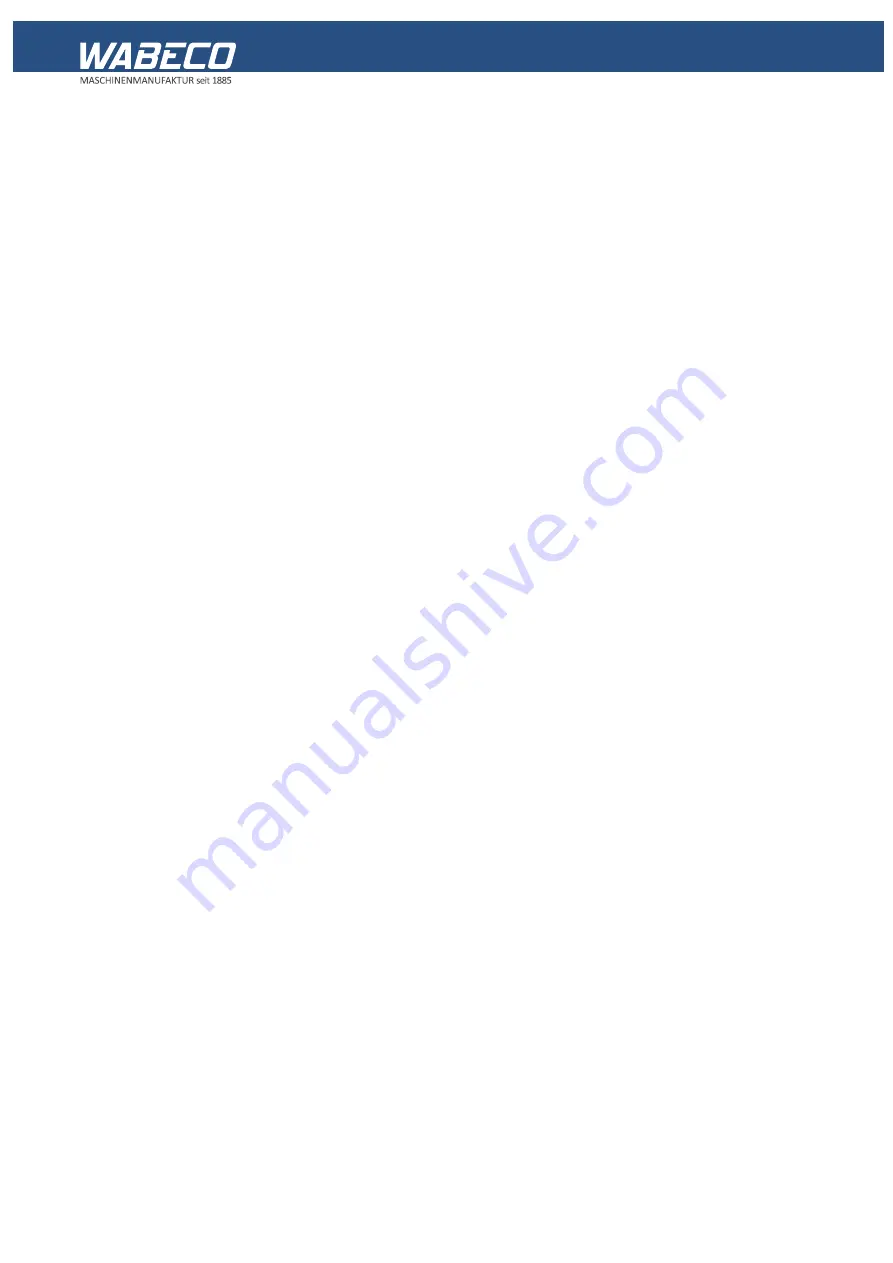
38
5.
Achieving optimum results
and avoiding incorrect usage
It is recommended that:
■
The borer should be fitted and tensioned with the key in such a way that the borer is positi-
oned precisely between the three clamping jaws of the crown gear, quick clamping or collet
chuck
■
Clamp the milling machine with shaft using the collet chuck and the appropriate collets
■
Clamp the milling machine with bored hole and longitudinal groove using the plugged mil-
ling machine spike
When boring, attention is to be paid that:
■
The appropriate revolutions are set according to the diameter of the borer
■
The pressure is gentle enough that the borer is able to cut without straining
■
In the event of too much pressure, the result is early borer wear or even borer breakage or jamming
in the bored hole.
In the event of jamming, immediately bring the main drive motor to a standstill by
pressing the emergency off switch
■
When using hard materials, for example, steel, ordinary boring oil must be used
■
The borer is always to be removed from the workpiece with the spindle rotating
■
When using non-metal materials, for example, wood, tearing on breakthrough can be prevents by
clamping a piece of waste wood under the workpiece to be processed
■
For wood workpieces with a veneer or plastic coating, always work from the side with the veneerWi-
th very thin sheets, also clamp using a piece of waste wood
When milling, attention is to be paid that:
■
T
he appropriate cutting speed is selected (see the section on revolution setting)
For materials with normal firmness values, e.g. steel 18-22m/min
For materials with higher firmness values 10-14m/min
■
The pressure is to be selected so that the cutting speed remains constant
■
For hard materials, use ordinary boring oil
When clamping the workpieces, attention should be paid that:
■
The appropriate clamping screws are used for the T-slots of the milling machine table or use a ma-
chine vice
■
The milling machine table of the cross slide support is to be cleaned of dirt residue and shavings in
order to ensure perfectly even clamping
Содержание CC-F1410 LF hs
Страница 41: ...41 7 Fitting and removing the tools 42 6 Spannen und Ausdr cken der Werkzeuge 1 2 3 4 5...
Страница 64: ...64 16 Drawings and legends 16 2 Electronic hood with 1 4 kW motor 16 2 2 CC F1410 LF 1 5 7 6 4 3 2...
Страница 98: ...98 16 Drawings and legends 16 12 Spindle Z axis with ball screws 16 12 1 F1410 LF F1410 LF hs...
Страница 102: ...102 16 Drawings and legends 16 13 Lateral drive for Z axis with ball screws 6 4 5 4 3 2 1 7 12 8 9 10 11 14 13...
Страница 118: ...118 16 Drawings and legends 16 20 Control panel for 1 4 kW motor 12 1 11 18 2 4 10 8 7 9 6 3 5 5 5 13 14 15 16 17...
Страница 120: ...120 16 Drawings and legends 16 20 Control panel for 1 4 kW motor 7 2 3 8 1 6 10 9 9 10 5 4 11 12 13 14 15 16 17...
Страница 122: ...122 16 Drawings and legends 16 21 Control panel for 2 0 kW motor 5 12 1 11 5 10 9 8 7 6 18 2 3 4 5 13 14 15 16 17...
Страница 124: ...124 16 Drawings and legends 16 21 Control panel for 2 0 kW motor 7 2 3 8 1 11 12 13 14 15 16 17...
Страница 126: ...126 16 Drawings and legends 16 22 Support arm for control panel 1 2 3 4 5 6 8 9 5 4 7 9 8...