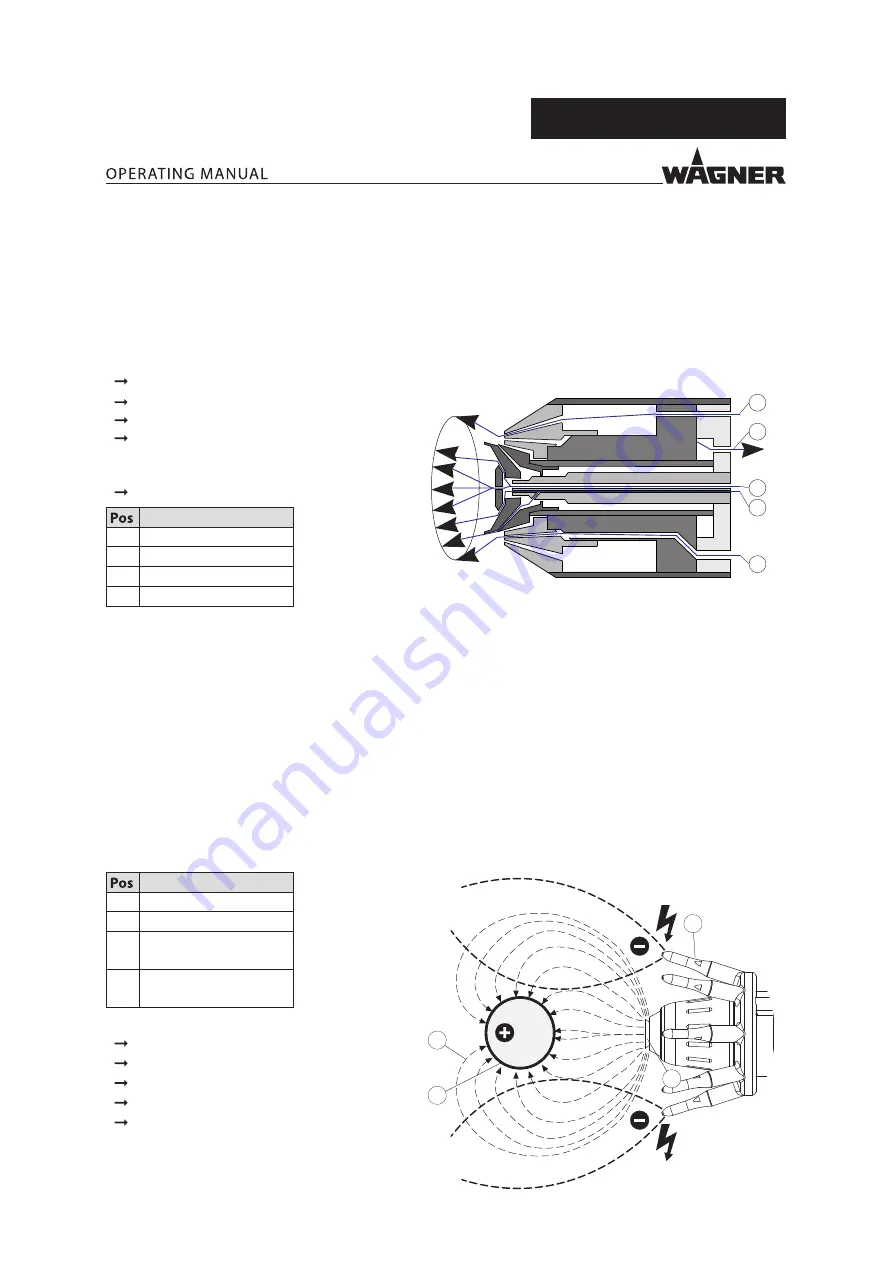
23
VERSION 01/2021
ORDER NUMBER DOC2422004
TOPFINISH Bell 1S ECH
5.2.2 ATOMIZATION PROCESS
5.2.2.1 SPRAYING PROCESS
During high-speed rotary atomization, the sprayed product is atomized radially at the
circumference of the rotating bell under low-pressure of approx. 0.03 to 0.40 MPa; 0.3 to
4.0 bar; 4.35-58.02 psi.
The steering air can be used to vary the atomizing cone diameter.
The spray pattern can be influenced by the following points:
Product pressure/flow rate
Rotation
Bell diameter
Pressure of steering air
approx. 0.03–0.40 MPa; 0.3–4.0 bar; 4.35–
58.02 psi
Applied high voltage
Designation
1 Steering air SA1/SA2
2 Turbine exhaust air
3 Spray product
4 Flushing agent
B_06634
1
3
4
1
2
Spray product (3) is fed through the central drill hole of the product tube.
The spray pattern is formed with the steering airs (1):
Steering air SA1: outer air for shaping.
Steering air SA2: inner air to advance the product.
Flushing agent (4) is fed in the outer annular gap of the product tube and is applied
through the central hole of the distributor.
The turbine exhaust air (2) is removed to the rear.
5.2.2.2 THE ELECTROSTATIC EFFECT
The fingers of the electrode ring generate an electrostatic force field via the applied high
voltage, through which the paint particles are charged.
The paint particles atomized by the rotating bell are now transported by kinetic and
electrostatic energy through the exterior charge via the electrode ring (electrode fingers)
to the grounded work piece and are distributed finely across the entire sprayed object.
Designation
1 Paint particle
2 Rotating bell
3 Electrode ring with
electrode fingers
4 Object to be sprayed is
grounded
Advantages:
High application effectiveness
Even coating thickness
Coating hidden locations
Improved edge covering
Low over spray
B_07446
4
1
2
3