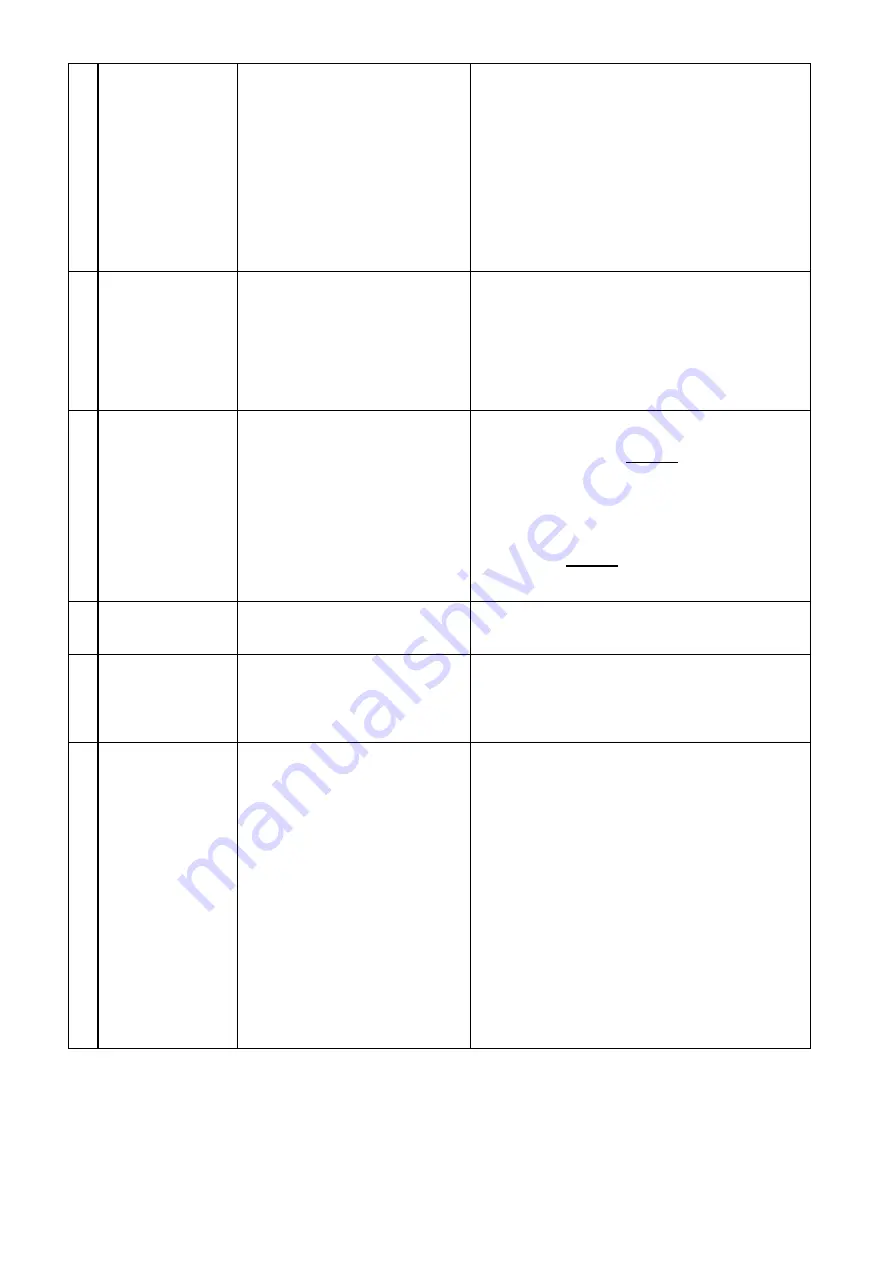
27-05-19 UNI-SAN Domestic Instructions Page 12
4. Motor does not
start at all.
-Not connected to power supply.
-Power cut/fuse blown.
-Thermal load activated.
-Faulty float level switch.
-Connect power as detailed Section 8.3.
-Restore electrical supply.
-Determine and remove the cause of the
overload trip. Leave the unit to cool down, check
for fault 5 and retry. If the overload re-occurs,
switch the power off and contact a Wallace
Service Agent.
-Check the float level switch setting and
operation. Refer fault 9 below.
5. Motor hums /
buzzes but does
not appear to run.
-Foreign body blocking the
impeller.
-Electrical fault.
-Float level switch is faulty.
-Remove obstruction from the pump. Check
freedom of operation as per fault 1 above.
-If there is no obstruction and the rotor turns
freely, then the motor is possibly faulty. Refer to
a service agent.
-Check the float level switch.
6. After
evacuation
the motor
engages several
times before
stopping, or
restarts at
intervals without
any liquid
discharged into
the collection
tank.
-Water is leaking / back flowing
into the unit from the delivery
pipe, triggering the motor to re-
start.
-Non-return valve does not
close properly.
-No non-return valve in the
delivery line.
-Check that the swing check valve is clear. This
should be the 25 mm SWING CHECK VALVE
supplied installed in a
vertical
section of pipe as
close as possible (within 1 metre) of the pump.
-Remove the obstruction.
-Fit 25 mm SWING CHECK VALVE supplied
installed in a
vertical
section of pipe as close as
possible (within 1 metre) of the pump.
7. Pump runs and
makes a rattling
noise.
Solid object is in the tank or in
the pump and will not pass
through the delivery.
Clear the obstruction.
8. Unit smells.
-Inadequate water leading to
clogged up/dirty unit.
-No water seal on waste pipes
to the unit.
-Flush unit out with a bleach solution and clean
water. Increase the proportion of water to solids
that flows into the unit.
-Plumb in waste water traps.
9. Pump does not
start or stop at the
correct levels of
liquid in the tank.
(This should be
ON at 200 mm
from the bottom
and OFF at 60
mm from the
bottom of the
tank).
ON level is the
same for both
domestic and
COMMERCIAL
models ).
-Tank not correctly vented.
-Float level switch jammed.
-Float and cable set at an
incorrect length.
-Faulty float level switch.
-Float level switch cable
stiff and inflexible.
-Unscrew tank inspection lid to allow venting.
Switch power on and operate pump. If operation
is correct, switch off power and check tank vent
is clear or fit vent according to Sections 8.2.6.
Replace inspection lid.
-Remove obstruction and recheck freedom of
operation.
-Ensure that 50 mm of float cable is exposed
inside the tank and the float switch can move
freely up and down.
Rotate the cable such that the float surface
bearing the word "SMALL" (in capitals) is on the
underside AND such that the float's flat surface
rests at a 45
angle to the water level.
-Replace the float level switch.
-Replace the float level switch.