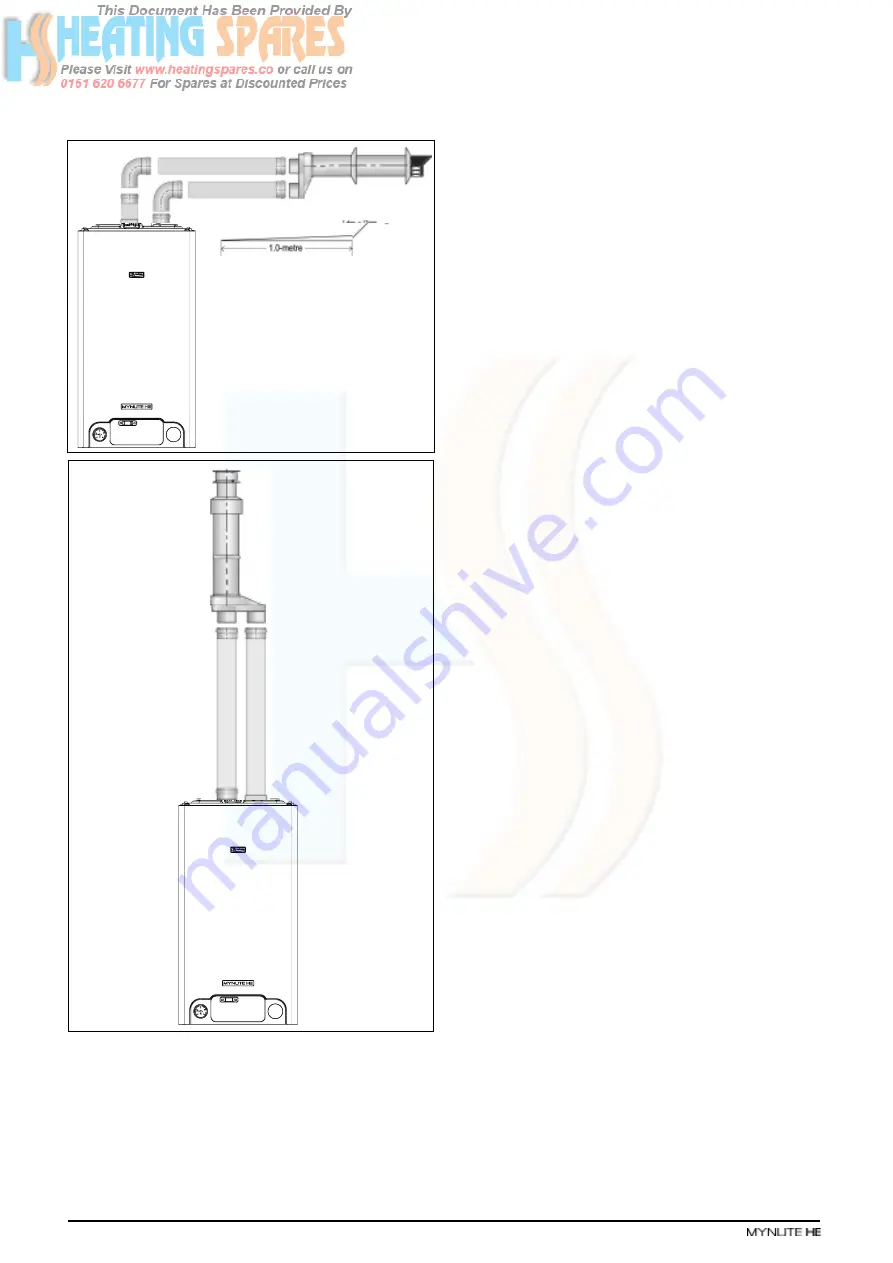
Supplied By www.heating spares.co Tel. 0161 620 6677
14
4.6
CONNECTING THE GAS AND WATER
The appliance is supplied with service valves. The
service valves are of the compression type. The
accessories pack contains sealing washers etc,
for use with the service valves.
When connecting pipe work to the valves, tighten
the compression end first then insert the sealing
washers before tightening the valve to the
appliance.
●
●
●
●
●
You must ensure that the entire flue system is
properly supported and connected.
●
●
●
●
●
Ensure that any horizontal sections of pipe have
a 1º fall towards the appliance (17mm per
1000mm).
Fig. 13
NOTE
It will be necessary to hold the valve with one
spanner whilst tightening with another.
4.6.1
GAS (fig. 6)
The appliance is supplied with a 15mm service
valve, connect a 15mm pipe to the inlet of the
valve and tighten both nuts.
NOTE
It will be necessary to calculate the diameter of
the gas supply pipe to ensure the appliance has
an adequate supply of gas.
4.6.2
FLOW & RETURN (fig. 6)
The appliance is supplied with 22mm service
valves for the flow and return connections, connect
a 22mm pipe to the inlet of each valve and tighten
both nuts.
NOTE
Depending on system requirements, it may
necessary to increase the size of the flow & return
pipe work after the service valve connections.
4.6.3
SAFETY VALVE (fig. 6)
Connect the safety valve connection pipe to the
safety valve outlet. Connect a discharge pipe to
the other end of the safety valve connection pipe
and tighten. The discharge pipe must have a
continuous fall away from the appliance to outside
and allow any water to drain away thereby
eliminating the possibility of freezing. The
discharge pipe must terminate in a position where
any water – possibly boiling – discharges safely
without causing damage or injury, but is still
visible.
4.6.4
CONDENSE PIPE
During normal operation the boiler produces
condense which is collected in a trap located in
the lower part of the boiler. A flexible pipe
(condense outlet pipe) is connected to the outlet
of the trap. The flexible pipe must be connected
to a plastic waste pipe only. The plastic waste
pipe must have a minimum of a 3º fall towards
the drain. Any external run of pipe should be
insulated to prevent the risk of freezing.
CONNECTING THE CONDENSATE OUTLET
Gently pull the condense outlet pipe down from
its location inside the boiler until approximately
100mm protrudes from the underside of the boiler.
Connect a suitable plastic (not copper) pipe (no
less than 20mm diameter) to the outlet pipe and
ensure it discharges in accordance with building
regulations or other rules in force.
4.7
ELECTRICAL CONNECTIONS
The electrical supply must be as specified in
section 3/3A. A qualified electrician should
connect the electrical supply to the appliance. If
controls – external to the appliance – are required,
a competent person must undertake the design
of any external electrical circuits, please refer to
section 8 for detailed instructions. ANY
EXTERNAL CONTROL OR WIRING MUST BE
SERVED FROM THE SAME ISOLATOR AS THAT
OF THE APPLIANCE. The supply cable from the
Fig. 12