouls following servicing.
Debris in pipeline is too fine to be trapped
by strainer.
Install finer mesh strainer element in the strainer.
Performance of backflow
preventers affected during
winter season.
Cold temperatures.
Electric heat-tape wrap closely together around the valve
body. Build a small shelter around the valve with a large
light bulb installed and left on at all times.
If the supply line is not used during the winter, removal of
the com plete body is the best. This creates an air gap to
eliminate any possible backflow.
Troubleshooting