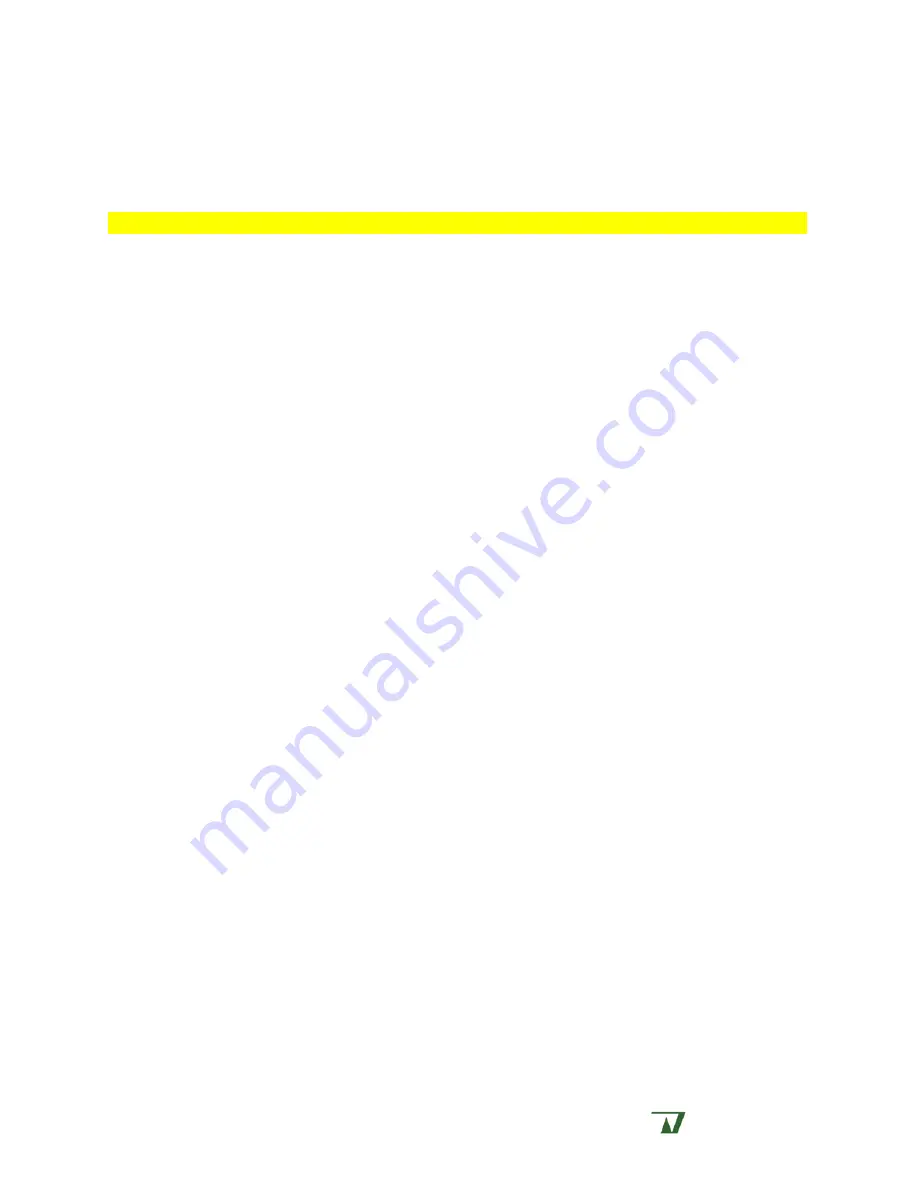
CL-200A Manual, Rev. 120523
11
OPERATION
The main use of a heater/cooler control device such as the
CL-200A
is to maintain a constant
bath temperature with minimum deviation from a set temperature. This is usually achieved by using
a thermally controlled chamber/platform or in-line solution heater, or a combination of both.
NOTE:
Refer to the front and rear panel schematics on pages 6-9 for orientation of the
CL-200A
controls.
AUTOMATIC MODE
In
Automatic Mode
, the
CL-200A
maintains the temperature of the connected heater/cooler at
the value set by the user.
Operation is straightforward. Connect your heater/cooler device and sensor thermistor as
described on page 10. Set the
CL-200A
to
internal commands
by setting the
INTERNAL
/
EXTERNAL
SELECT
control (Item J) to
internal
. Place the
CL-200A
into
auto mode
by switching the
COOLING
MODE SWITCH
(Item C) to
auto
. Switch the
METER
(Item B) to
Set Temp
and adjust to the desired set-
point using the
SET TEMPERATURE
control (Item H).
Alternatively, the
CL-200A
can be commanded using external inputs. Set the
CL-200A
to
external commands
by setting the
INTERNAL
/
EXTERNAL SELECT
control (Item J) to
external
. In this
mode the
CL-200A
will accept external temperature settings from the
EXT TEMP SET
BNC (Item U) on
the instrument rear panel. This input is calibrated to 100 mV/°C.
The selectable
LOOP SPEED
control (Item G) is used to adjust the speed of the feedback loop in
the heater/cooler-thermistor system, which controls the rate of change of the
CL-200A
output
voltage. Non-Warner heater systems with feedback thermistors can be used in
automatic mode
provided they are compatible with the
CL-200A
requirements.
LOOP SPEED
is normally set to
fast
to provide the shortest cycle time between the application of
power to the heater element and the sensing of temperature at the thermistor. For heater/cooler-
thermistor systems with long response times, such as with Warner’s
SC-20
in-line solution
heater/cooler, the
fast
setting will cause the temperature to overshoot the target resulting in system
oscillation. For this condition, try
medium
or
slow
settings to find a more optimal feedback rate.
Feedback Thermistor Selection
A
FEEDBACK THERMISTOR
switch allows the user to select which thermistor is used for the
control loop. Choosing
T1
(control thermistor) sets the peripheral device’s internal thermistor to
control the feedback loop. Selecting
T2
(monitor thermistor) allows feedback control at the location of
the monitor thermistor, as selected by the user.
The standard
CONTROL THERMISTOR
is the sensor located in the heating/cooling device. This
sensor is placed at the optimal point to control the temperature of the heating/cooling device. The
MONITOR THERMISTOR
is the peripheral thermistor that can be used to monitor the temperature at
another location in the experimental configuration. This thermistor monitors the temperature at the
selected point in the experiment and is more accurate but is less stable in the control loop because of
the delay between heating (or cooling) and sensing.
To protect the experiment if the monitor thermistor is removed, the limit of the increase in
temperature between the control and monitor thermistors in the feedback loop is 8
˚
C. This lowers
Warner
Instruments
A Harvard Apparatus Company