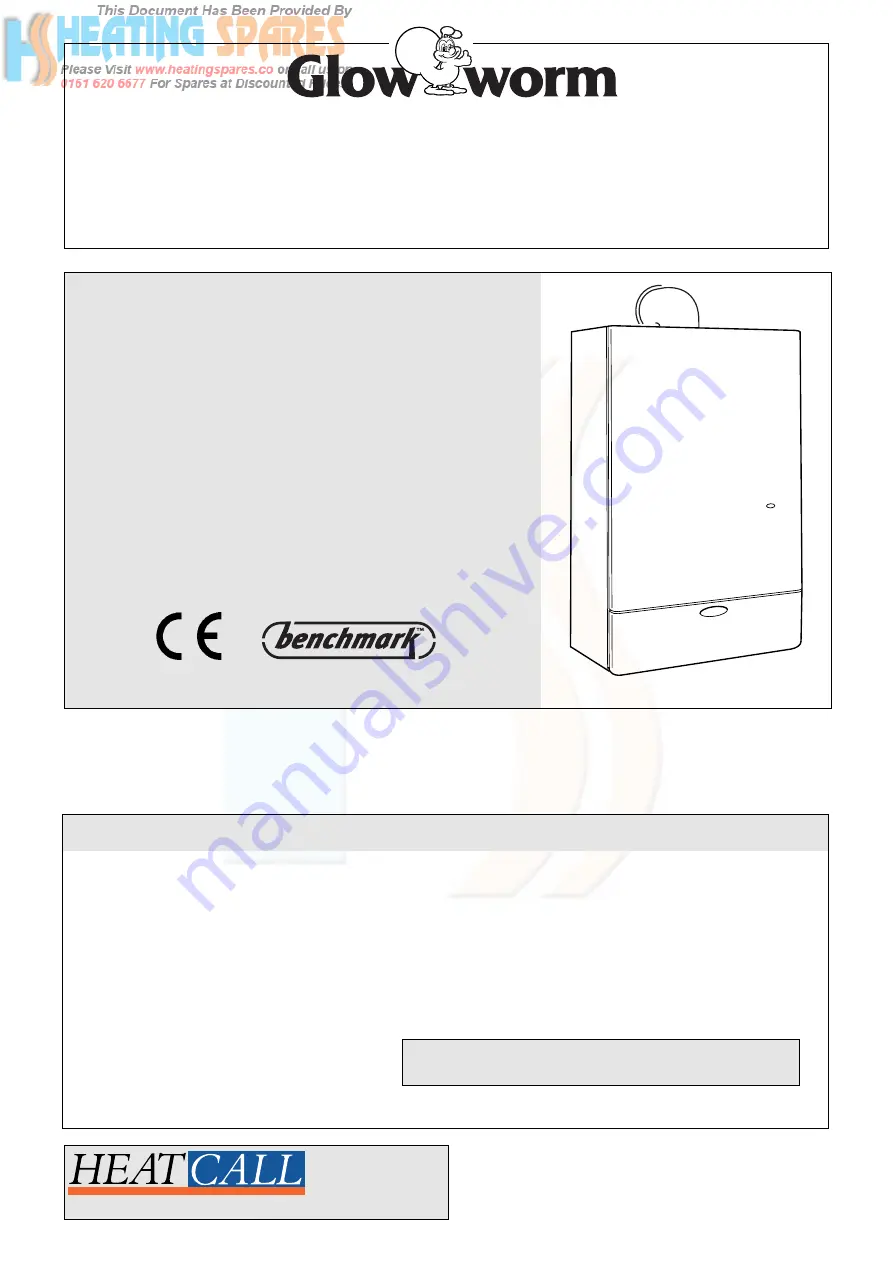
Supplied By www.heating spares.co Tel. 0161 620 6677
221679H.11.00
Hepworth Heating Ltd.,
Nottingham Road, Belper, Derbyshire. DE56 1JT
General/Sales enquiries:
Tel: (01773) 824141 Fax: (01773) 820569
One Contact Local Service
Customer Services:
Tel: (01773) 828100
Fax: (01773) 828070
Instructions for Use
Installation and Servicing
T o b e l e f t w i t h t h e u s e r
This is a Cat I
2H
Appliance
6936
Fanned Flue Combination Boiler
With Honeywell gas control
G.C. No. 47 047 04A
COMPACT 80p
❑
✔
❑
✔
❑
✔
All replacement parts
All labour charges
All call-out charges
Guarantee Registration
REGISTER YOUR GLOW-WORM APPLIANCE
FOR 1ST YEAR GUARANTEE PROTECTION
CALL 0208 247 9857
Thank you for installing a new Glow-worm appliance in your home.
Glow-worm appliances' are manufactured to the very highest standard so we are pleased
to offer our customers' a Comprehensive First Year Guarantee.
In the centre pages are to be found your Guarantee Registration Card, which we recommend you complete and
return as soon as possible.
If this card is missing you can obtain a copy or record your registration by telephoning the Heatcall Customer
Service number 01773 828100.
Our Guarantee gives you peace of mind plus valuable protection against breakdown by covering the cost of:
The instructions consist of three parts, User, Installation and Servicing Instructions, which include the Guarantee Registration Card.
The instructions are an integral part of the appliance and must, to comply with the current issue of the Gas Safety (Installation and Use)
Regulations, be handed to the user on completion of the installation.