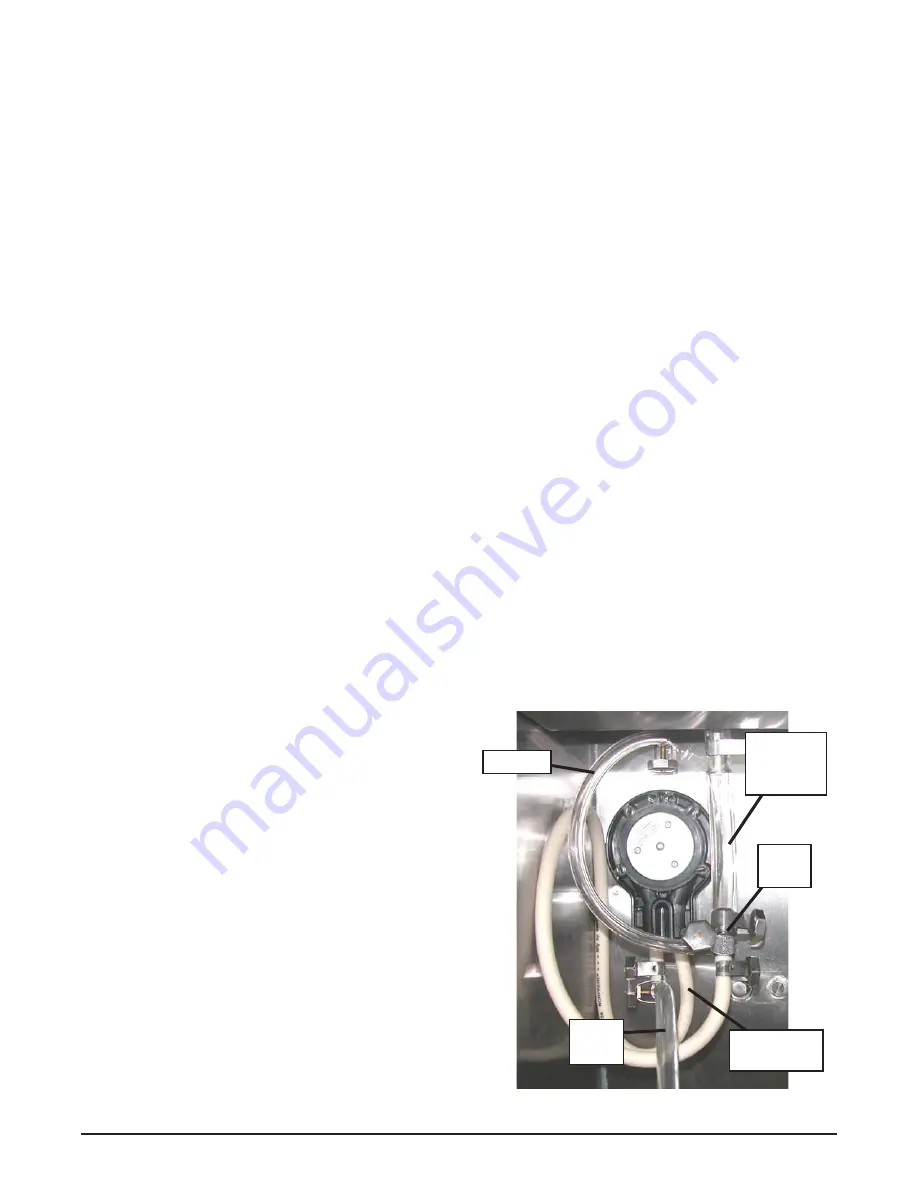
Owner’s Manual #513669
12
O431 I2 Model Machines
J.
When the product is ready, the display will read
“SERVE”. Open the spigot to dispense product.
NOTE
If the product consistency needs to be adjusted, use
the Technician passcode and go to the Basic Set-
tings menu. Adjust the CutOut Consistency higher
to increase the consistency or lower to decrease
the consistency. Make adjustments in increments
of 5 for best results.
