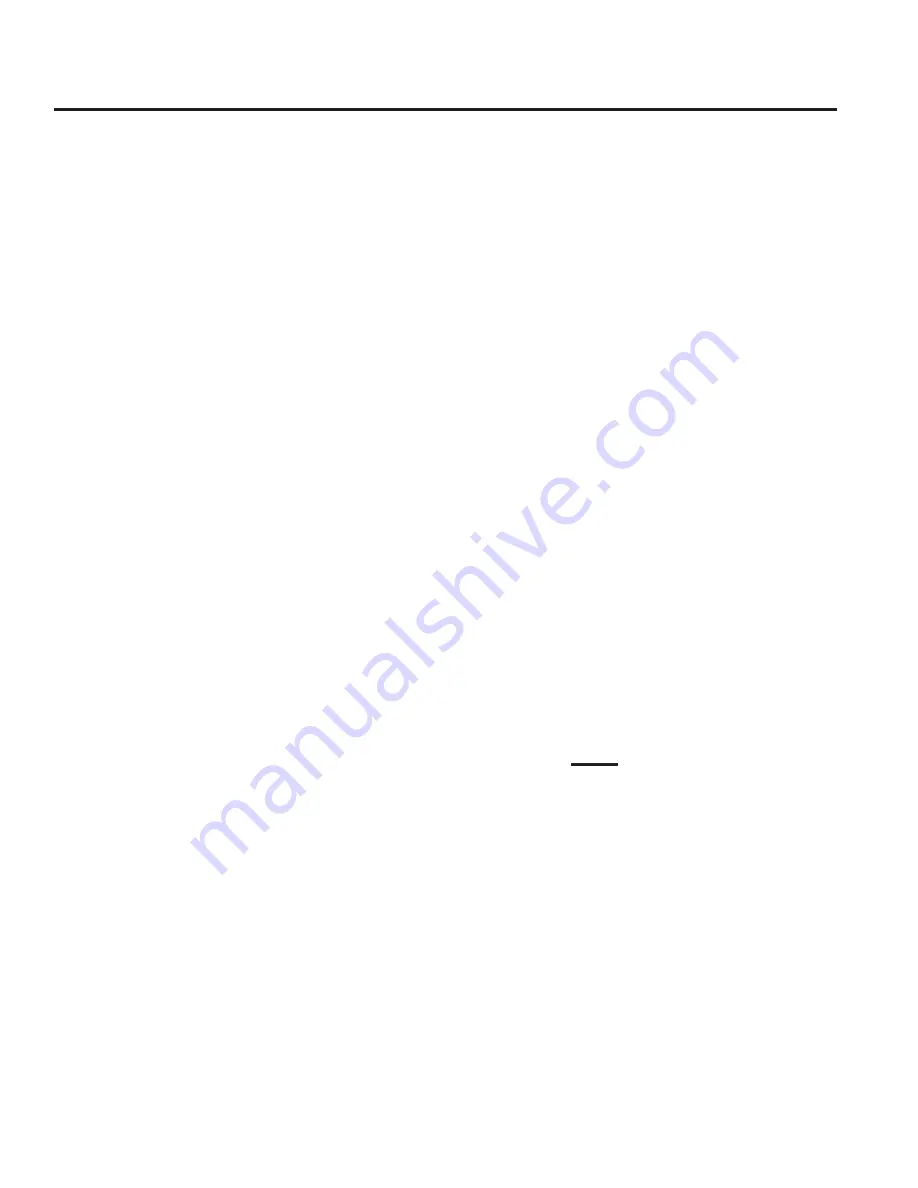
12
D15-991-2400 Rev B
D/G15 & D/G17 Service (Fluid End)
f. Reinstall the valve assemblies:
• Clean the valve ports and shoulders in the valve plate
(26) with a Scotch-Brite pad or fine emery cloth. Wash
the valve plate after cleaning, and lubricate the valve
ports with a compatible grease, oil, or petroleum jelly.
• Install new O-rings (9, 15) on seats (10, 16) and
lubricate all O-rings.
• Inlet Valves (five center, larger valves). Insert the
spring retainer (14) into the valve plate (26), followed by
the Tetra seal (13) if spring retainer is plastic. Insert the
spring (12) into the retainer, followed by the valve (11)
onto the spring. Finally, insert seat (10) with new O-ring
into the valve bore with the larger I.D. chamfer (seating
surface) facing down, towards the valve.
