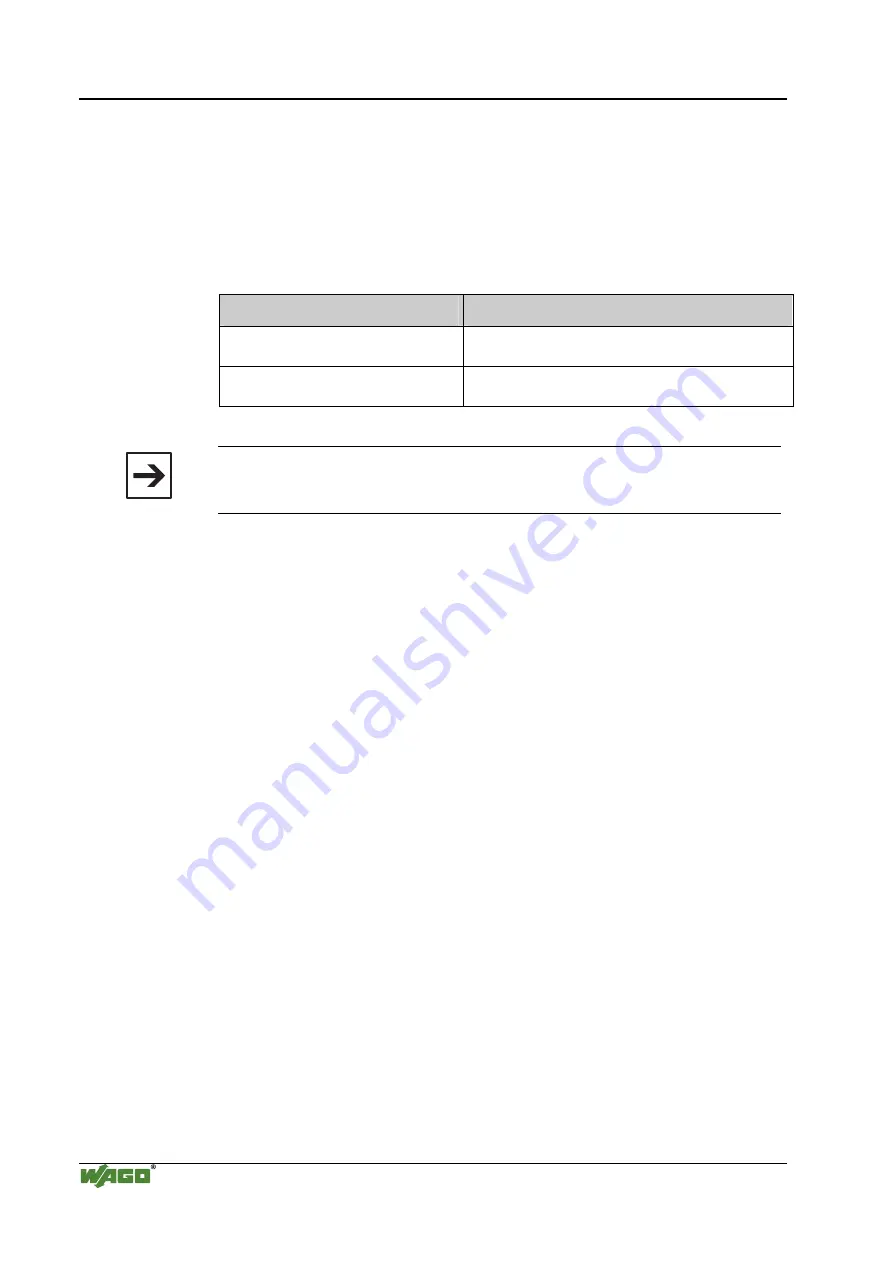
46 • Fieldbus Coupler 750-337, 750-338
Description
WAGO-I/O-SYSTEM
750
CANopen
3 Fieldbus Coupler
3.1 Fieldbus Coupler 750-337, 750-338
3.1.1 Description
The fieldbus coupler for CANopen differ in the fieldbus connection.
Item
Fieldbus Connection
750-337
MCS (Multi connector system)
750-338
D-SUB connection (9-pole)
Note
In this manual, the diagrams and pictures are shown from the coupler
750-337. The descriptions also apply equally to the coupler 750-338.
The fieldbus coupler 750-307 displays the peripheral data of all I/O modules
in the WAGO-I/O-SYSTEM 750 on CANopen. The data is transmitted with
PDOs and SDOs.
In the initialization phase, the bus coupler determines the physical structure of
the node and creates a process image from this with all inputs and outputs.
This could involve a mixed arrangement of analog (word by word data ex-
change) and digital (byte by byte data exchange) modules.
The local process image is subdivided into an input and output data area. The
process data can be read in via the CANopen bus and further processed in a
control system. The process output data is sent via the CANopen bus. The data
of the analog modules are mapped into the PDOs according to the order of
their position downstream of the bus coupler. The bits of the digital modules
are compiled to form bytes and also mapped into PDOs. Should the number of
digital I/Os exceed 8 bits, the coupler automatically starts another byte.
The entries in the object directory can be mapped to the 32 RxPDOs and 32
TxPDOs as required. The entire input and output data area can be transmitted
with the SDOs.
“Spacer modules” can be set using the software.