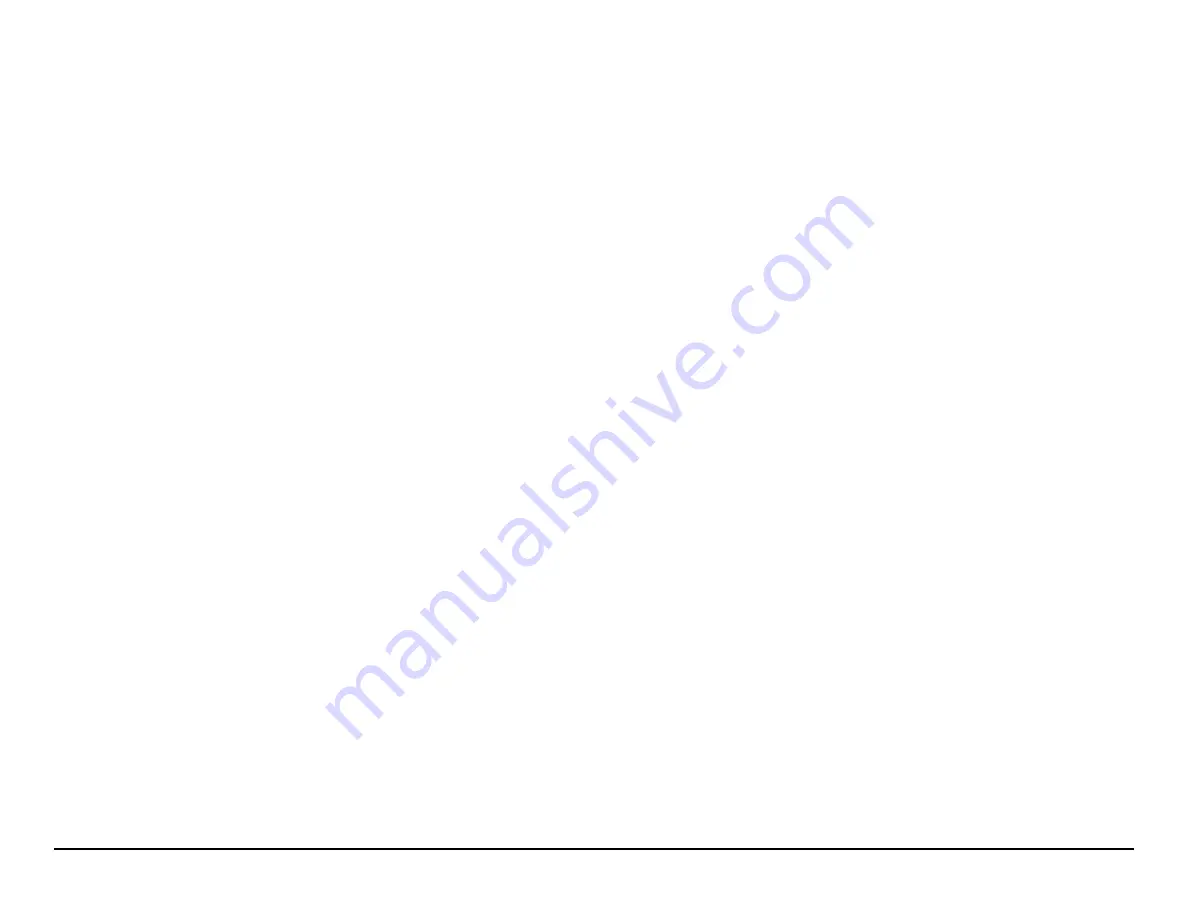
rhdf2dl1sm-rev0413
Model RHDF2 Page 7
PRINCIPLE OF PUMP OPERATION
This ball valve fitted pump has been equipped with IDEX’s patented AirVantage equipment. To fully understand the
operation of the AirVantage, one must first understand the basics of Air Operated Double Diaphragm (AODD) pumps.
AODD’s are powered by compressed air. The compressed air is directed behind each of the flexible diaphragms by a
Main Air Valve. Once the diaphragm has reached the end of its stroke, a Pilot Valve is mechanically actuated, sending
an air signal back to the Main Air Valve which redirects air to the opposite diaphragm. This causes the diaphragm
assemblies, which are connected by a common Diaphragm Rod, to move in a reciprocating action.
Air is directed to the inboard side of the diaphragm, which is closest to the center of the pump. This is referred to
as the air side of the diaphragm. The opposite side is commonly called the fluid side. Most AODD pumps have a 1:1
ratio design. This means, when the discharge of the pump is closed completely (dead headed), the maximum pressure
the pump will create will be equal to the air pressure being applied to the pump. At this point, and only at this point, the
diaphragm will be completely balanced. The air pressure is equivalent to the fluid pressure and there will be no movement
of the diaphragm. If the pump is stroking, then the system is not balanced. There will be more pressure applied to the air
side than fluid pressure on the fluid side.
