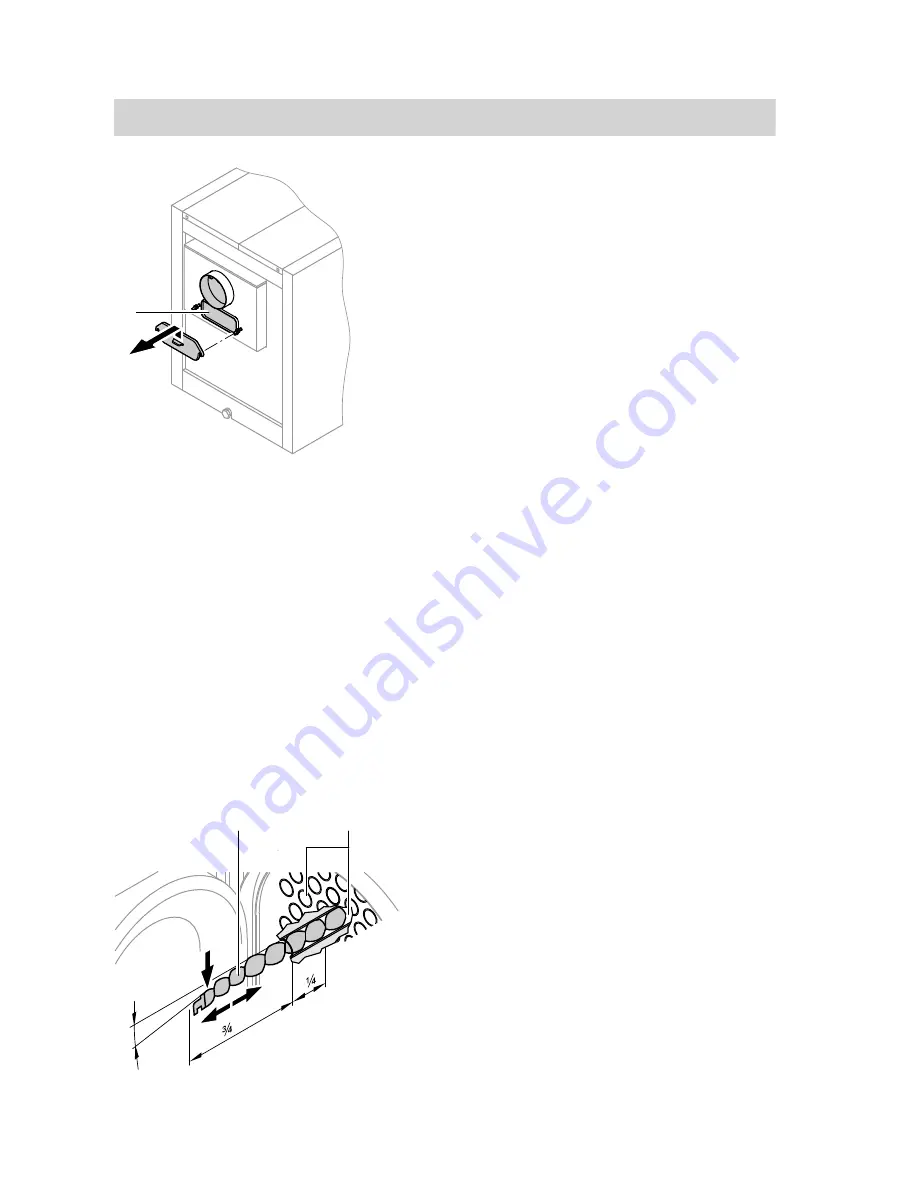
12
D
3.
Remove combustion residues from
the flue and the flue outlet through the
cleaning aperture in outlet
D
using a
vacuum cleaner.
Inserting the turbulators
!
Please note
Burner adjustments and specific
system conditions can cause the
turbulators to move forward,
which may result in them being
burnt. This can also lead to dam-
age to the thermal insulation on
the boiler door.
Before insertion, the turbulators
must be slightly bent (see
steps).
10-15°
B
A
1.
Push turbulators
A
approx. ¼ of
their length into hot gas pipes
B
.
2.
Bend turbulators approx. 10-15°.
3.
Push the turbulators into the hot gas
flues as far as they will go. When
doing this, check the prestress.
Note
Ensure that turbulators cannot easily
be pulled out of the hot gas flues.
Commissioning, inspection, maintenance
Further details regarding the individual steps
(cont.)
5692 701 GB
Содержание VITOPLEX 100
Страница 31: ...31 5692 701 GB...