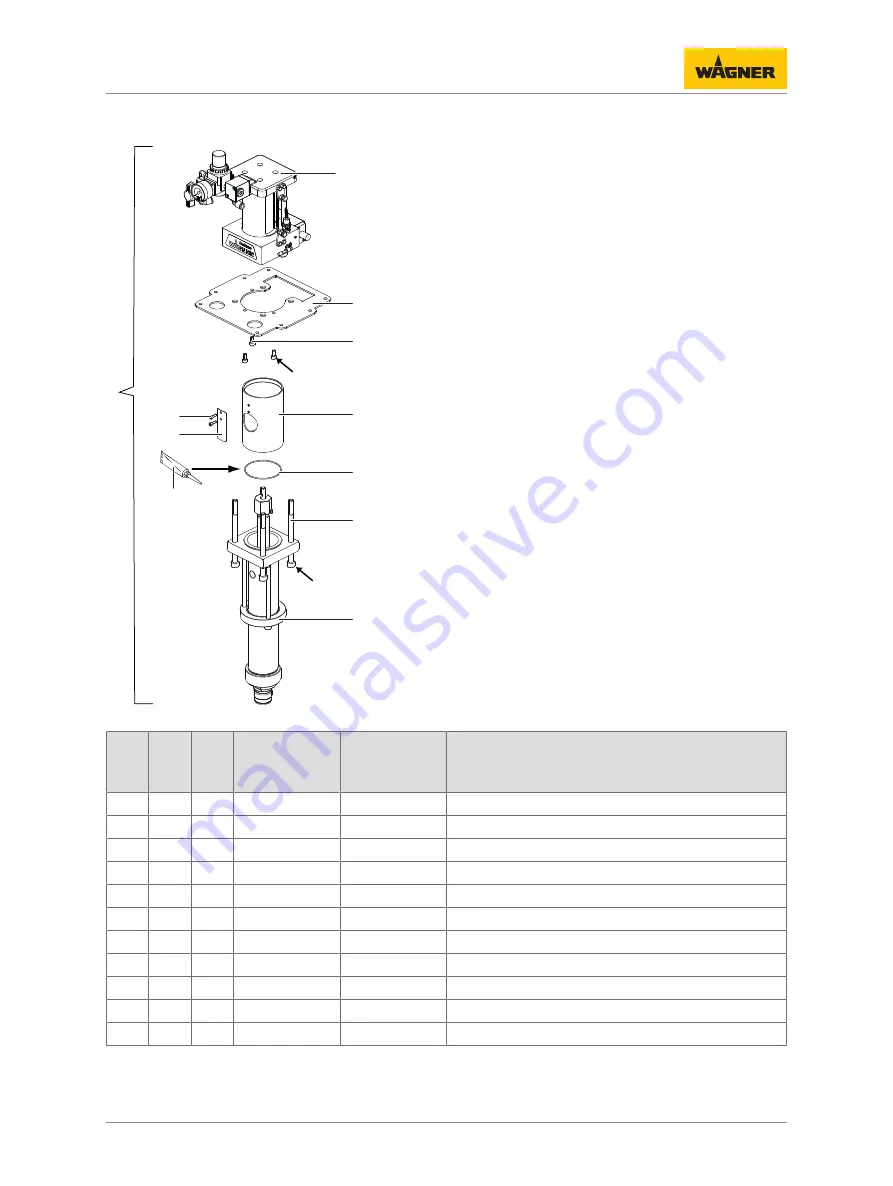
Operating manual Piston Pump EvoMotion 5-60
14 Spare Parts
54
Order number 2333563 | Edition 10/2020
14.3 OVERVIEW OF THE COMPONENTS
B_04148
4
8
1
5
6
7
9
3
10
15 Nm; 11.1 lbft
5 Nm; 3.7 lbft
11
2
Pos
K
Stk
Without sen-
sor
Order no.
With sensor
Order no.
Designation
1
1
2329535
2330596
EvoMotion 5-60 PE/T
2
1
U3B05012075
U3B05012075S Air motor M50 EM
3
1
2329681
Fluid section 60 PE/T EM
4
1
2332394
Pump support plate
5
1
A359.71B
M/P spacer tube
6
1
E516.71A
Safety fixture spacer
7
2
9900353
Hexagon socket head cap screw
8
3
9900346
Hexagon socket head cap screw
9
1
L236.06A
O-ring
10
4
9900385
Hexagon socket head cap screw
11
1
9998808
Mobilux® EP 2 grease