During each stroke of the pump there are two distinct operations that occur. One diaphragm is moving away from
the center of the pump, moving fluid out of the Discharge Manifold, while the other diaphragm is moving toward the
center, bringing fluid into the Suction Manifold. Considering that the pump has a common suction and discharge port,
these two operations are separated from each other through a series of Check Valves.
PRINCIPLE OF AIRVANTAGE
AirVantage is a special air side device which uses equipment that can accurately monitor the operation of the pump.
Based on the monitored information, air is metered to the correct amount to perform the work required, and
NOTHING MORE.
Once the pump starts up, and the AirVantage is turned on, the LED indicator light will go through a series of patterns.
Initially the light will be solid green. This indicates the AirVantage is allowing the pump to reach a steady state. Next,
the light will pulse at a very rapid rate. This is called the learn phase. Learn is where the AirVantage monitors the pump
in non-AirVantage mode. This will set the parameters for operation in AirVantage mode. In less than one minute, the
pump will change tones. The LED indicator light will start an uneven blink when optimization has started. Optimization
will be completed once the LED light is blinking in unison with the stroke rate of the pump. All this is completed without
sacrificing a significant amount of flow.
INSTALLATION AND START-UP
The pump should be located near the product being pumped, in order to keep the suction line as short as possible.
Minimize the number of fittings between the product and the pump and maintain the line size, if possible. Better results
will always be realized if the line size of the suction line is increased by one size. It's not recommended to hook up
rigid pipe directly to the pump. Some method of expansion joint or vibration isolator should be used. A Warren Rupp
Tranquilizer
®
is recommended to reduce the pulsation in the flow. If the fluid level is more than 10 feet (3 meters) above
the level of the pump, a pressure regulating device may need to be added to the exhaust of the pump (Consult the factory
for recommendations).
AIR SUPPLY
The air supply pressure cannot exceed 125 psi (8.6 bar). The air line and associated components (filters,
regulators, solenoid valves, etc.) should not be less than ½” (13 mm). However, 3/4" (19mm) or greater is preferred. An
air line filter-regulator is necessary for the AirVantage installation. The required component (PN: 020.107.000) is available
through the distributor. Rigid pipe should not be hooked directly to the air inlet of the AirVantage. A flexible hose should be
installed to reduce the strain. Do not let the weight of the air line components be supported by the air inlet of the pump.
Failure to provide a means of supporting the weight may result in damage to the pump. If the pump will be shut down for
any extended length of time, it is recommended that the air supply to the pump should be shut off.
AIR LINE MOISTURE
Water in the compressed air supply can create problems such as icing and freezing of the exhaust air. The
formation of ice in the exhaust can cause the pump to cycle erratically, degrade efficiency, or even stop the pump. Fitting
the pump with the AirVantage technology reduces the exhaust temperature. This is due to more energy being extracted
from every pulse of air. When more energy is extracted, the temperature of the air is reduced. Some method of air drying
will be necessary. Most refrigerant dryers installed on compressors can reduce the dewpoint to about 40° F. This is
normally adequate for most pumping applications. If further drying needs to occur due to internal ice build-up, a desiccant
dryer can be installed. These air line dryers can lower the dewpoint to around -40° F.
AIR VALVE LUBRICATION
The air valve and pilot valve are designed to operate without lubrication. There may be instances of personal
preference or when extremely dry air is being used (instrument quality or nitrogen) that a small amount of lubrication will
improve the life of the rubber components being used on the air side of the pump. The lubrication may be added using an
air line lubricator (¾” PN: 020.051.001 – 1” PN: 020.052.001). At the point of operation use SAE 10 weight, non detergent
oil at a maximum rate of 1 drop per hour for every 20 scfm (9.4 liters/sec) of air consumption. Consult the pump curve to
determine this value. The smallest amount needed is preferred.
AIR INLET AND PRIMING
To start the pump, make sure the AirVantage switch is in the off position. Increase the pressure until the pump starts
to cycle. The pump stroke rate should slow slightly when the pump is primed. Once the pump is fully primed, increase
the pressure at the regulator until the desired flow rate is achieved. Again, the pump curve can be used to derive this
value. If increasing the pressure to the pump does not generate a higher flow rate, then cavitation has occurred. Back the
regulator off slightly. To gain the most efficiency from the pump, try to run the pump fully primed at all times.
BETWEEN USES
When the pump is being used to move materials that tend to settle out or solidify, the pump should be flushed to
prevent damage. The product that remains in the pump could dry and settle out. This could potentially cause damage
to the diaphragms and/or check valves during restart. In freezing temperatures the pump must be completely drained
between uses. Due to the addition of the new technology, it is recommended the air supply to the pump be shut off if the
pump is going to be shut down for an extended length of time.