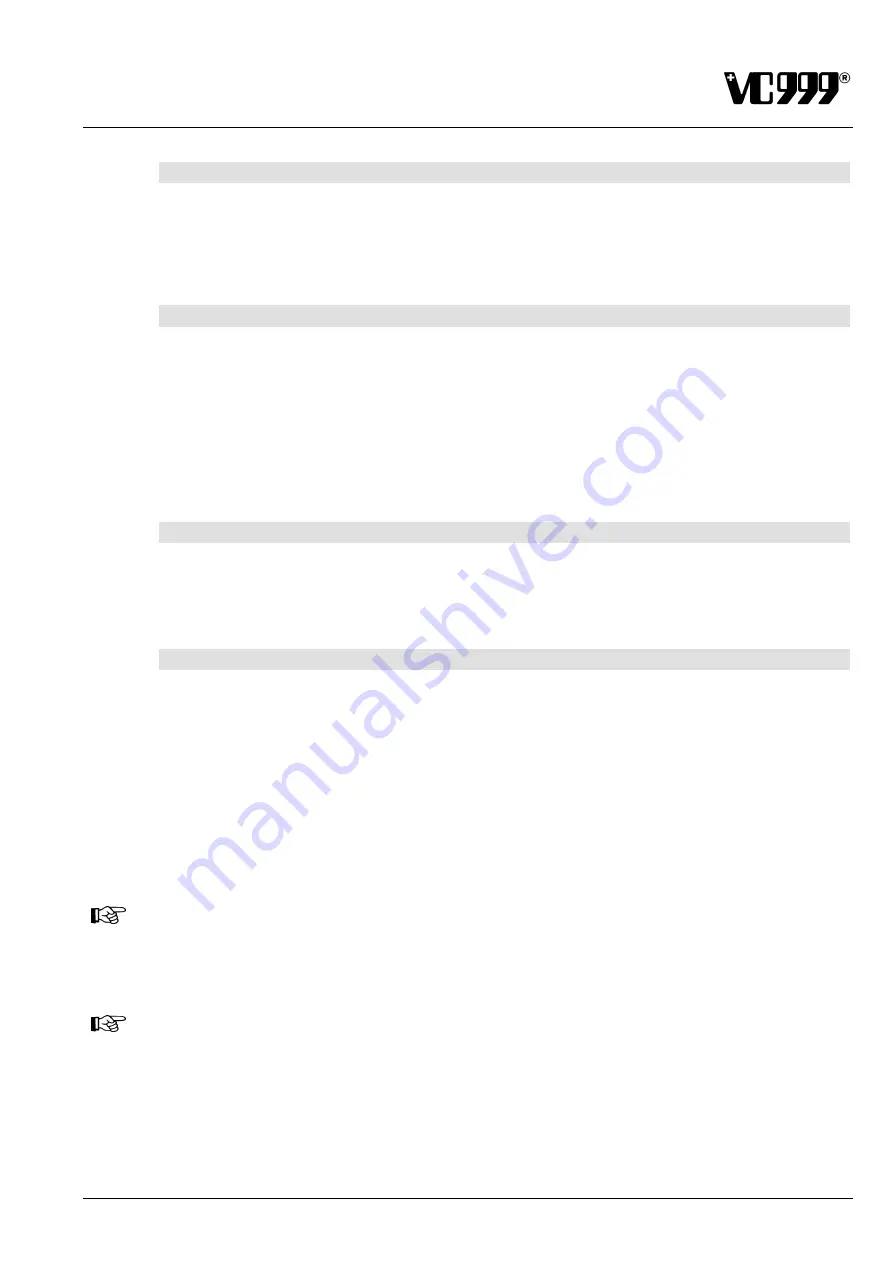
Vacuum Packaging Machine VC999 K7
Operation
2008-11-26
Art.-No. 592.016
Page 35/121
9 Operation
This section is aimed at "users" of the Vacuum Packaging Machine, who use and monitor them in nor-
mal operation. It provides all the information required for operation, from start-up through to operation
and shutdown of the Vacuum Packaging Machine.
9.1
Requirements for operation
Before the Vacuum Packaging Machine can be started up, the following requirements must be met:
•
The Vacuum Packaging Machine must be properly installed and connected by authorized and fully
qualified personnel (Service personnel).
•
The emergency stop buttons must be released.
•
The vacuum chamber must be clean and dry.
