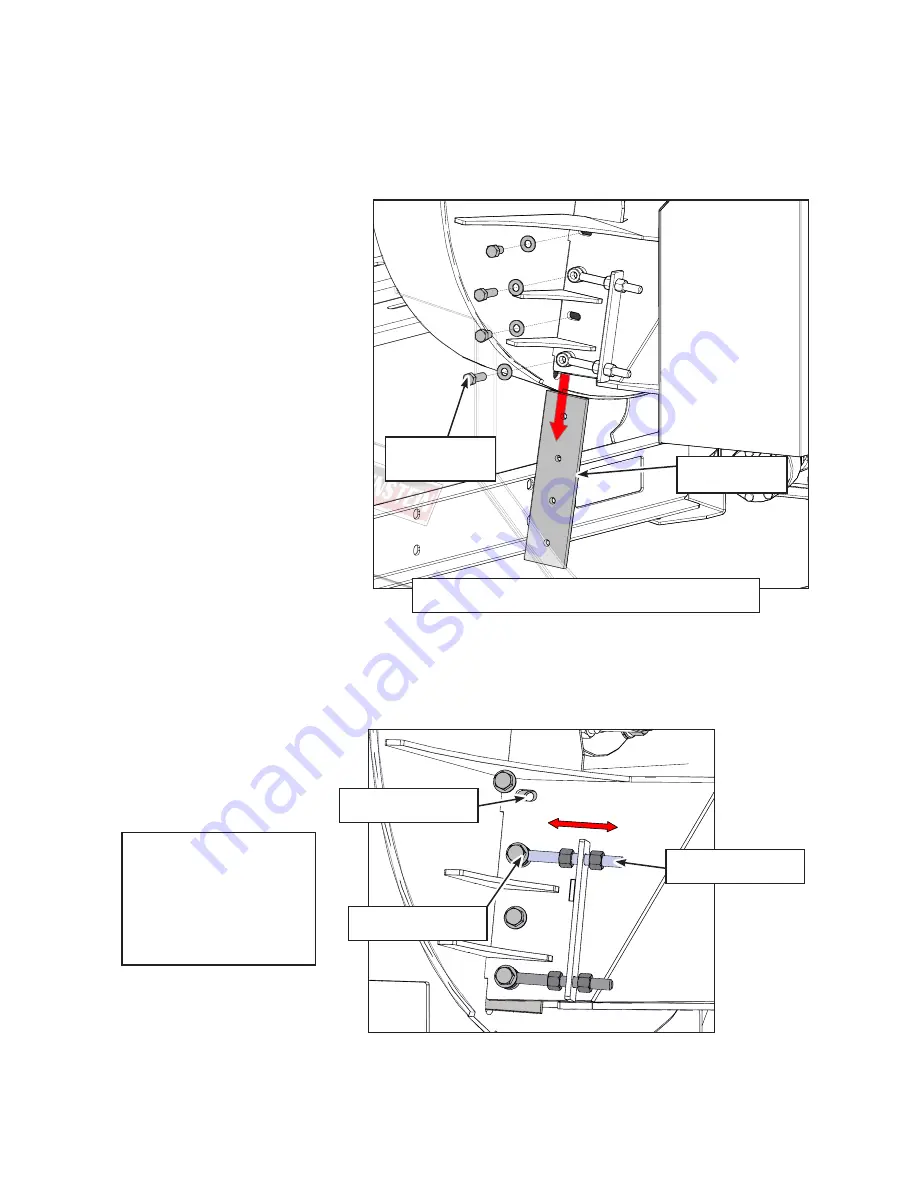
42
7�2�6 LEDGER BLADES:
Each machine is equipped with a ledger (stationary) blade that acts as a shear for the moving rotor
blades.
The ledger blade is located on the lower rotor housing, mounted on slotted holes for adjustment. There
are 4 usable corners on the blade, when the corner facing the rotor blade rounds over, remove the blade
and re-install with a different corner facing the rotor blade. It is recommended that the clearance between
the rotor and stationary blades be
set and maintained at 1/32 to 1/16"
(.76 - 1.52 mm) to obtain the best
performance.
1.
Ensure the machine is set in
Safe
Condition
(See Section 7.2).
2.
Remove the 4 bolts that hold the
ledger blade to the ledger mount.
3.
Carefully remove the blade, pull it
down and slightly to the side to clear
the axle.
4.
Rotate the blade and replace or
replace with new or re-sharpened
blade.
5.
Hand tighten the bolts.
6.
Set the clearance between the
ledger and rotor blades using the
ledger adjuster: loosen the nuts on
the adjuster and move the ledger to
the correct clearance.
7.
Clearance settings should be set at
1/32 - 1/16" (.76 - 1.52 mm).
For fast and easy setting, use the chipper clearance setting gauge, included with your BX CHIPPER
8.
Ensure you move both adjusters evenly.
9.
Tighten adjuster nuts, then tighten ledger blade bolts. Tighten as specified in the torque chart.
Ledger Blade
Ledger Blade
Bolts
Cut-away view showing Ledger Blade Assembly
Ledger Adjuster
Slotted Mounting
Holes
Loosen Nuts
Ledger Blade:
depending on
your model the ledger blade
may have 3 mounting holes.
The removal / replacement /
adjustment procedure is the
same for both.