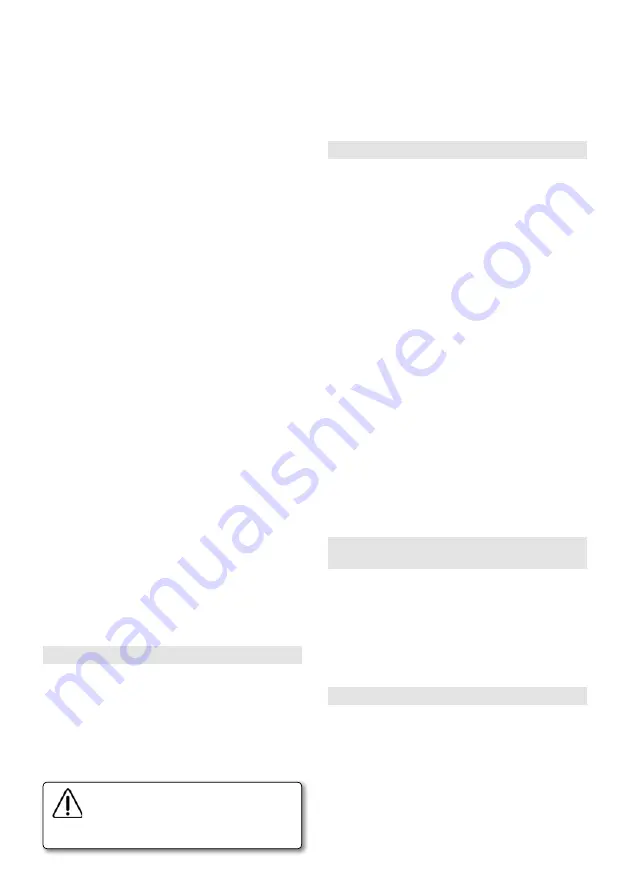
8
To unlock the depth rod E (Fig. 2) loosen the knob H, press
down firmly on adjustment knob F and turn it to raise or
lower the depth rod, if a greater or lesser cutting depth is
required. The gauged adjustment indicator G can be moved
separately from the knob, so that it may be set to zero
from any position using the reference mark. When turning
the knob after adjusting the indicator, both elements will
turn together, there by indicating the degree to which
the rod has been moved. A full turn of the knob moves
the rod by 34 mm, with a maximum distance of 55 mm.
To hold the depth rod in the required position, release
the pressure from the adjustment knob. Next, to ensure
that the rod is firmly held in place, it should be locked
using fastening knob H.
PRECISION ADJUSTMENT.
If you wish to make precision
adjustments to the previously set depth, simply turn
adjustment knob I (Fig. 2). A full turn of the knob moves
the rod by 1 mm, with a maximum distance of 5 mm.
Each division in the gauged fine-adjustment indicator
J (Fig. 2) represents an advance of 0.1 mm.
MAKING DEEP CUTS.
To safely make cuts that are too
deep to be made with a single pass, we recommend
making several successive cuts using the six 3-mm steps
in the revolving depth turret K (Fig. 2).
Lower the machine until the cutting bit is level with
the surface on which the router is resting. Use locking
knob L (Fig. 1) to hold the machine in this position.
Loosen fastening knob H (Fig. 2), then press down and
turn adjustment knob F until the depth rod presses
against the lower step of the revolving depth turret,
using fine adjustment if required. In this position, turn
depth indicator G (Fig. 2) until position zero matches
the reference mark. This will be the starting position
indicating the point at which the bit comes into contact
with the material. Hold the rod in place with knob H
(Fig. 2), release the locking knob L (Fig. 1) and leave the
machine in the off position.
Make the first cut on the material. Turn the turret Q
to the next step and then make another cut, and so on
until the required depth is obtained when the bottom
step is reached.
10. LOCKING THE ROUTING DEPTH
To carry out several repetitive jobs in which the router
depth is always the same, it may be useful to prevent
the head from being released by accidentally moving
the locking knob L (Fig. 1). This may be done by inserting
two M (Fig. 6) in the threaded shaft, one above and one
below the head body. This locks the head at any point
along its depth setting.
When working with the router depth
locked, the tool will be permanently
outside the base surface. Therefore the
following actions must be taken:
- Stop the machine unlatching switch A (Fig. 1) and wait
until the machine has come to a complete stop before
setting it down on its base, on a flat surface, with the
cutting tool free.
- Remove nuts M (Fig. 6) to return to the normal lock
conditions using knob.
11. USE OF PARALLEL GUIDE
The parallel guide is used for trimming edges and cut-
ting slots of different shapes, depending on the profile
shape. Hard metal cutter bits are particularly useful
for smoothing edges and lengthening the working life
of the bits.
The parallel guide N (Fig. 1) is inserted in the openings
on the base O (Fig. 2) and is held in place using the two
knobs P (Fig. 1).
NORMAL SQUARE ADJUSTMENT
– Loosen the base
knobs P (Fig. 1), move the square to the required position
and then tighten the knobs in this position.
PRECISION ADJUSTMENT
– Once the square has been
approximately positioned and held in place, a further
fine adjustment may be made. To do this, loosen square
fastening knob R (Fig. 1), turn the adjustment knob S to
the required measurement, then tighten the square fas-
tening knob again in this position. A full turn of the knob
moves the square by 1 mm, with a maximum distance of
10 mm. The gauged fine-adjustment indicator T can be
moved separately from the knob, so that it may be set to
zero from any position using the reference mark. When
turning the knob S again after adjusting the indicator T,
both elements will turn together, there by indicating the
degree to which the square has been moved, with each
division representing an advance of 0.1 mm.
12. USE OF TEMPLATE GUIDES
(optional accessories)
The template guides are used for routing with a wide
variety of shapes. The chosen template guide U (Fig. 3) is
held to the base V with the two screws W. On making a
copy, a difference between the size of the template and
the routed part will appear. The difference between the
radius of the template guide and the cutting tool must
always be taken into account when making a template.
13. DUST COLLECTOR ATTACHMENT
To attach the dust collector connector X (Fig. 2), place
it in the central recess in base, with the connection
facing the back, and hold it in place with screws Y. If
trimming dovetails with the Virutex PL11 model dove-
tailing attachment, guide and position the dust collector
connector as desired so that the trimmer moves over
the dovetailing attachment better.
The dust collector connector X may be attached either
directly to the suction tubes of AS182K and AS282K
dust collectors, or else by using the smaller-diameter
Содержание FR356Z
Страница 32: ...32 Fig 1 Fig 3 Fig 4 Fig 5 Fig 6 Fig 2 L A R T S N P E Z X P O K F G H E J I V U W C D E1 B M ...
Страница 33: ...33 Fig 7 Fig 8 Fig 9 A1 B1 D1 C1 ...
Страница 34: ......
Страница 35: ......