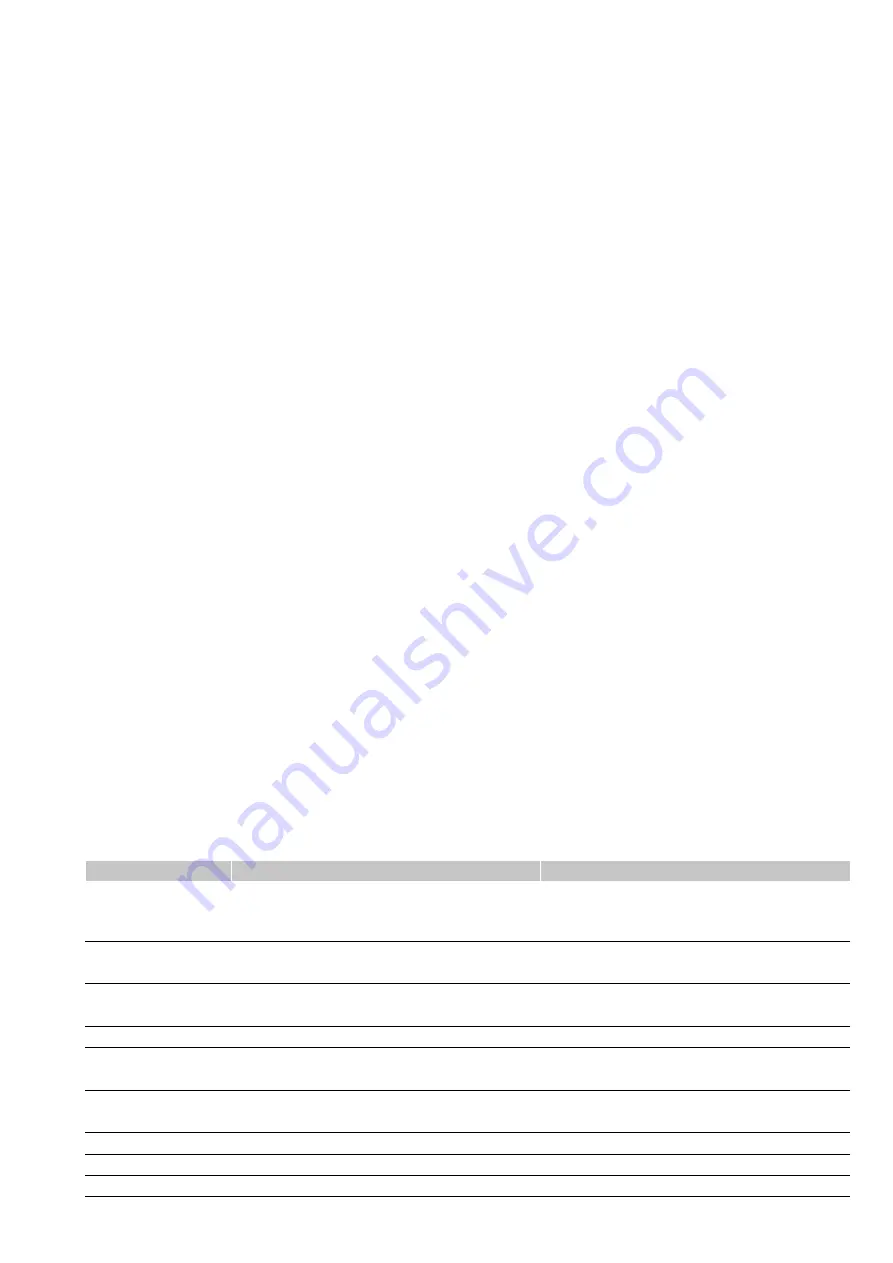
24/28 NT-50907501-KUBAIR-F400-AN-210312
5. START-UP
Before the turbine is started up, make sure that the whole motor and wheel are able to rotate freely and
that there are no objects which may be projected by the turbine. The accessories must be attached to the
casing to avoid any accidental contact with the rotating parts.
The machine must be attached to its support before it is powered on.
Switch on just an instant to check the direction of rotation of the turbine.
WARNING
: The impeller rotating direction must correspond to each speed in the direction indicated by
the arrow on the product. A centrifugal backward fan unit with an impeller that does not rotate in the right
direction still creates a lowrate and a low pressure in the duct. An incorrect rotating direction can lead to an
abnormal overheating of the motor, resulting in its destruction and cancelling our manufacturer’s warranty.
If the rotating direction is incorrect, cut off the electrical power supply, make sure no power is present,
and then reverse the two power supply phases at the level of the motor’s terminal box for the three-phase
motors, or make sure that the mains network connection conforms to the schematic diagram of § "4.2
Technical Characteristics" for the single-phase motors.
While running, make sure that the motor’s absorbed current is not more than 10% above the name plate
indicated current.
Once the installation and tests have ended, present the main points of the operating and maintenance
manual to the user; the following should be explained:
• How to start up and shut down the device.
• How to change the operating modes.
Then hand over to the user with the technical instructions for use of the casing and assembled accessories
(control panel, etc.) so that they can be accessed at all times.
6. MAINTENANCE
The maintenance frequency depends on the operating conditions. If the air is dirty (poor quality), the
duration between two visits must be shortened.
WARNING
: Before any maintenance operation, cut off the power supply upstream of the casing and make
sure that it cannot be re-established during the intervention (lockout).
The motors used do not require any particular maintenance. They are fitted with sealed greased-for-life
ball bearings.
6.1 Maintenance periodicity
Unit/Item
At commissioning
Every 6 months minimum
Turbine
Check the rotating direction ; make sure that the
moving and fixed parts do not rub together
Clean, if necessary ; make sure that the moving
and fixed parts do not rub together
Electric motor
Check the connections, in particular, the ground
connection
Retighten the lugs, if necessary ; check the
nominal current
Power switch
Check the connections, in particular, the ground
connection
Retighten the lugs, if necessary
Pressure relief switch
Check the electrical/aeraulic connections
Check the operation
Control panel
Make sure that there are no defects ; check the
connections, in particular, the ground connection
Make sure that there are no defects ; retighten
the lugs, if necessary
Plastic dome
Make sure that the cooling holes are not
obstructed
Check the general condition ; make sure that
the cooling holes are not obstructed
Protection gratings
Make sure that they are present
Clean, if necessary
Duct networks
Make sure that there are no leaks
Clean, if necessary
Attachment
Check the mechanical tightness
Retighten the screws, if necessary