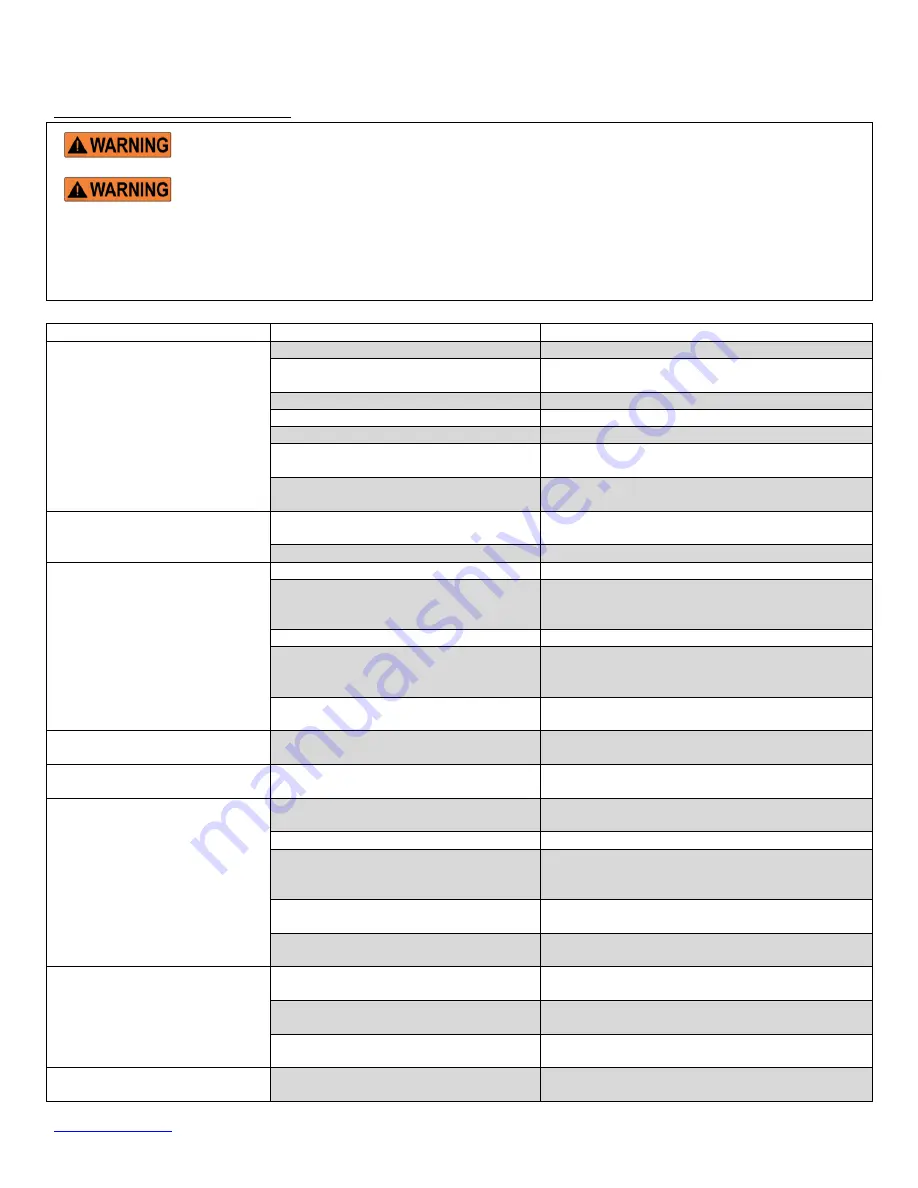
Operator’s Manual
2/2/21
EHLT, MANUAL.DOCX
Copyright 2020, Vestil Manufacturing Corp.
Page
22
of
24
TROUBLESHOOTING GUIDE
Care should be taken to identify all potential hazards and comply with applicable safety procedures
before beginning work.
Remove any load and install the maintenance props before beginning any inspection or service on
the lift table. See below.
Only qualified individuals trained to understand mechanical devices, electrical and hydraulic circuits, and the hazards
associated with them, should attempt troubleshooting and repair of this equipment.
Consult the factory for any problems not addressed in this manual. ALWAYS have the product serial number or model
number on hand when calling the factory.
PROBLEM
POSSIBLE CAUSES
ACTION
Power unit doesn’t run when “UP”
button is pressed.
Transformer fuse is blown.
Test with meter. Replace if bad.
No supply voltage.
Test with meter. Check fuses, breakers, and overloads to
determine the cause
Upper-travel limit switch is engaged or bad.
Inspect and test switch. Replace if bad.
Bad control transformer.
Check for 24 VAC at secondary. Replace if bad.
Bad motor relay coil.
Test with meter. Replace if bad.
Bad solenoid start switch (DC units).
The green LED on motor relay will be off, or will turn off
when the UP pushbutton is pressed.
Battery voltage low (DC units).
Test with meter. Charge battery if low (is the motor relay
LED on?)
Motor runs but platform doesn’t
move. Power unit not noisy.
Motor rotation is wrong (AC-powered units
only).
Verify the motor runs CW, opposite the shaft end.
Pump is failing to produce pressure.
Consult factory.
Motor hums or pump squeals, but
the platform does not move, or the
platform moves only slowly.
Pump is failing to produce pressure.
Consult factory.
Excess voltage drop to motor, due to power
wire size too small, wire run to long, or
incoming voltage too low.
Check the power installation for adequacy. Check the
incoming voltage
while the motor is running
. Correct
any problems found.
Motor is “single-phasing”.
Determine and correct cause of voltage loss on phase.
Pressure relief opening at full pressure.
Check for structural damage or binding of the scissor
legs, etc.
Check for platform overload condition.
Contamination holding open the lowering
valve or the check valve.
Remove and inspect valves. Clean per instructions in the
“Inspection and Maintenance” section.
Platform raises, then drifts down.
Contamination holding open the lowering
valve or the check valve.
Remove and inspect valves. Clean per instructions in
“Inspection and Maintenance” section.
Spongy or jerky platform movement.
Excessive air in the hydraulic cylinders.
Bleed air per procedure described in the “Inspection and
Maintenance” section.
Platform won’t lower.
Perimeter toe guard actuated.
Check for a toe guard extrusion or rubber corner that is
stuck. Adjust if necessary.
Perimeter toe guard switch or wire broken.
Inspect visually; check with mutimeter. Repair as needed.
Solenoid coil is bad.
Check with multimeter using the diode-check function.
(Reading for ohms will not provide an accurate test of
the coil). Replace if bad.
Physical blockage of the mechanism.
Inspect for foreign material or objects blocking the
scissors or the rollers.
Solenoid valve, flow control, or suction hose
screen plugged.
Remove and inspect valves. Clean per instructions in
“Inspection and Maintenance” section.
Platform lowers too slowly.
Solenoid valve, flow control, or suction hose
screen plugged.
Remove and inspect valves. Clean per instructions in
“Inspection and Maintenance” section.
Velocity fuse locking (indicated by platform
only slowly creeping down).
Check for air in hydraulic system. Bleed air as needed.
Flow control valve spool sticking.
Remove and inspect valves. Clean per instructions in
“Inspection and Maintenance” section.
Platform lowers too quickly.
Flow control valve spool sticking.
Remove and inspect valves. Clean per instructions in
“Inspection and Maintenance” section.