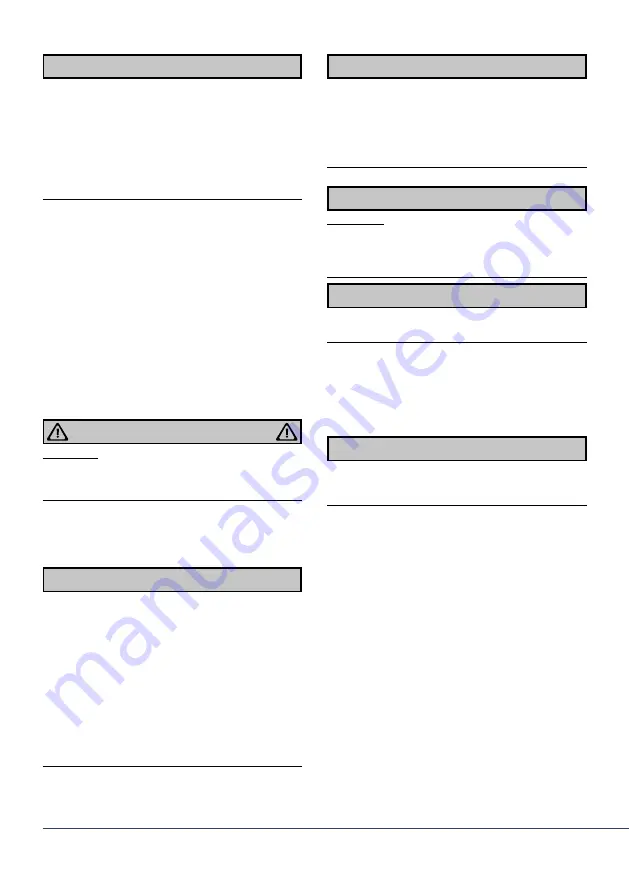
14
ʸ
Ensure that the coolant supply and return hoses have been
correctly installed. Coolant supply = blue, coolant return =
red.
ʸ
Do not use deionised or demineralised water as coolant or
for leak and flow tests. This may shorten your welding torch’s
service life.
ʸ
We recommend the use of Böhler Welding coolant for liquid-
cooled welding torches.
ʸ
The cooling system must be purged of any air each time the
device is commissioned and after every cable assembly
change: disconnect the coolant return hose from the coolant
recirculator and hold it over a collection receptacle. Close
the opening on the coolant return hose. Then re-open it by
abruptly releasing it. Repeat until the coolant flows into the
collection receptacle continuously and without air bubbles.
4.7. Setting the shielding gas volume
ʸ
The type and amount of shielding gas used depend on the
welding task and the gas nozzle geometry.
ʸ
Make all shielding gas connections gas-tight.
ʸ
To prevent the shielding gas supply from becoming clogged
by impurities, the cylinder valve must be opened briefly
before connecting the cylinder. This will expel any impuriti-
es that may be present.
ʸ
Each time the wire is replaced, make sure that the start of
the wire is free of burrs and not bent.
ʸ
Only qualified personnel are permitted to perform work on
the device or system.
ʸ
Consult the documentation for the welding components.
The trigger’s two-cycle mode can be activated when using a
standard welding torch. Further operating modes (e.g. 4-cycle)
and torch handle modules depend on the welding power
source and must be ordered separately.
4.9.1. Trigger function
1. Press and hold the trigger on the handle = start welding.
2. Release the trigger = stop welding.
NOTICE
NOTICE
NOTICE
NOTICE
Risk of injury
Puncture or cut-in wounds may be caused by the wire
electrode.
ʸ
Keep your hands out of the danger zone.
ʸ
Wear the correct protective gloves.
CAUTION !
4.5. Attaching the cable assembly on the machine side
1. Join the central connector and the central socket at the
wire feeder.
2. Use the connection nut to secure both of these.
3. Attach the coolant supply and return connectors to the
MT W
.
4. Attach the shielding gas and control lead connectors in
the case of other machine connections.
4.6. Connecting the coolant
1. Lay the cable assembly connected to the machine side
out straight.
2. Insert the wire into the wire feeder as specified by the
manufacturer.
3. Press the ‘zero-current wire feed’ trigger on the wire
feeder until the wire comes out of the contact tip.
4.9. Torch handle control elements
Risk of burns
The cable assembly overheats if the coolant level is too low.
ʸ
Wear the correct protective gloves.
ʸ
Check the coolant level at regular intervals.
Connecting the coolant (Fig. 3 / p. 3)
1 - Control lead
2 - Coolant supply hose
3 - Coolant recirculator
4 - Coolant return hose
WARNING
4.8. Feeding in the wire
English
- English -
For use with aluminium, copper, nickel and stainless steel wires:
1. Lay out cable assembly straight, screw in contact tip.
2. Slide wire guide containing the brass liner first through the
cable assembly until a noticeable resistance is felt at the
contact tip.
3. Slide clamp nipple, O-ring and nut onto PA liner and tigh-
ten the nut under tension.
4. Mark overlength of the PA liner in front of the wire feed
rolls and cut it off at the mark using the cutter.
ʸ
New, as yet unused PA liners have to be abridged to the
actual length of the cable assembly.
ʸ
For PA liners with an outer diameter of 4.00 mm, the capil-
lary tube in the distance adaptor must be replaced with a
guide tube.
ʸ
For changeable and repluggable torch necks and torch
necks that cannot be changed, combined wire guides with
integral brass liner are used.
ʸ
For changeable torch necks, a neck-liner made of brass is
used.
NOTICE
4.4.2. PA liner