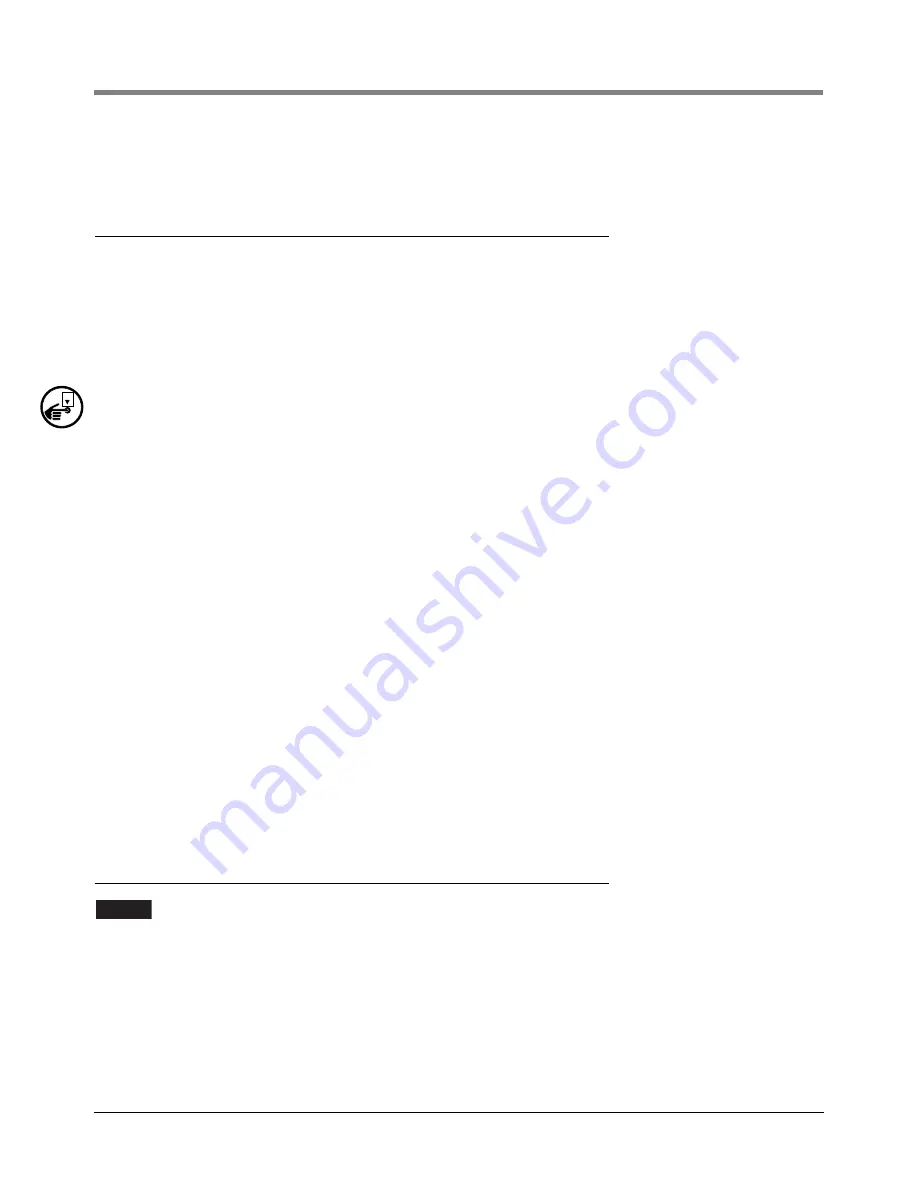
4-5
4
Vac System Testing - TLS-350/350R Consoles
Vacuum Integrity Test Prior to Filling Tank (Optional)
Enter the pressure at which the installed Relief Valve is rated to open (the vent pressure is stamped on the body of
the V-R Relief Valve). The permitted range is -5 to -9 psi (-34 to -62 kPa). Default vent pressure is -9 psi. Press
ENTER to confirm your entry. Press Tank/Sensor to setup another Vac Sensor.
Vacuum Integrity Test Prior to Filling Tank (Optional)
Skip to ‘Running a Manual Test’ below if this optional test is not going to be performed. If an external vacuum
source is not used to produce a vacuum in the monitored zones prior to startup, you must perform a ‘Manual Test’
on each sensor to clear the ‘No Vac’ alarm.
A procedure to test the integrity of the interstitial spaces monitored by the Veeder-Root Vacuum Sensors is
discussed in this section. An external vacuum source and necessary fittings must be supplied by the customer.
Before beginning this procedure all vacuum sensor components in the containment sump must be installed as
described in this manual and be connected to a Smart Sensor module in the TLS Console.
1. Shut off, tag, and lock out power to the pump.
2. At the TLS Console, configure each of the monitored Vac Sensors in the containment sump (ref. TLS-3XX
Setup Manual, P/N 576013-623). Go to the Smart Sensor Diag and place each of the monitored Vac Sensors
in EVAC HOLD (ref. TLS-3XX Troubleshooting Manual, P/N 576013-818).
3. At the 3-way ball valve connected to the tank’s interstitial riser cap, connect the external vacuum source to the
valve’s top barbed fitting. Rotate the valve handle to its up position and pull a vacuum down to -8 psi (-55.1
kPa), or if a relief valve is present, down to 1 psi (6.89kPa) above the relief valve’s opening pressure (e.g., if
relief valve opens at -7 psi [-48.26 kPa], pull the vacuum down to -6 psi [-41.36kPa]). When the desired
vacuum is attained, rotate the valve handle to its down position. Remove the external source from the valve’s
upper barbed fitting.
4. If necessary, repeat this procedure for the product line’s interstitial space, the vapor line’s interstitial space and
the double-wall containment sump’s interstitial space.
5. With all of the monitored interstitial spaces under vacuum, at the TLS Console, stop the EVAC HOLD for each
Vac Sensor. After a minimum wait of 12 minutes, monitor the Leak Rate and Time to No Vac display for each
Vac Sensor. Record the displayed values for each of the containment sump’s Vac Sensor in the chart in
Appendix A.
As a
g
eneral
g
uideline, the Time to No Vac should ideally be 100 hours, and should not be less than 24
hours. Also, a Leak Rate
g
reater than 22.4
g
ph (84.79 litre) will
g
enerate a Vacuum Warnin
g
. Both of these
dia
g
nostics are indicators of whether the system has a si
g
nificant vacuum leak. If either dia
g
nostic exceeds
the
g
uideline, the source of the leak should be corrected before the system is started up. Once the leak(s) is
corrected, repeat steps 2-5.
6. When the monitored interstitial spaces under vacuum are within normal operating limits as described in Step 5,
fill the tank.
7. Once the tank is full, restore power to the pump.
Running a Manual Test
This test is required for each sensor.
You enter the DIAG MODE of the TLS Console by pressing the MODE key until its display appears. Press the
FUNCTION key to select diagnostic functions and the STEP key to view each of the Function’s displays. To enter
changes to displayed data, use the same front keys used enter to system programming selections (i.e., ENTER,
CHANGE, etc.). Figure 4-4 displays the Vac Sensor Manual Test procedure steps and Figure 4-5 displays the Vac
Sensor Evac Hold procedure steps.
OFF
NOTICE