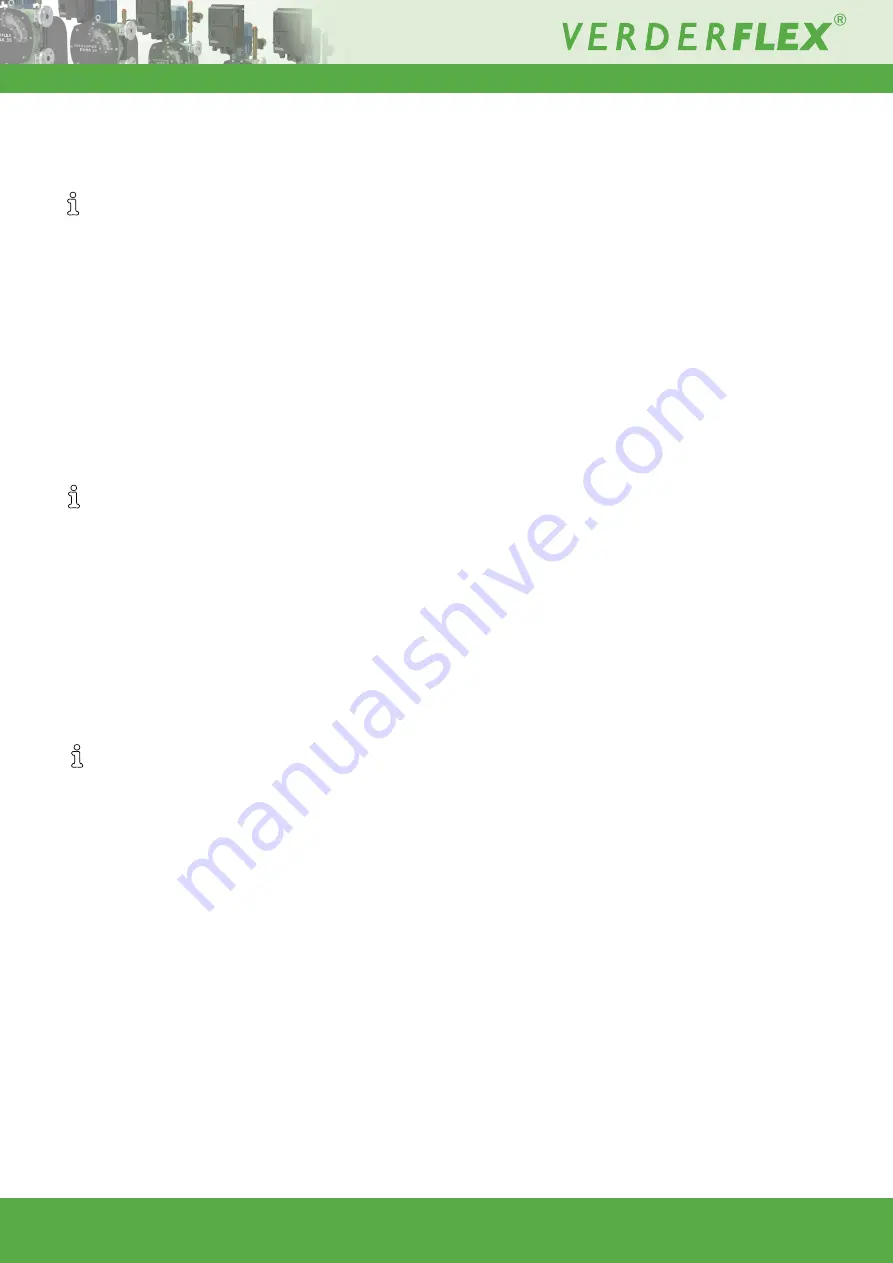
iDura 05-35
Version 1.0v-11/2020
© Verder International B.V
11 | Page
7 Service and Inspection of
Electrical Components
It is understood that electrical components must be
periodically inspected to ensure site health and safety
regulations. Only a trained electrician should service the
pump’s electrical components. When doing so, ensure the
following:
1. Power to the inverter is disconnected and locked out
2. The inverter has been turned off and locked out
3. The speed dial is set to minimum and directional dial is set
to zero
4. The inverter has been allowed at least 10 minutes to de-
energise.
8 Troubleshooting for the iDura
(Inverter Range)
A comprehensive list of error messages and their causes
can be found in the Invertek OptiDrive E3 operation
manual.
Below are the typical troubleshooting error messages that
may be received based on Verder factory settings and
relate to the pump configuration:
1. “
E-TriP
” - the hose burst sensor has been triggered. Check
for a hose burst.
2. “
l_t_trP
” - suspected motor overtemperature. Allow motor
to cool and restart inverter.
8.1 Hose Burst Detection and Vent Kit
Hose burst sensor supplied as standard with the iDura,
have been pre-wired to the inverter. No further wiring has
to be done by the user to use the hose burst detection.
Verderflex hose burst detector and vent kit provide three
basic functions:
1. Stops the pump in conjunction with the inverter, in
case of accidental hose burst;
2. Detect over pressure inside the pump;
3. Release excess pressure from pump housing
The calibrated sensor detects any increase in the pressure
inside a pump casing. As the pressure threshold is reached, the
sensor changes state and this can be used to turn-off the pump.
The system has a detection threshold of 0.4 Bar (5.8 P.S.I) and
when the casing pressure exceeds this, it initiate triggers the
inverter to stop the pump. In the event of a pressure rise inside
the pump casing exceeding 2bar, the vent kit helps to release
this excess pressure from the pump.