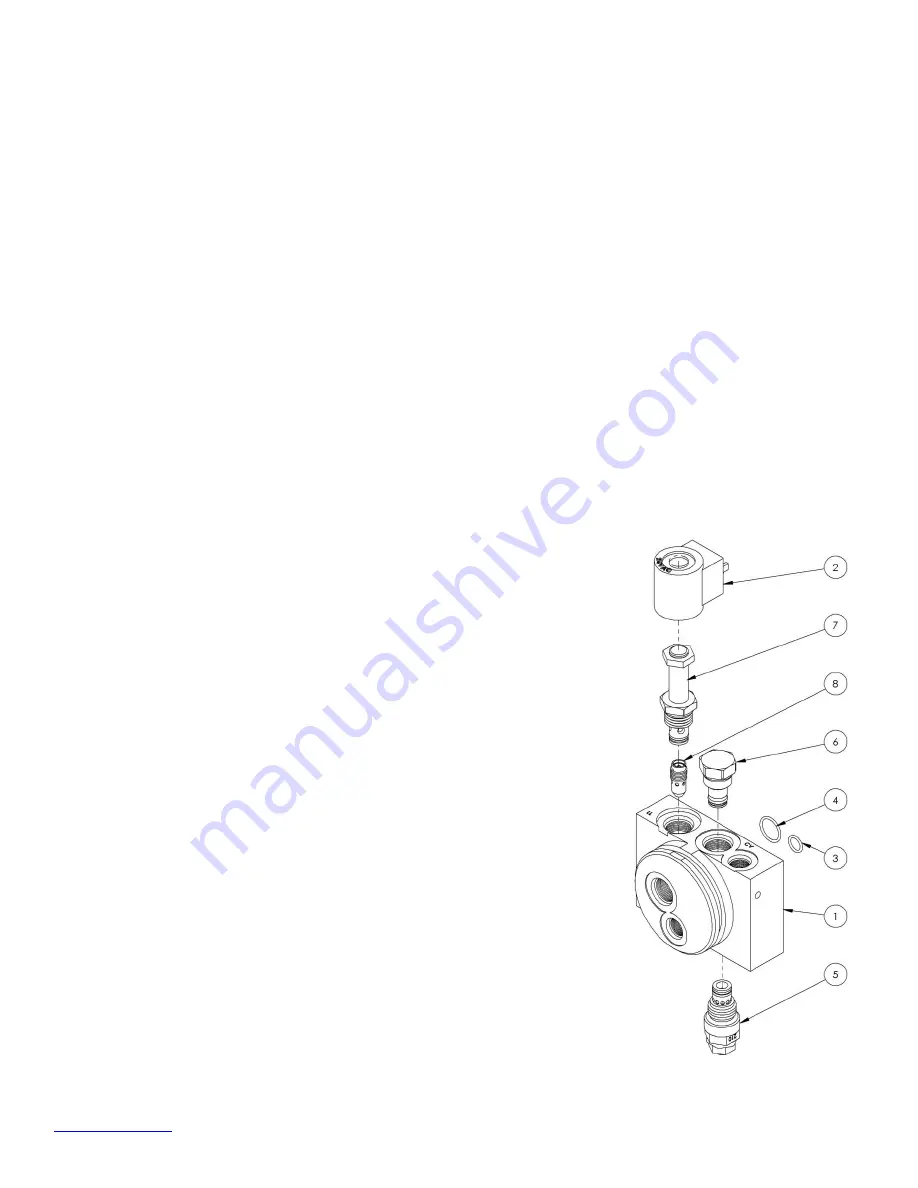
Operator’s Manual
2/2/21
EHLT, MANUAL.DOCX
Copyright 2020, Vestil Manufacturing Corp.
Page
20
of
24
1.
Oil level. The oil should be 1” to 1-½” below the reservoir fill hole with the platform in the fully lowered
position. See the Annual Inspection section for the hydraulic oil specification.
2.
Worn or damaged hydraulic hoses or electrical wires.
3.
Wear in the pivot points on the legs.
4.
Looseness or wear in the rollers.
5.
Integrity of the retaining hardware on all rollers and all pivot point pins.
6.
Integrity of the frame anchor bolts, and for cracks in the concrete around them.
7.
Proper functioning of any hand- or foot-operated mechanisms.
8.
Unusual noises or movement during operation.
9.
Condition of all information, safety, and warning labels. These should be clean and clearly legible.
10.
Dirt and debris. Clean, sweep, or wipe down as needed.
Annual inspection.
Check the condition of the oil. Change the oil if it darkens, becomes gritty, or turns a milky color (indicating the
presence of water). Replace with an anti-wear hydraulic oil with a viscosity grade of 150 SUS at 100°F (ISO 32 cSt @
40°C), such as AW 32, HO 150 or Dexron non-synthetic transmission fluid. You may use a synthetic transmission fluid if
you flush the system with the synthetic fluid before filling the reservoir. 150 SUS at 100°F (ISO 32 cSt @ 40°C) or Dexron
transmission fluid.
Solenoid valve maintenance.
In the event that the platform creeps down slowly after releasing the “DOWN”
control, it will be necessary to remove the lowering cartridge valve for inspection
and cleaning.
1.
Remove any load from the platform.
2.
Raise the platform. Lower the maintenance props into the side frame.
Lower the platform until it rests on the props.
3.
On most EHLT models, the power unit is attached to the hinged side of
scissor lift mechanism. The manifold assembly is attached to the end of
the power unit.
4.
Remove the nut holding the solenoid coil (item (2), right) on the
solenoid valve stem. Remove the coil (2), then unscrew the valve (7)
from the manifold.
5.
Inspect the valve for contaminants. Inspect the O-rings and back-up
washers for cuts, tears, or other damage.
6.
With the valve immersed in mineral spirits or kerosene, insert a thin
tool such as a small screwdriver or a small hex wrench in the hole at
the bottom of the valve (illustration, next page). Push the spool in and
out several times. A properly functioning spool should move freely,
with about 1/16” of travel. Use mineral spirits to flush the valve.
7.
If the spool continues to stick, the stem could be bent. The valve will
need to be replaced.
8.
Blow the valve off with a compressed-air gun while again pushing the
spool in and out.
9.
Inspect the bottom of the manifold’s valve cavity for contaminants.