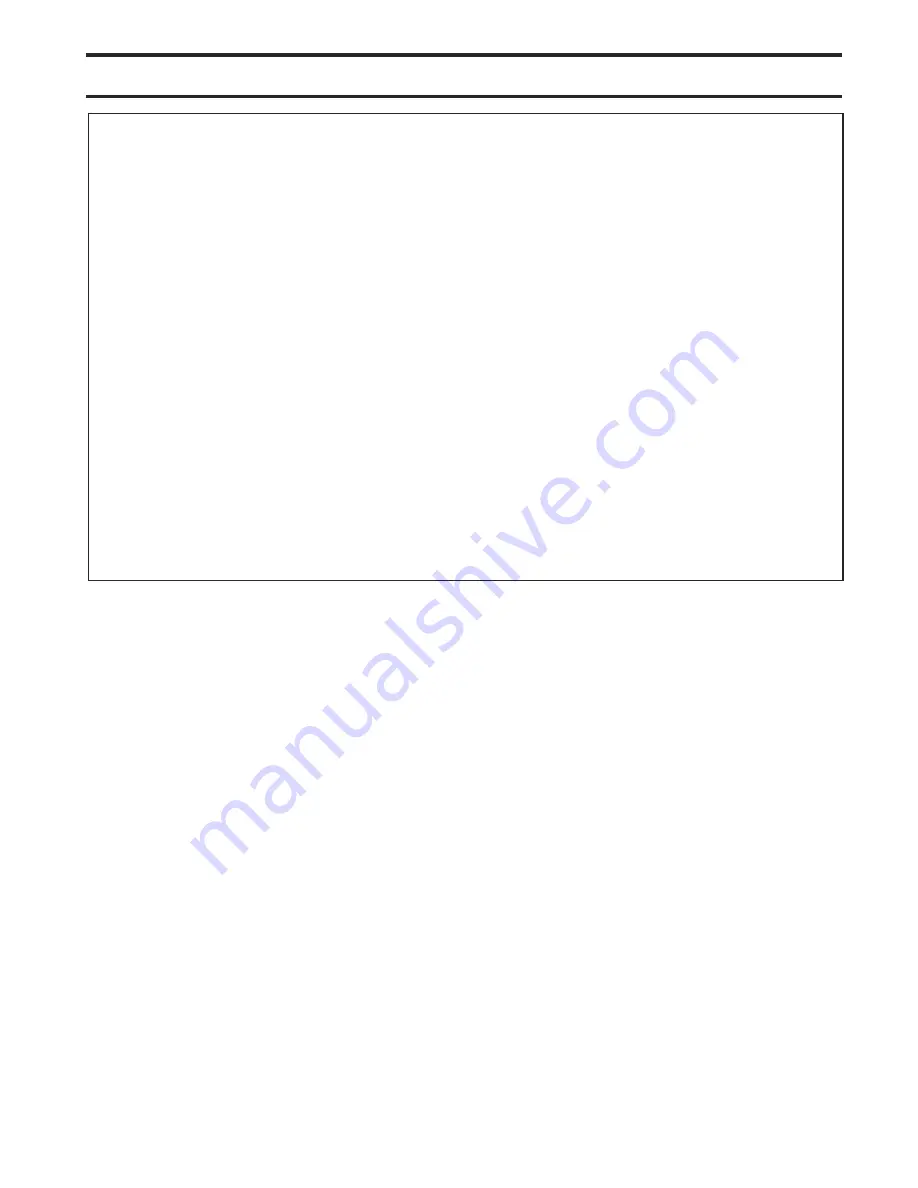
3
INTRODUCTION
General Warnings
The control valve, fittings and, or bypass are designed to
accommodate minor plumbing misalignments but are not
designed to support the weight of a system or the
plumbing.
Do not use Vaseline, oils, other hydrocarbon lubricants or
spray silicone anywhere. A silicon lubricant may be used on
black o-rings but is not necessary.
Avoid any type of lubri-
cants, including silicone, on red or clear lip seals.
The nuts and caps are designed to be unscrewed or tight-
ened by hand or with the special plastic wrench. If necessary
a pliers can be used to unscrew the nut or cap. Do not use
a pipe wrench to tighten or loosen nuts or caps. Do not place
screwdriver in slots on caps and/or tap with a hammer.