• Outlet Valves (five outer, smaller valves). Insert the
outlet seat (16) with new O-ring into the valve bore with the
larger I.D. chamfer (seating surface) facing up. Insert a
Tetra Seal (17) if valve spring retainers are plastic. Insert
the valve (18) and spring (19) onto the seat. Finally, insert
the spring retainer (20) into the valve bore.
• Make sure the springs are all properly nested into the
spring retainers to ensure proper valve performance.
3. Inspect and Replace
Diaphragms (22)
a. Lift a diaphragm by one edge, and turn the pump shaft
until the diaphragm moves up to “top dead center”. This
will expose machined cross-holes in the spool valve (55)
behind the diaphragm.
b. Insert a 3/32 x 6 in. hex wrench through one of the
machined cross-holes, to hold the diaphragm up and to
keep the valve plunger from rotating. The proper size tool
is included in the Wanner Tool Kit. (Don’t remove the tool
until the new diaphragm is installed in step “f” below.)
c. Unscrew the diaphragm. Use a T30 Torx bit, and turn
counterclockwise.
d. Inspect the diaphragm carefully. A damaged diaphragm
generally indicates a pumping system problem and
replacing only the diaphragm will not solve the larger
problem. Inspect the diaphragm for the following:
•
Half-moon marks
. Usually caused by cavitation of
pump (See Troubleshooting section).
•
Concentric circular marks.
Usually caused by
cavitation of pump (See Troubleshooting section).
•
Small puncture
. Usually caused by sharp foreign
object in fluid, or by ice particle.
•
Diaphragm pulled away
from center screw or from
cylinder sides. Usually caused by fluid being frozen
in pump, or by overpressurization of pump.
•
Diaphragm stiff and inflexible
. Usually caused
by pumping fluid incompatible with diaphragm
material, or diaphragm operated at temperatures
below rated capability.
•
Diaphragm edge chewed away
. Usually caused by
overpressurizing system.
CAUTION: If a diaphragm has ruptured and foreign
material or water has entered the oil reservoir, do
not operate the pump. Check all diaphragms, then
flush the reservoir completely (as outlined below)
and refill it with fresh oil. Never let the pump stand
with foreign material or water in the reservoir, or with
the reservoir empty.
e. Clean away any spilled oil.
f. Install a new diaphragm and tighten to 18 in.-lbs (203
N-cm).
g. Repeat the above inspection procedure (and replacement,
if necessary) with the other four diaphragms.
4. Flush Contaminant from
Hydraulic End
(only if a diaphragm has ruptured)
a. With the valve plate and manifold still removed (see
above), remove the oil drain cap (28) allow all oil and
contaminant to drain out.
b. Fill the reservoir with compatible solvent, manually turn
the pump shaft to circulate the kerosene, and drain.
Dispose of this contaminated fluid properly.
c. Repeat the flushing procedure (step “b” above).
d. Fill the reservoir with fresh oil, manually turn the pump
shaft to circulate the oil, and drain again.
e. Refill the reservoir. If the oil appears milky, there is
still contaminant in the reservoir. Repeat the flushing
procedure until the oil appears clean.
5. Prime the Hydraulic Cells
Method #1 (system head
pressure
less
than 2 psi)
a. With the pump
horizontal and the fluid end head
removed
, fill the reservoir with the appropriate Hydra oil
for the application. Have a catch basin for oil that leaks
from behind the diaphragms when priming. Catch the
oil and dispose of it properly;
do not reuse it
.
b. All air in the oil within the hydraulic cell (behind the
diaphragm) must be forced out by turning the shaft (and
thus pumping the piston). A Shaft Rotator is included
in the Wanner D-15 Tool Kit. Rotate the shaft two
revolutions and refill the reservoir. Rotate it two more
revolutions and refill again. Continue to do this until the oil
that is being pumped from the back of all five diaphragms
is free of air.
c. Wipe excess oil from the cylinder housing (25) and
diaphragms (22).
d. Ensure that the oil level is 1/4 in (6 mm) above the cast
surface in the upper oil reservoir.
e. Replace oil fill cap (30).