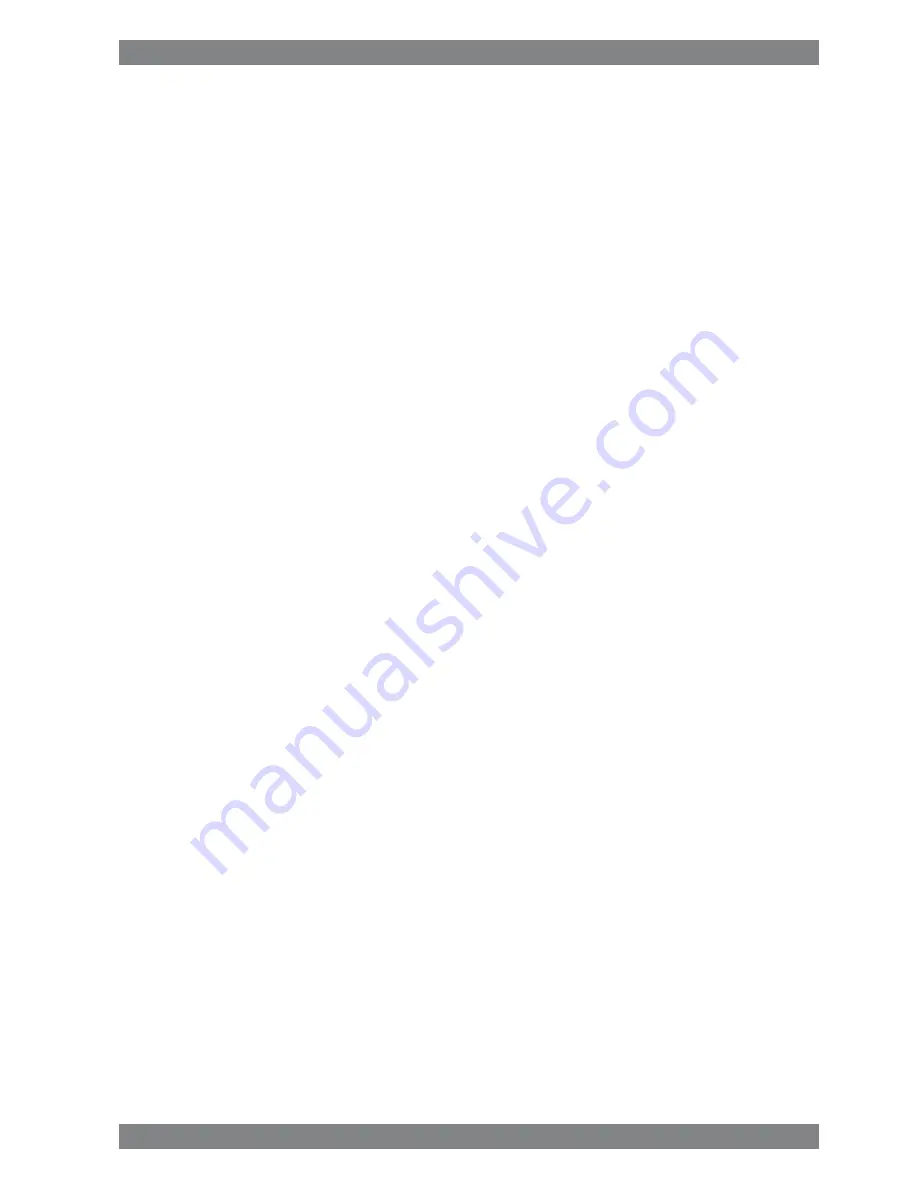
15.
Foundation
Engines can be either rigidly mounted on chocks, or resiliently mounted on rubber elements.
If resilient mounting is considered, Wärtsilä should be informed about existing excitations such
as propeller blade passing frequency. Dynamic forces caused by the engine are listed in the
chapter Vibration and noise.
15.1
Steel structure design
The system oil tank may not extend under the reduction gear, if the engine is of dry sump type
and the oil tank is located beneath the engine foundation. Neither should the tank extend
under the support bearing, in case there is a PTO arrangement in the free end. The oil tank
must also be symmetrically located in transverse direction under the engine.
The foundation and the double bottom should be as stiff as possible in all directions to absorb
the dynamic forces caused by the engine, reduction gear and thrust bearing. The foundation
should be dimensioned and designed so that harmful deformations are avoided.
The foundation of the driven equipment must be integrated with the engine foundation.
15.2
Mounting of main engines
15.2.1
Rigid mounting
When main engines are rigid mounted normally either adjustable steel chocks or resin chocks
are used. The chocking arrangement shall be sent to the classification society and Wärtsilä
for approval.
The bolt closest to the flywheel at either side of the engine shall be made as a Ø34H7/m6
fitted bolt. All other bolts are clearance bolts.
The clearance bolts shall be through bolts with lock nuts. Ø33 holes can be drilled into the
seating through the holes in the mounting brackets.
The design of the foundation bolts is shown in the foundation drawings. When these dimensions
are followed, standard bolts can be used for the clearance bolts in order to fulfill the
requirements of the classification societies. For the fitting bolts is recommended to use a high
strength steel, e.g. 42CrMo4 TQ+T or similar. A high strength material makes it possible to
use a higher bolt tension, which results in a larger bolt elongation (strain). A large bolt elongation
improves the safety against loosening of the nuts.
To ensure sufficient elongation distance sleeves according to the bolt drawings shall be used.
In order to avoid bending stresses in the foundation bolts the nuts underneath the top-plate
must be provided with spherical washers which can compensate for an inclined surface.
Alternatively the contact face of the nut/bolthead underneath the top plate should be counter
bored perpendicular to the orientation of the bolt.
When tightening the bolts with a torque wrench, the equivalent stress in the bolts is allowed
to be max. 90% of the material yield strength.
Side supports should be fitted to all engine feet where no fitting bolts are used. In addition
end supports should be fitted at the free end of the engines in case fitting bolts are omitted.
Side supports are to be welded to the top plate before aligning the engine and fitting the
chocks. If resin shocks are used an additional pair of lateral supports shall be fitted at the
flywheel end of the engine. The clearance hole in the chock and top plate should have a
diameter about 2 mm larger than the bolt diameter for all clearance bolts.
Wärtsilä 26 Product Guide - a9 - 7 September 2016
15-1
15. Foundation
Wärtsilä 26 Product Guide
Содержание WARTSILA 26
Страница 1: ...W RTSIL 26 PRODUCT GUIDE...
Страница 12: ...This page intentionally left blank...
Страница 34: ...This page intentionally left blank...
Страница 50: ...This page intentionally left blank...
Страница 92: ...This page intentionally left blank...
Страница 114: ...This page intentionally left blank...
Страница 148: ...This page intentionally left blank...
Страница 160: ...This page intentionally left blank...
Страница 172: ...This page intentionally left blank...
Страница 182: ...This page intentionally left blank...
Страница 188: ...This page intentionally left blank...
Страница 190: ...This page intentionally left blank...
Страница 193: ......
Страница 194: ......
Страница 195: ......