Do not use pipe dope or other sealants on threads, Teflon
tape must be used on the threads of the 1" NPT elbow or the
1/4" NPT connection and on the threads for the drain line
connection. Teflon tape is not necessary on the nut connec-
tion or caps because of o-ring seals.
After completing any valve maintenance involving the drive
assembly or the drive cap assembly and pistons, press the
NEXT and REGEN buttons for 3 seconds or unplug power
source jack
from the printed circuit board (black wire) and
plug back in. This resets the electronics
and establishes the service piston positions. The display
should flash all wording, then flash the software version (e.g.
154) and then reset the valve to the service position.
All plumbing should be done in accordance with local plumb-
ing codes. The pipe size for the drain line should be a mini-
mum of 1/2". Backwash flow rates in excess of 7 gpm or
length in excess of 20' require 3/4" drain line.
Solder joints near the drain must be done prior to connect-
ing the drain line flow control fitting. Leave at least 6"
between the drain line control fitting and solder joints when
soldering pipes that are connected on the drain line control
fitting. Failure to do this could cause interior damage to the
drain line flow control fitting.
When assembling the installation fittings package (inlet and
outlet),
connect the fitting, to the plumbing system first and
then attach the nut, split ring and o-ring. Heat from soldering
or solvent cements may damage the nut, split ring or o-ring.
Solder joints should be cool and solvent cements should be
set before installing the nut, split ring, and o-ring. Avoid get-
ting primer and solvent cement on any part of the o-rings,
split rings, bypass valve or control valve.
Plug into an electrical outlet. Note: All electrical connections
must
be connected according to local codes. (Be certain the
outlet is
uninterrupted.)
Install grounding strap on metal pipes.
Softening of water by the exchange process involves the
exchange or substitution of the hardness minerals, chiefly calci-
um and magnesium, for sodium minerals. The exchange is made
possible because the minerals are ionic in nature (often called
ionized impurities) which means they have an electrical charge.
The ion exchange process is based on the fact that like charges
repel one another, and unlike charges attract.
Calcium and magnesium ions in water are actually dissolved
rock. They have been dissolved by water, the “universal solvent”,
as it trickles down through strata of rock and soil it dissolves cal-
cium and magnesium deposits. This dissolved rock eventually
finds its way into an underground aquifer and when water from
the aquifer is pumped to the surface, it contains the dissolve
hardness minerals of calcium and magnesium and is said to be
hard water.
An ion exchange softener exchanges the hardness minerals, cal-
cium, and magnesium, for sodium, from the softener resin.
Sodium is less objectionable because it does not build up on sur-
faces as scale deposits.
All three minerals are positively charged ions called cations. The
exchange takes place by passing water containing hardness
minerals over a man-made ion exchange resin contained in a
suitable tank. The resin, polystyrene divinyl benzene in most-
modern softeners, consist of millions of tiny plastic beads, all of
which contain many negatively charged exchange sites to attract
the positive cations. When the resin is in the regenerated
state
these negatively charged exchange sites hold positively charged
sodium cations.
As the calcium and magnesium contact the resin beads in their
travel through the resin tank, they displace the sodium ions from
the exchange sites. During the ion exchange process, relatively
small amounts of other strongly charged cations such as iron
and manganese are also removed along with the calcium and
magnesium.
Ion exchange is possible for two reasons: (1) All cations do not
have the same strength of positive charge and (2) the resin
prefers the stronger charged cations calcium and magnesium
than it does the weaker sodium cations.
The exchanged sodium cations pass downward through the
resin “bed” and out the softener outlet, thus, the softener delivers
“soft”water.
Eventually, all of the resin exchange sites are occupied by calci-
um and magnesium and no further exchange can take place. The
resin is said to be exhausted and must be regenerated.
The softener resin is regenerated with a dilute brine solution of
sodium chloride (common salt) and water. During regeneration
the flow of service water from the softener is first stopped. Brine
is drawn from the brine tank mixing with a separate stream of
water. The brine solution flows through the resin, contacting the
resin beads loaded with calcium and magnesium ions. Even
though the calcium and magnesium are more strongly charged
than the sodium, the concentrated brine solution contains
literally billions of weaker charged sodium ions which have the
power
to displace the smaller number of calcium and magnesium
ions. When the calcium and magnesium ions are displaced, the
positive sodium ions are attracted to the negative exchange sites
is said to be regenerated and ready for the next softening cycle.
Principles of Softening and Ion-Exchange