K.
The machine dispenses product at a reasonable
draw rate. If the machine is overdrawn, the result
is a soft product or a product that will not dispense
at all. If this occurs, allow the machine to run for
approximately 30 seconds before dispensing more
product. A dispense rate adjustor is located under
the header panel, to the immediate right of the
spigot handle. Turning the knob counterclockwise
will decrease the dispense rate.
L.
Do not operate the machine when the MIX LOW
message is displayed. Refi ll the mix container
immediately.
NOTE
The control has a standby mode for Serve 1 and a
sleep mode for Serve 1 and Serve 2. After a preset
number of freezing cycles in Serve 1, the control will
enter the standby mode (followed by sleep mode)
and remain there until someone draws product or
presses the PUSH TO FREEZE button. In Serve 2
the control directly goes into the Sleep2 mode. In
the sleep mode, the machine will keep the product
below 41°F (5°C). Sleep modes do not take the
place of cleaning and sanitizing. Federal, State,
and local regulatory agencies determine frequency
of cleaning and sanitizing.
3.10 MIX
INFORMATION
Mix can vary considerably from one manufacturer to
another. Differences in the amount of butterfat content
and quantity and quality of other ingredients have a
direct bearing on the fi nished frozen product. A change
in machine performance that cannot be explained by a
technical problem may be related to the mix.
Proper product serving temperature varies from one
manufacturer’s mix to another. Mixes should provide a
satisfactory product in the 20°F to 24°F range. Diet and
low-carb mixes typically freeze to proper consistency at
higher temperatures.
When checking the temperature, stir the thermometer in
the frozen product to get an accurate reading.
Old mix, or mix that has been stored at too high a tempera-
ture, can result in a fi nished product that is unsatisfactory.
To retard bacteria growth in dairy based mixes, the best
storage temperature range is between 33° to 38°F (0.5°
to 3.3° C).
3.11
OPERATION OF MIX PUMP
The mix pumps are operated from the buttons on the
IntelliTec2™ touchpad. When the pump button is pressed
On, the mix pump motor will start pumping mix into the
freezing cylinder. When the set pressure is reached, the
mix pump will shut off automatically.
NOTE
The mix pump motor is equipped with an internal
overload that will “trip”, disabling the pump when
the motor is overloaded. Consult the troubleshoot-
ing section for corrective information. The internal
overload will automatically reset after cooling. If
the condition continues, contact a qualifi ed service
person.
A.
Mix Operation: The peristaltic mix pump contains
one continuous mix pump hose. When looking at
the face of the peristaltic mix pump, the left side
of the hose is the mix intake or pickup. The right
side of the hose is the mix discharge. Mix is drawn
up the pickup side of the hose and transferred
through the discharge side to the machine (Fig.
3-9).
B.
Air Operation: The air compressor operates
whenever the peristaltic mix pump is running.
Air enters through a check valve on the piston
downstroke. The air is discharged through a
second check valve, on the piston upstroke. The
air and mix join at the tee and then travel to the
machine.
C.
The overrun adjustment is preset at the factory.
If an adjustment becomes necessary, refer to
Section 4.
Figure 3-9 Mix Pump Hose Routing
Air Line
Mix
Intake
Mix
Discharge
3-way
Tee
Air/mix to
Freezing
Cylinder
Содержание STOELTING O431 I2
Страница 1: ...Model O431I2 OPERATORS MANUAL Manual No 513669 Rev 0 ...
Страница 2: ......
Страница 20: ...Owner s Manual 513669 14 O431 I2 Model Machines ...
Страница 24: ...Owner s Manual 513669 18 O431 I2 Model Machines ...
Страница 30: ...Owner s Manual 513669 24 O431 I2 Model Machines ...
Страница 34: ...Owner s Manual 513669 34 O431 I2 Model Machines ...