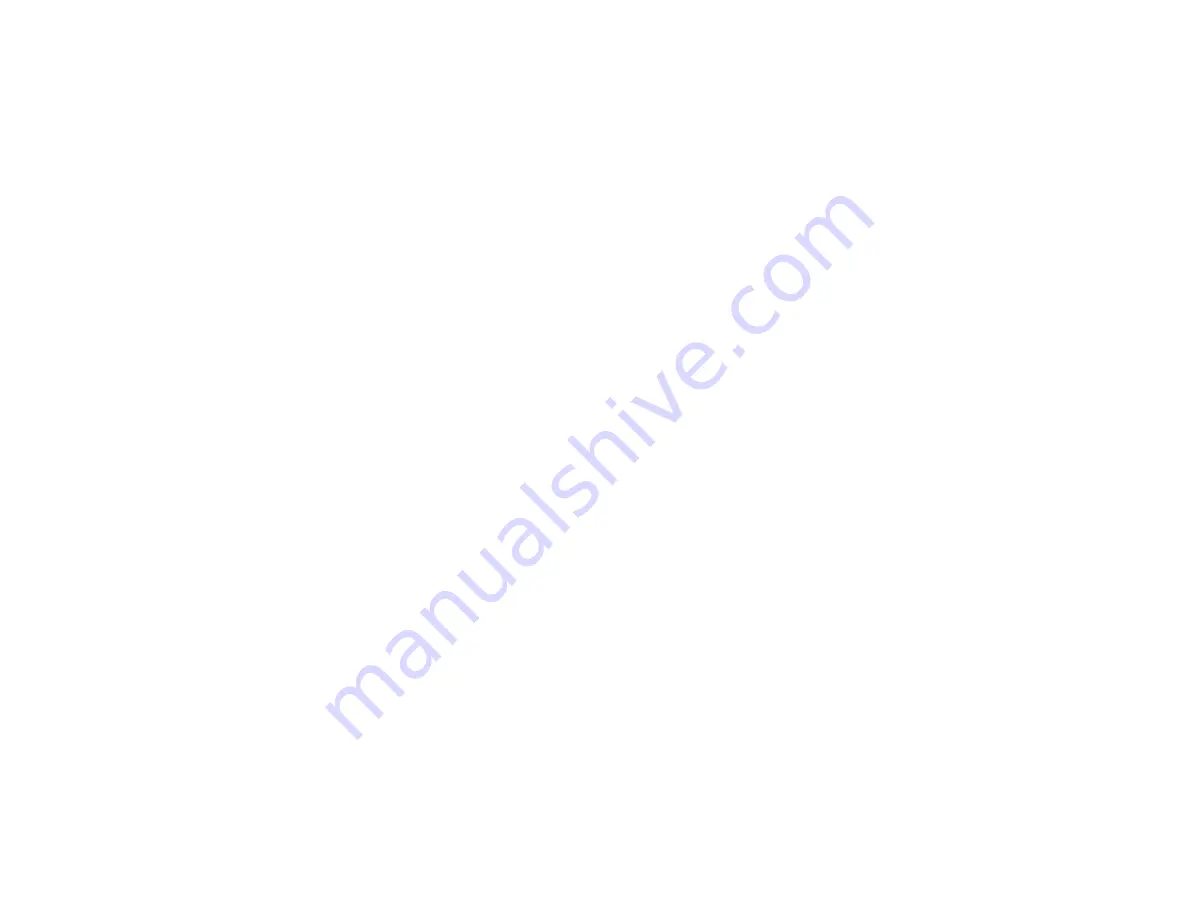
F-1031, Section 4307
Page 11 of 12
Reassembly of Miscellaneous Parts
Tachometer Drive
1.
Install tachometer driven gear (T89) in drive shaft housing (T11) making
sure it fits into bushing (T88) previously installed in the housing.
2.
Install sleeve (T90) over end of gear (T89) and thread into housing (T11).
Miscellaneous Hardware
1.
Install magnetic drain plug (T27).
2.
Install breather (T134).
3.
Install oil level plug (T73) and site plug (T134).
4.
Install breather (T27) if removed.
5.
Install sump oil strainer (T132).
6.
If reusing flinger grommet (T137) and flinger disc (T138), install on impel‐
ler shaft.
NOTE: Tapered end of grommet should face the pump.
7.
For cases built between 9/87 and 8/93, install V-style flinger (T138) with
flap towards the oil seal on the driven shaft. For cases built after 8/93 or
not re-using older flinger, install sealing boot.
Oil Pump
1.
Install gasket (T96) over pilot diameter on oil pump (T34).
2.
Position pump (T34) on adapter (T31).
3.
Line up drive tang of oil pump shaft with slot in driven shaft.
4.
Fit pilot diameter of oil pump (T34) into adapter (T31) making sure tang on
oil pump shaft and slot in driven shaft line up and engage. Fasten pump
(T34) to adapter (T31) with screws (T97) which pass through pump into
the adapter.
Oil Hoses
1.
Install nipple (T101), tee (T102), hose (T64 or T67) if previously removed
and adapter union (T66) between discharge side of pump and spray tube
assembly.
2.
Install street elbows (T57) at sump strainer (T132) and inlet of oil pump
(T34).
3.
Install adapter union (T66) in elbow (T57) at sump strainer (T132).
4.
Install hose (T67).
5.
Install plug (T98) (a pressure gauge may have been installed) in tee (T102
and case (T28).
Reassembly of Accessories to the Transmission
Electric Shift Assembly
1.
Make sure adjusting screws (T86) are in place and adjusted. Adjusting
screw retainer (T87) should be installed in slot end of each screw.
2.
Position and bolt electric shift assembly into place making sure gasket
(T56) is installed between shift assembly and face of the case (T74).
Fasten in place with cap screws (T52).
3.
Fasten pivot plate (T62) and cover (T75) to shift arm (T62) if these were
removed.
4.
Reconnect wiring and check for proper adjustment of indicator light switch
if shift unit is so equipped.
NOTE: If chassis is equipped with an automatic transmission, indi‐
cator lights must be used.
Refer to separate operation and maintenance instructions for adjust‐
ment of the shift switch. For details of electric shift assembly, refer
to separate service parts list.
Pneumatic Shift Assembly
1.
Make sure adjusting screws (T86) are in place and adjusted and adjusting
screw retainer (T87) installed in slot end of each screw.
2.
Position and bolt pneumatic shift assembly into place making sure gasket
(T56) is installed between shift assembly and face of the case (T74).
Fasten in place with cap screws (T52).
3.
Connect power supply and truck transmission interfaces.
4.
SAE J1402 air brake hose recommended, 1/4” to 3/8”. Connect air lines
from main truck supply.
Brake Assembly
1.
If previously removed, reinstall the drain tube (T85) in hole in bottom of
coupling shaft housing (T42).
2.
Install and fasten brake assembly to coupling shaft housing (T42). Install
related linkage and brake drum, and adjust brake. For detailed instructions
on brake installation and adjustment, refer to separate instructions.
Содержание Y Series
Страница 14: ......