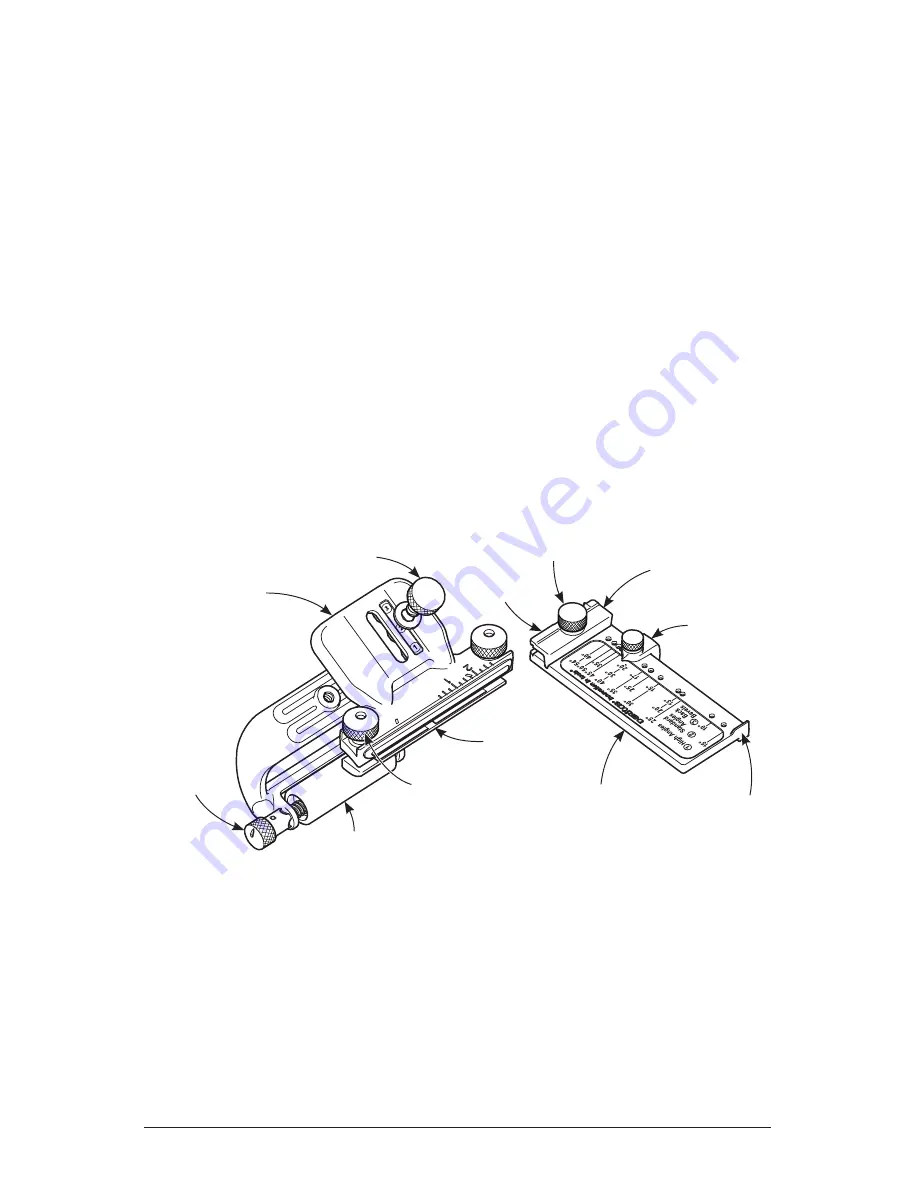
This Veritas
®
Mk.II Honing Guide is an all-in-one system for sharpening
edge-cutting tools. The great advantage of this system is that it has everything you
need to precisely set primary bevel angles for high-angle and standard-angle blades,
as well as back bevels. The ranges are numbered and color-coded for clarity and
ease of use. The registration jig not only squares the blade in the carrier, but also
sets the appropriate blade projection for the desired bevel angle. It lets you sharpen
consistently to the same result or make a controlled change, as desired. This not only
makes tool sharpening on bench stones and surface plates faster, but also reduces the
wear caused by needless reshaping of edges.
This honing guide can be used to sharpen fl at or tapered blades up to 2
7
/
8
"
wide and
15
/
32
"
thick in the standard-angle confi guration. (The thickness is limited to 0.254
"
in the high-angle confi guration and to 0.282
"
in the back-bevel confi guration.)
Our eccentric roller makes it easy to create a micro-bevel without resetting the
blade in the guide.
The main components are die-cast zinc/aluminum alloy and the other parts are all
precision machined from brass or steel for durability and accuracy.
Note:
Before using the honing guide, apply a drop of oil to the junction of the roller,
as shown in
Figure 15
.
Step 1: Lapping
Since a sharp edge is basically the meeting point of two smooth surfaces, the fi rst
thing to ensure is that the face or bottom of any blade is perfectly smooth in the area
near the cutting edge before you attempt to hone the bevel.
An easy way to lap a new blade is on a water stone of 800 or 1000 grit; only on a
very wide blade would you have to resort to a coarser stone such as 250 grit. It need
not be lapped fl at along the entire face, particularly in the case of plane blades, but
Figure 1: Mk.II honing guide components.
Registration
Stop
Fence
Registration
Jig
Registration Jig
Clamp Knob
Blade Clamp
Knob
Clamp Bar
Micro-Bevel
Knob
Roller
Blade Carrier
Blade Carrier
Locking Knob
L-Bracket
Registration
Jig Clamp
2
Содержание Mk.II Honing
Страница 1: ...Mk II Honing Guide 05M09 01 U S Pat No 7 553 216 ...
Страница 13: ...05M09 09 Patent Pending Narrow Blade Head ...