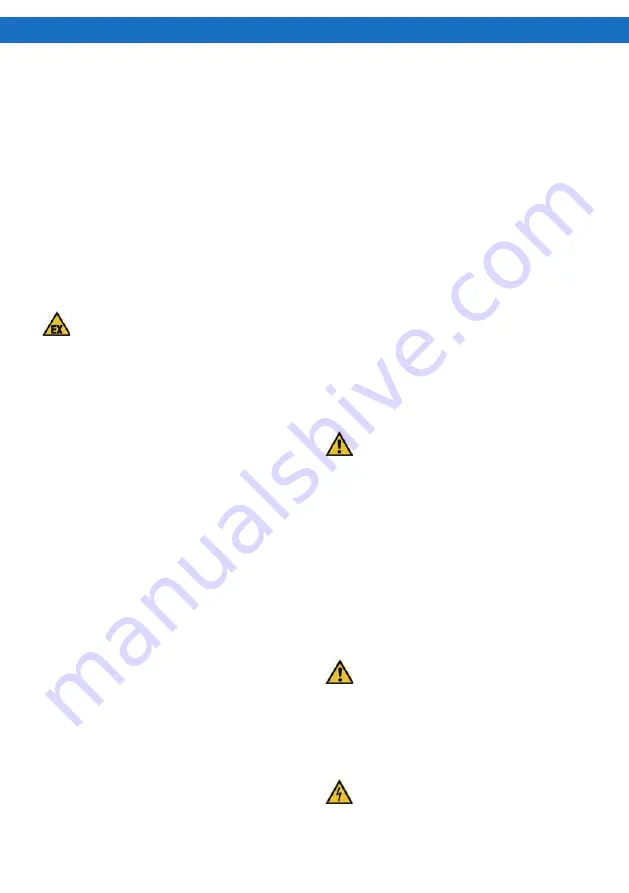
English
13
12
08.2017
50229 01
50229 01
08.2017
Limitation of the total thickness of paint or insulation
layer depending on the individual explosion group:
– IIA, IIB: Total layer thickness ≤ 2 mm
– IIC:
Total layer thickness ≤ 0,2 mm
Limitation of the surface resistance of the used paint or
resin to:
– IIA, IIB, IIC, III surface resistance ≤ 1GΩ for motors of
group II and group III
Breakdown voltage ≤ 4 kV for explosion group III (only
dust, measured according to the method described
in IEC 60243-1 for thickness of insulation material).
In addition the specifications of IEC/EN 60079-32
Electrostatic risks, especially annex A: Basics of static
electricity, annex B: Electrostatic discharges in special
situations and annex C: Combustibility of materials
should be observed.
Spare parts
Except for standard, commercially available
and equivalent parts (like anti-friction bear-
ings) only original spare parts (see spare
parts list) shall be used; this applies espe-
cially for seals and connection parts. For
spare parts orders the following information
is necessary:
– Spare parts name
– Motor type
– Motor number
Storage
For storage or use outside we recommend the use of
a protection cover. A long term exposure with direct
intensive solar radiation, rain, snow, ice or dust must be
avoided.
Long term storage (more than 12 months)
Long term storage must be done indoors in vibration-
free, dry rooms with temperatures not below -20°C and
not above +40°C. The storage environment must not
contain aggressive gas, vapours, dusts and salts. Prefe-
rably motors shall be moved and stored only in original
packing. Storage and transport with motors standing on
their fan covers is not allowed. Additionally unprotected
metal surfaces like shaft ends and flanges must be pro-
tected with a medium for longtime corrosion protection
in addition to the existing factory-provided temporary
corrosion protection. If there is a risk of motors being
covered by moisture from condensation, please provide
precautionary measures against humidity. Than a
special packing in airtight sealed plastic foil is necessary
or as alternative packing in plastic foil with desiccants.
Please put desiccant bags in the terminal box as well.
For the transport please use the eye bolts/attachment
eyes of the motors together with suitable lifting accesso-
ries. The eye bolts/attachment eyes must only be used
for lifting the motors without additional mountings like
foundation plates, gears and others.
Motors with reinforced bearings are supplied with a
transportation safety device. The transportation safety
device at the shaft end must only be removed during
installation of the motor and before switching on.
Turn the shafts at least once a year so that false
brinelling is avoided. During longer periods of storage
the working life of the grease is reduced (ageing). When
using open bearings it is recommended to check the
condition of the grease once a year. If a pollution or
oil drainage is visible, the grease must be exchanged.
Closed bearings (ZZ 2RS) must be replaced after
storage times > 48 months.
Disposal
When disposing of the motors please observe appli-
cable national law.
In addition please take care that all oil and grease
is disposed according to the ordinance of waste oils
(Altölverordnung). They must not be contaminated with
solvents, cold cleaners and paint residues.
Before recycling the individual materials must be
separated. Most important components are grey cast
iron (housing), steel (shaft, stator and rotor sheets,
consumables), aluminium (rotor), copper (windings) and
plastics (insulation materials like for example Polyami-
de, Polypropylene and others). Electronic components
like printed circuit boards (inverter, encoder, etc.) must
be recycled separately.
Terminal board connections
In standard design surface cooled motors
are adapted for both rotational directions.
An exception are the 2-pole motors from size
355 and low-noise motors, which are charac-
terized by a “G” behind the number of poles.
They are equipped with a fan dependent on
the direction of rotation. If such fans or
return stops are used a sign for sense of
rotation has to be fixed on the fan cover.
The connections U1, V1, W1 at phases L1, L2, L3
(in alphabetical or natural succession) always produce
clockwise rotation. However, if the machine is marked
„DL“ in the type designation, the motor is already swit-
ched to the lefthand drive.
The direction of rotation can be reversed by direct
switching on by reversing two mains conductors on the
terminal plate of the motor.
A change in direction of rotation is not
permissible in the case of design with return
stops or/and rotation-dependent fans.
For a machine with only one shaft end or two shaft
ends of different thickness, the direction of rotation of
the rotor, which an observer observes when looking at
the end face of the single or thicker end of the shaft, is
considered to be the rotational direction.
For each motor the correct connection
diagram is attached. The connection must be
done accordingly. For the connection of
auxiliary circuits please see the additional
connection diagram, which is also attached.