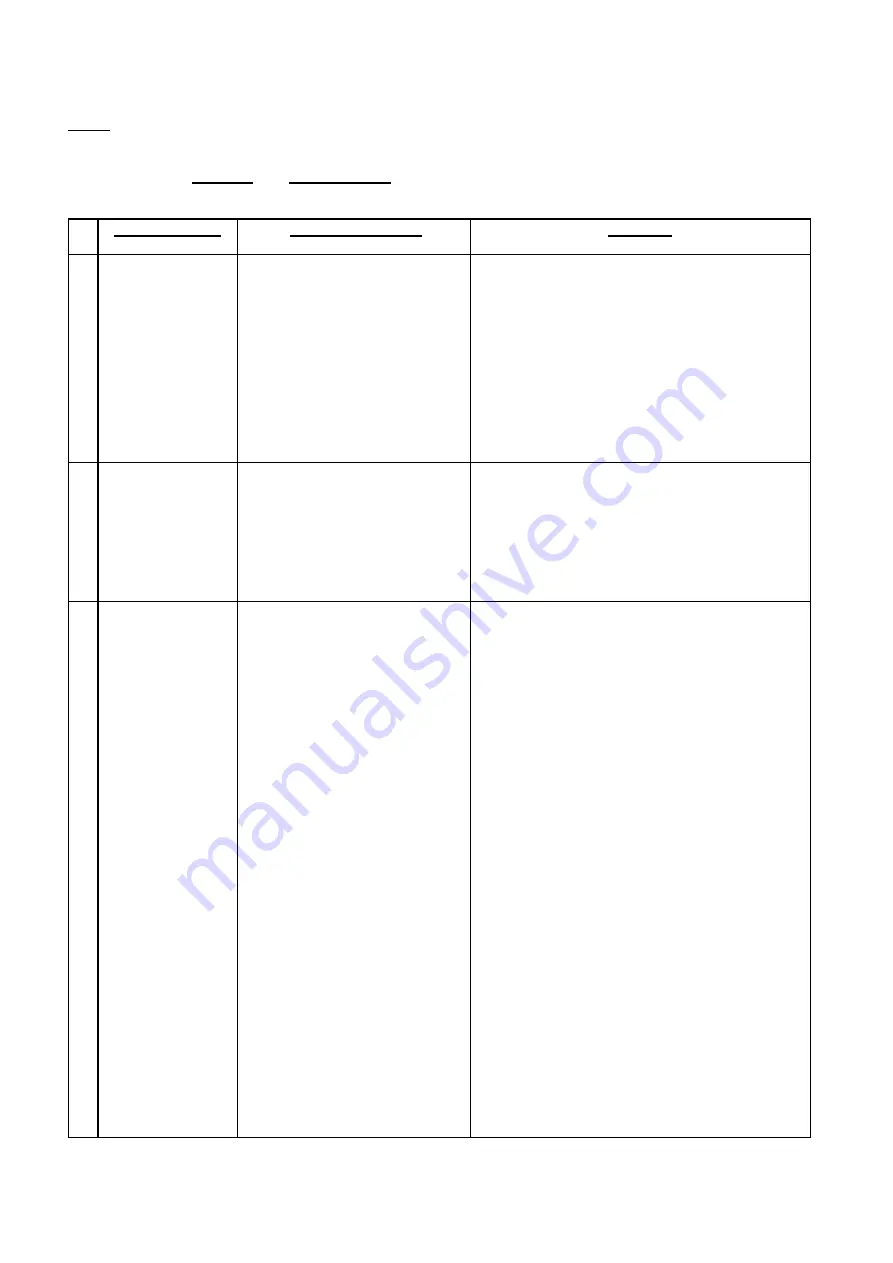
27-05-19 UNI-SAN Domestic Instructions Page 11
DO NOT DISCHARGE LIQUID INTO THE PUMP IF IT IS NOT OPERATING.
NOTE In the warranty period, any work not described in this manual must be carried out by Wallace Pumps Service
Agents otherwise your warranty and the product's durability period will be invalidated.
ALWAYS ensure isolation and disconnection of the power supply
to the pump before and whilst carrying out
any servicing work on the unit. Also ensure no liquid will flow into it during servicing.
OCCURRENCE
POSSIBLE CAUSE
REMEDY
1. -Motor
runs
continuously
without clearing
the liquid.
- Switch operated by water level
remains in the ON position
because :
a. pipework is blocked; or
b. pump is blocked; or
c. tank is blocked; or
d. check valve installed back to
front
e. delivery hose is kinked.
-Check that the pipework is clear.
-Turn off the power and check that the pump can
rotate freely in both directions by turning the
shaft at the top end of the motor with a
screwdriver.
-If blocked, clear the obstruction.
- Reverse the valve.
-PVC Pipes are recommended.
2.
-Pump runs but
delivers little or no
liquid.
-Delivery head (combination of
vertical and horizontal pipe
lengths, pipe bends and size) is
too high for the unit.
-Check the system against the pump operating
parameters. Refer Section 5 (Building design). If
the building or application design is in excess of
the pump capability shown on the chart, call our
office for advice.
-Check that the pump is not pumping the water
level down too low. ( Refer fault 9 below ).
3.
- Pump starts but
takes over 10
seconds to reduce
the liquid level in
the tank
( as seen through
the inspection lid).
-Delivery line is partially blocked
or too small.
-Wrong type of delivery valve
used ; eg spring poppet type
-Float level switch is too long.
-Float level switch is hung up.
-Float or pressure switch is
faulty.
-Pump is not venting.
-Tank is not venting
-Unblock and/or change the pipework to the
minimum ID. Refer Section 5( Hydraulic
capability ).
-Always use a 25 swing check valve in a vertical
position within 1 metre of pump.
-Check that the pump is not pumping the water
level down too low. (Refer fault 9 below).
-Remove the obstruction via the inspection lid.
-Replace the switch.
-Visually check that the tank vent pipe is clear ;
or by releasing the pipe from the tank and blow
down it; or by removing it and flush clean.
-Check that the vent functions:
. Liquid should rise in the vent tube until the
pump starts;
.When the pump runs, little or no liquid should
flow through the vent tube. Remove the
inspection lid to check the return flow into the
tank;
.When the pump stops, the liquid in the vent
tube should draw down to empty.
-Check that the pump is not pumping the water
level down too low. (Refer fault 9 below).