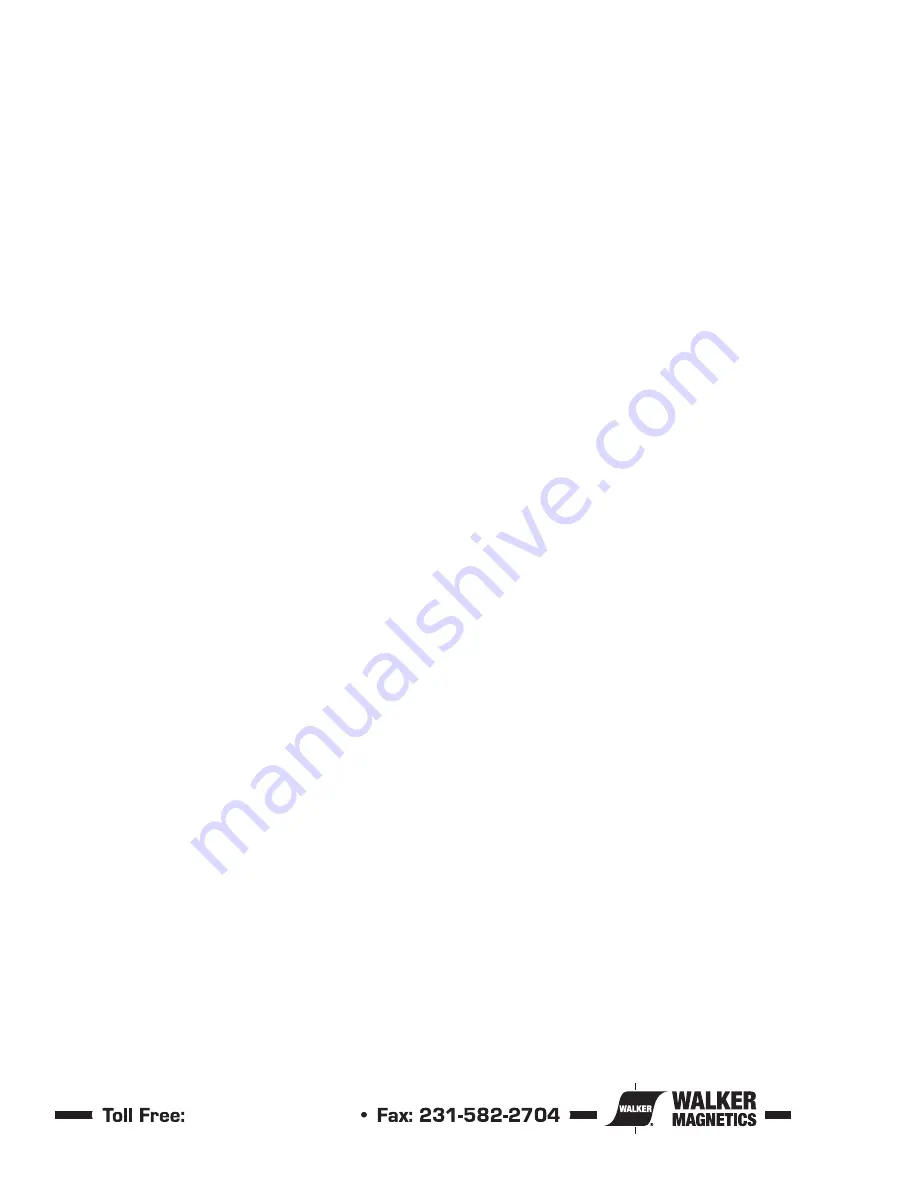
800-WMAGNET
10 of 33
2. When any control (power section) is to be placed in a secondary enclosure while still in its original enclosure, the following
specifications must be met:
a. With the control (power section) mounted in its original enclosure and then mounted in a secondary
enclosure, the air surrounding the original enclosure should not exceed 104° Fahrenheit.
b. The air temperature must be measured:
1) With the control in the Full holding position;
2) After the control has been in operation for 30 minutes; and
3) With the chuck holding the largest load to be used.
