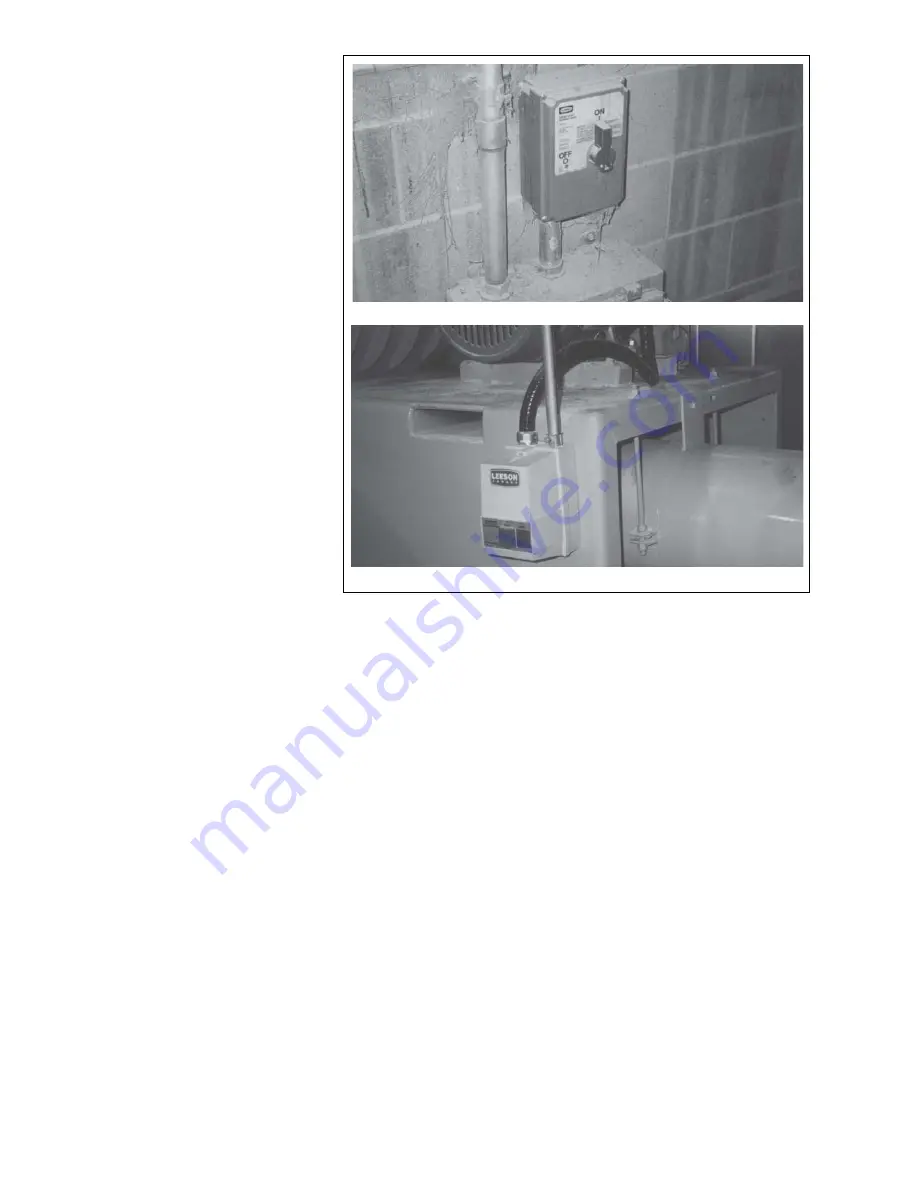
Fig. 4- 5 SWITCHES (TYPICAL)
Master
On/Off
4.
Starting Machine:
a.
Check that the master
panel is not locked out.
If it is, identify cause and
retrieve the tag. Turn
master panel on.
b.
Turn machine on at the
On/Off switch.
5.
Stopping Machine:
Turn the machine off using
the On/Off switch. This will
shut down both the blower
and the airlock.
23
Содержание Central Vac
Страница 1: ......
Страница 2: ......
Страница 22: ...b Attach wand or tube to the end of hose Hose Wands Fig 4 4 GATHERING COMPONENTS...
Страница 32: ...4 Check the oil level in the blower reservoirs 2 locations Schematic Rear Front Fig 5 3 RESERVOIRS...
Страница 50: ...7 SPECIFICATIONS 7 1 MECHANICAL SPECIFICATIONS SUBJECT TO CHANGE WITHOUT NOTICE...
Страница 53: ...PARTS ACCESSORIES...
Страница 65: ......
Страница 66: ......