•
The conveyor belt must be tensioned and centered as far as possible.
9.2 Preparation
Before you can start packaging, you must prepare the product for packaging, prepare the packaging
material and adjust the Vacuum Packaging Machine to suit the product to be packed.
9.2.1
Preparing the product
Read the part entitled "Suitable products" in section 2.3 „Use in accordance“ to determine which prod-
ucts are permitted for packaging with the Vacuum Packaging Machine.
The chamber dimensions of the vacuum chamber dictate the maximum product size. Read the section
3.3.1 „Dimensions“. To achieve the optimum packaging result, observe the following points when pre-
paring the product for packaging:
•
the product portion size should be selected to avoid soiling the bag opening when the product is in-
serted.
•
cooked products should be left to cool as long as possible.
NOTICE
The boiling temperature falls in the vacuum, so that warm products start to evaporate heavily,
impairing the vacuum quality and the pump capacity. Choosing a suitable type of vacuum (see
description
Mask 101/102: Parameter 1/2 and 2/2
).
NOTICE
It is vital to comply with the relevant health and safety regulations when packaging foodstuffs
or sterile products, otherwise the products may be inedible or unusable.
Содержание K7
Страница 2: ......
Страница 4: ......
Страница 44: ...Vacuum Packaging Machine VC999 K7 Operation Page 44 121 Art No 592 016 2008 11 26 Fig 9 7...
Страница 98: ...Vacuum Packaging Machine VC999 K7 Appendix Page 98 121 Art No 592 016 2008 11 26 15 Appendix 15 1 Program table...
Страница 99: ...Vacuum Packaging Machine VC999 K7 Appendix 2008 11 26 Art No 592 016 Page 99 121 15 2 Pneumatic diagram...
Страница 100: ...Vacuum Packaging Machine VC999 K7 Appendix Page 100 121 Art No 592 016 2008 11 26 15 3 Wiring diagrams...
Страница 101: ...Vacuum Packaging Machine VC999 K7 Appendix 2008 11 26 Art No 592 016 Page 101 121...
Страница 102: ...Vacuum Packaging Machine VC999 K7 Appendix Page 102 121 Art No 592 016 2008 11 26...
Страница 103: ...Vacuum Packaging Machine VC999 K7 Appendix 2008 11 26 Art No 592 016 Page 103 121...
Страница 104: ...Vacuum Packaging Machine VC999 K7 Appendix Page 104 121 Art No 592 016 2008 11 26...
Страница 105: ...Vacuum Packaging Machine VC999 K7 Appendix 2008 11 26 Art No 592 016 Page 105 121...
Страница 106: ...Vacuum Packaging Machine VC999 K7 Appendix Page 106 121 Art No 592 016 2008 11 26...
Страница 107: ...Vacuum Packaging Machine VC999 K7 Appendix 2008 11 26 Art No 592 016 Page 107 121...
Страница 108: ...Vacuum Packaging Machine VC999 K7 Appendix Page 108 121 Art No 592 016 2008 11 26...
Страница 109: ...Vacuum Packaging Machine VC999 K7 Appendix 2008 11 26 Art No 592 016 Page 109 121...
Страница 110: ...Vacuum Packaging Machine VC999 K7 Appendix Page 110 121 Art No 592 016 2008 11 26...
Страница 111: ...Vacuum Packaging Machine VC999 K7 Appendix 2008 11 26 Art No 592 016 Page 111 121...
Страница 112: ...Vacuum Packaging Machine VC999 K7 Appendix Page 112 121 Art No 592 016 2008 11 26...
Страница 113: ...Vacuum Packaging Machine VC999 K7 Appendix 2008 11 26 Art No 592 016 Page 113 121...
Страница 114: ...Vacuum Packaging Machine VC999 K7 Appendix Page 114 121 Art No 592 016 2008 11 26...
Страница 115: ...Vacuum Packaging Machine VC999 K7 Appendix 2008 11 26 Art No 592 016 Page 115 121...
Страница 116: ...Vacuum Packaging Machine VC999 K7 Appendix Page 116 121 Art No 592 016 2008 11 26...
Страница 117: ...Vacuum Packaging Machine VC999 K7 Appendix 2008 11 26 Art No 592 016 Page 117 121...
Страница 118: ...Vacuum Packaging Machine VC999 K7 Appendix Page 118 121 Art No 592 016 2008 11 26...