4 OPERATING INSTRUCTIONS
The O. S. Walker Microprocessor Chuck Control, model SMART-D, uses a remote unit that can select the following functions:
Full Holding; Variable Holding; Residual Holding; and Release. This control comes equipped with an adjustment for the
number of pulses per Release cycle. It also has additional options, which are a Part Released feature, a Current Sense
feature, and a Lockout feature.
4.1 Important Facts about Magnetic Holding
Workpiece characteristics must be considered in order to determine the magnetic holding attraction that a magnetic chuck
can provide.
This is true for all magnetic chucks because they all operate using the same fundamental laws of physics. Magnetic power is
often pictured as lines of magnetic force flowing from north to south pole. Anything that limits the flow of these magnetic lines
of force obviously reduces the magnets holding capacity. There are many important factors that limit the flow of these lines of
force.
4.1.1 Surface Conditions
Magnetic lines of force do not flow easily through air. They need iron in order to flow freely; therefore, anything that
creates a space or an air gap between the magnet and the workpiece limits the flow of magnetic lines of force and, thus,
reduces the holding capacity of a magnetic chuck.
•
Magnetic Chuck Surface Condition
-- The holding surface of a magnetic chuck must be clean, smooth, flat, and
free of nicks or burrs in order to minimize the air gap between the chuck holding surface and the Workpiece. All Walker
chucks are designed with soft, low carbon steel magnetic poles in the top plate in order to maximize the holding capacity;
therefore, special care must be taken to protect these areas.
•
Workpiece Surface Condition
-- The holding capacity of the chuck will be reduced if certain surface conditions exist. A
rough surface finish on the workpiece creates an air gap as also foreign materials like dirt, paint, rust, paper, and rags.
4.1.2 Workpiece Thickness
The greater the number of lines of magnetic force flowing from a magnet into the workpiece the greater the effectiveness
of the magnetic chuck. The thicker the workpiece, the more lines of magnetic force are able to flow. After a certain
thickness of the workpiece, no additional lines of force will flow because the magnet has reached its full capacity.
• Thin workpieces mean less iron available, and thus fewer lines of magnetic force flow from the magnet into the
workpiece. Therefore, the chuck holding capacity is reduced.
• Typically, the minimum thickness of a workpiece required to reach full holding capacity is the same as the thickness
of the chuck major magnetic steel poles.
4.1.3 Portion of the Chuck Surface In Contact With the Workpiece
The full surface of the chuck top plate must be covered by the workpiece to achieve the maximum holding capacity.
The surface of the workpiece must contact equal areas of the chuck opposite polarity major magnetic poles to obtain
maximum holding force.
Содержание IMI 100D
Страница 18: ...800 WMAGNET 18 of 33 5 6 Smart 75 100D Panel Layout Figure 5 1 Smart 75 100D Panel...
Страница 19: ...800 WMAGNET 19 of 33 5 7 Smart 20 30 50D Panel Layout Figure 5 2 Smart 20 30 50D Panel...
Страница 20: ...800 WMAGNET 20 of 33 5 8 Smart 7 10 15D Panel Layout Figure 5 3 Smart 7 10 15D Panel...
Страница 21: ...800 WMAGNET 21 of 33 5 9 Smart 3 5D Panel Layout Figure 5 4 Smart 3 5D Panel...
Страница 22: ...800 WMAGNET 22 of 33 5 10 Main PC Board Figure 5 5 Main PC Board...
Страница 30: ...800 WMAGNET 30 of 33 5 3 Remote Enclosure Dimensions Figure 5 12 Remote Enclosure BB 8783...
Страница 31: ...800 WMAGNET 31 of 33 5 4 Remote Wiring Connections Figure 5 13 Remote Wiring Connections...
Страница 34: ...1 800 W MAGNET WWW WALKERMAGNET COM 900632 A 07 21...